کد مقاله | کد نشریه | سال انتشار | مقاله انگلیسی | نسخه تمام متن |
---|---|---|---|---|
1698947 | 1519310 | 2016 | 6 صفحه PDF | دانلود رایگان |
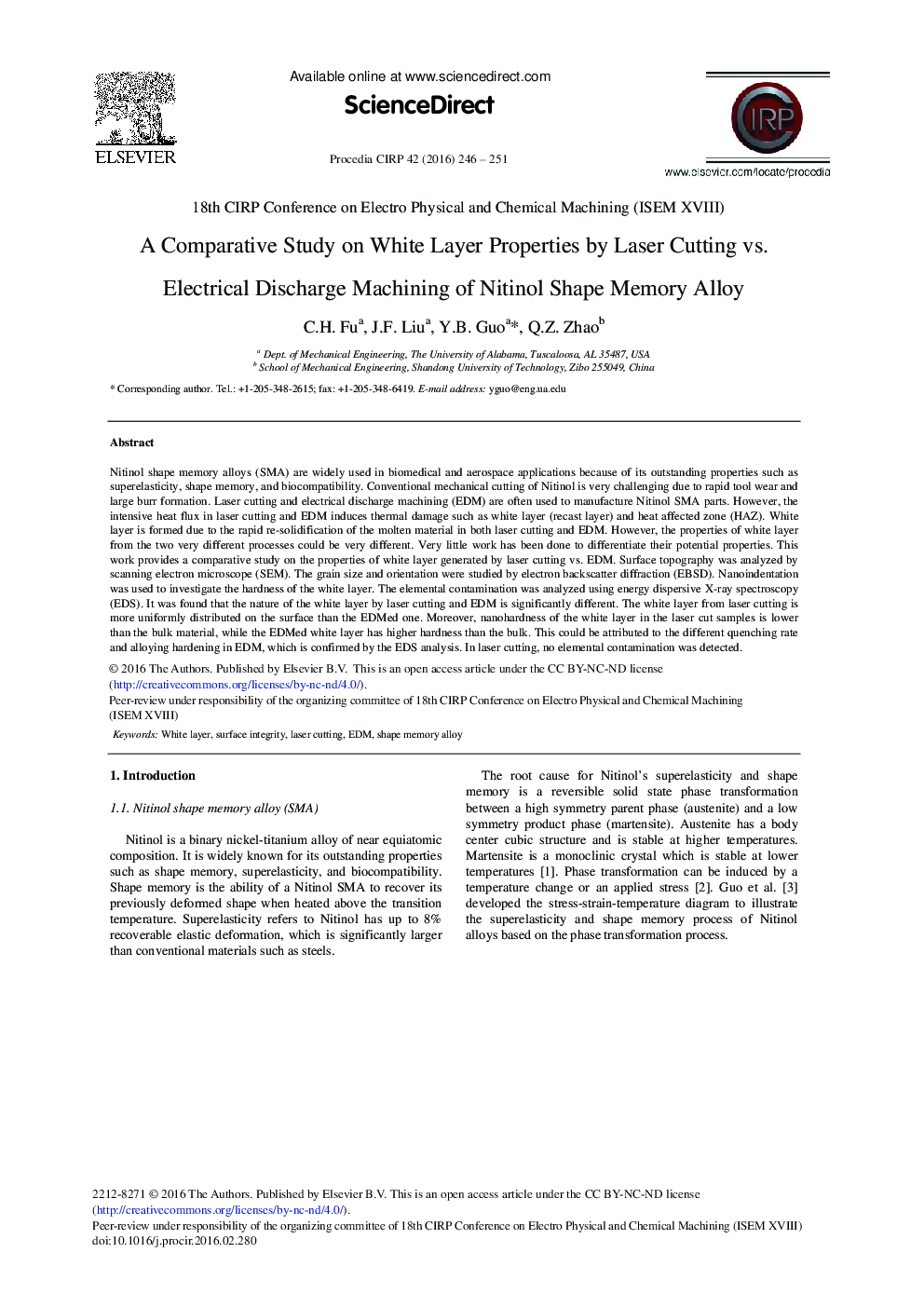
Nitinol shape memory alloys (SMA) are widely used in biomedical and aerospace applications because of its outstanding properties such as superelasticity, shape memory, and biocompatibility. Conventional mechanical cutting of Nitinol is very challenging due to rapid tool wear and large burr formation. Laser cutting and electrical discharge machining (EDM) are often used to manufacture Nitinol SMA parts. However, the intensive heat flux in laser cutting and EDM induces thermal damage such as white layer (recast layer) and heat affected zone (HAZ). White layer is formed due to the rapid re-solidification of the molten material in both laser cutting and EDM. However, the properties of white layer from the two very different processes could be very different. Very little work has been done to differentiate their potential properties. This work provides a comparative study on the properties of white layer generated by laser cutting vs. EDM. Surface topography was analyzed by scanning electron microscope (SEM). The grain size and orientation were studied by electron backscatter diffraction (EBSD). Nanoindentation was used to investigate the hardness of the white layer. The elemental contamination was analyzed using energy dispersive X-ray spectroscopy (EDS). It was found that the nature of the white layer by laser cutting and EDM is significantly different. The white layer from laser cutting is more uniformly distributed on the surface than the EDMed one. Moreover, nanohardness of the white layer in the laser cut samples is lower than the bulk material, while the EDMed white layer has higher hardness than the bulk. This could be attributed to the different quenching rate and alloying hardening in EDM, which is confirmed by the EDS analysis. In laser cutting, no elemental contamination was detected.
Journal: Procedia CIRP - Volume 42, 2016, Pages 246-251