کد مقاله | کد نشریه | سال انتشار | مقاله انگلیسی | نسخه تمام متن |
---|---|---|---|---|
10146755 | 1646413 | 2019 | 29 صفحه PDF | دانلود رایگان |
عنوان انگلیسی مقاله ISI
Effect of vibratory peening on the sub-surface layer of aerospace materials Ti-6Al-4V and E-16NiCrMo13
دانلود مقاله + سفارش ترجمه
دانلود مقاله ISI انگلیسی
رایگان برای ایرانیان
موضوعات مرتبط
مهندسی و علوم پایه
سایر رشته های مهندسی
مهندسی صنعتی و تولید
پیش نمایش صفحه اول مقاله
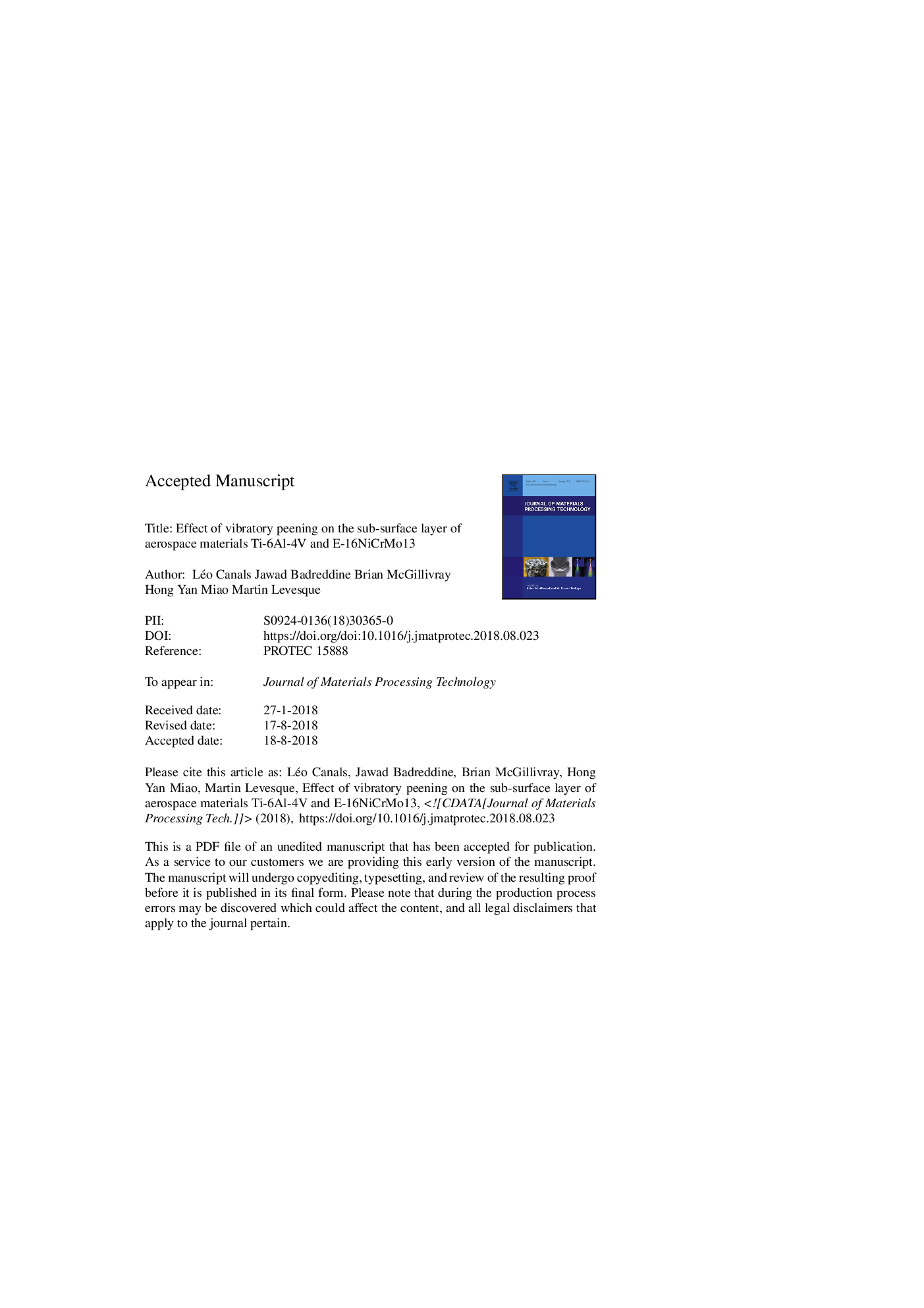
چکیده انگلیسی
Shot peening (SP) is a widely used fatigue life improvement process consisting of impacting a metallic component with high-velocity shot. The plastic deformation induces a layer of compressive residual stress and cold work which delays crack initiation and crack propagation. However, shot peeing also increases surface roughness, which acts as stress concentrator and decreases fatigue life. Vibratory finishing (VF) is a mass finishing process in which components are placed in an oscillating bowl or tub containing polishing media. The media flow around the component polishes its surface and decreases its roughness. Vibratory peening (VP) is a modified vibratory finishing process that induces compressive residual stresses comparable to those induced by shot peening and which produces a much better surface finish. In this paper, the effects of vibratory peening on surface roughness, on residual stresses, and on hardness are investigated. Two aerospace materials are assessed, titanium alloy Ti-6Al-4V and carburized steel E-16NiCrMo13. The process parameters studied are frequency, media mass and processing time. A study of Almen intensity as a function of machine parameters is carried out in order to determine the machines parameters leading to the target Almen intensities of 0.12â¯mmA, 0.18â¯mmA and 0.25â¯mmA. The influences of media mass and frequency on peening intensity are examined. The study results show that the VP process can deliver the targeted intensities consistently. Roughness measurements show that for both the materials studied, VP produces good surface roughness with a consistent average roughness value in the range of 0.3-0.4â¯Î¼m. The residual stress profiles produced by VP are comparable to those produced by conventional SP for identical Almen intensity. Compared to conventional SP, VP is found to lead to higher maximum compressive values for steel and unchanged values for titanium, with greater depth of the compressive region (+126% for steel). Hardness measurements show that VP has limited influence on a layer with depth of 70â¯Î¼m. In general, the VP process is capable of consistently producing a beneficial layer of compressive residual stress together with a good surface finish, which is an appealing avenue to improve the fatigue properties of aerospace components.
ناشر
Database: Elsevier - ScienceDirect (ساینس دایرکت)
Journal: Journal of Materials Processing Technology - Volume 264, February 2019, Pages 91-106
Journal: Journal of Materials Processing Technology - Volume 264, February 2019, Pages 91-106
نویسندگان
Léo Canals, Jawad Badreddine, Brian McGillivray, Hong Yan Miao, Martin Levesque,