کد مقاله | کد نشریه | سال انتشار | مقاله انگلیسی | نسخه تمام متن |
---|---|---|---|---|
297858 | 511769 | 2011 | 10 صفحه PDF | دانلود رایگان |
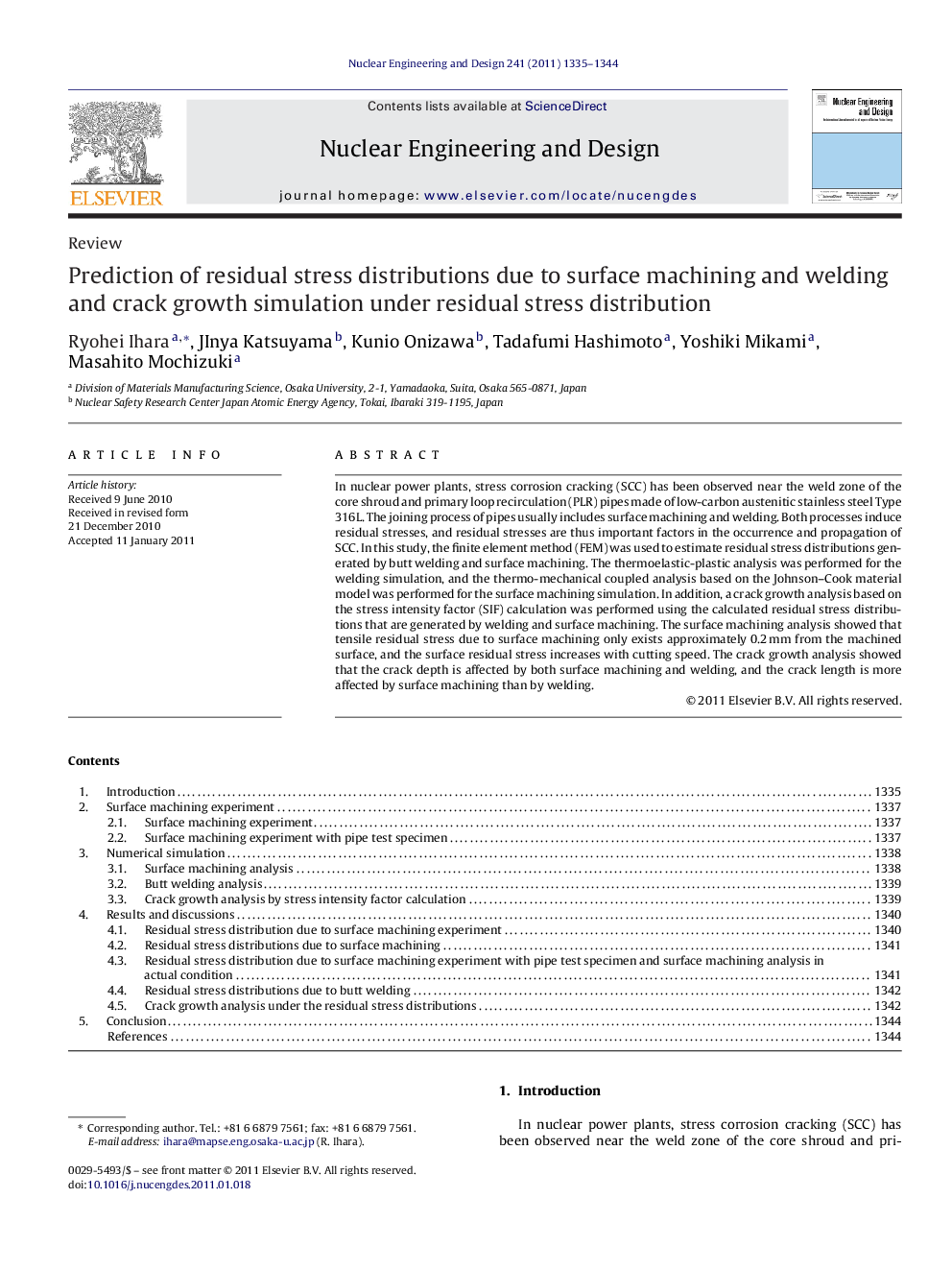
In nuclear power plants, stress corrosion cracking (SCC) has been observed near the weld zone of the core shroud and primary loop recirculation (PLR) pipes made of low-carbon austenitic stainless steel Type 316L. The joining process of pipes usually includes surface machining and welding. Both processes induce residual stresses, and residual stresses are thus important factors in the occurrence and propagation of SCC. In this study, the finite element method (FEM) was used to estimate residual stress distributions generated by butt welding and surface machining. The thermoelastic-plastic analysis was performed for the welding simulation, and the thermo-mechanical coupled analysis based on the Johnson–Cook material model was performed for the surface machining simulation. In addition, a crack growth analysis based on the stress intensity factor (SIF) calculation was performed using the calculated residual stress distributions that are generated by welding and surface machining. The surface machining analysis showed that tensile residual stress due to surface machining only exists approximately 0.2 mm from the machined surface, and the surface residual stress increases with cutting speed. The crack growth analysis showed that the crack depth is affected by both surface machining and welding, and the crack length is more affected by surface machining than by welding.
Research highlights
► Residual stress distributions due to welding and machining are evaluated by XRD and FEM.
► Residual stress due to machining shows higher tensile stress than welding near the surface.
► Crack growth analysis is performed using calculated residual stress.
► Crack growth result is affected machining rather than welding.
► Machining is an important factor for crack growth.
Journal: Nuclear Engineering and Design - Volume 241, Issue 5, May 2011, Pages 1335–1344