کد مقاله | کد نشریه | سال انتشار | مقاله انگلیسی | نسخه تمام متن |
---|---|---|---|---|
440845 | 691290 | 2011 | 13 صفحه PDF | دانلود رایگان |
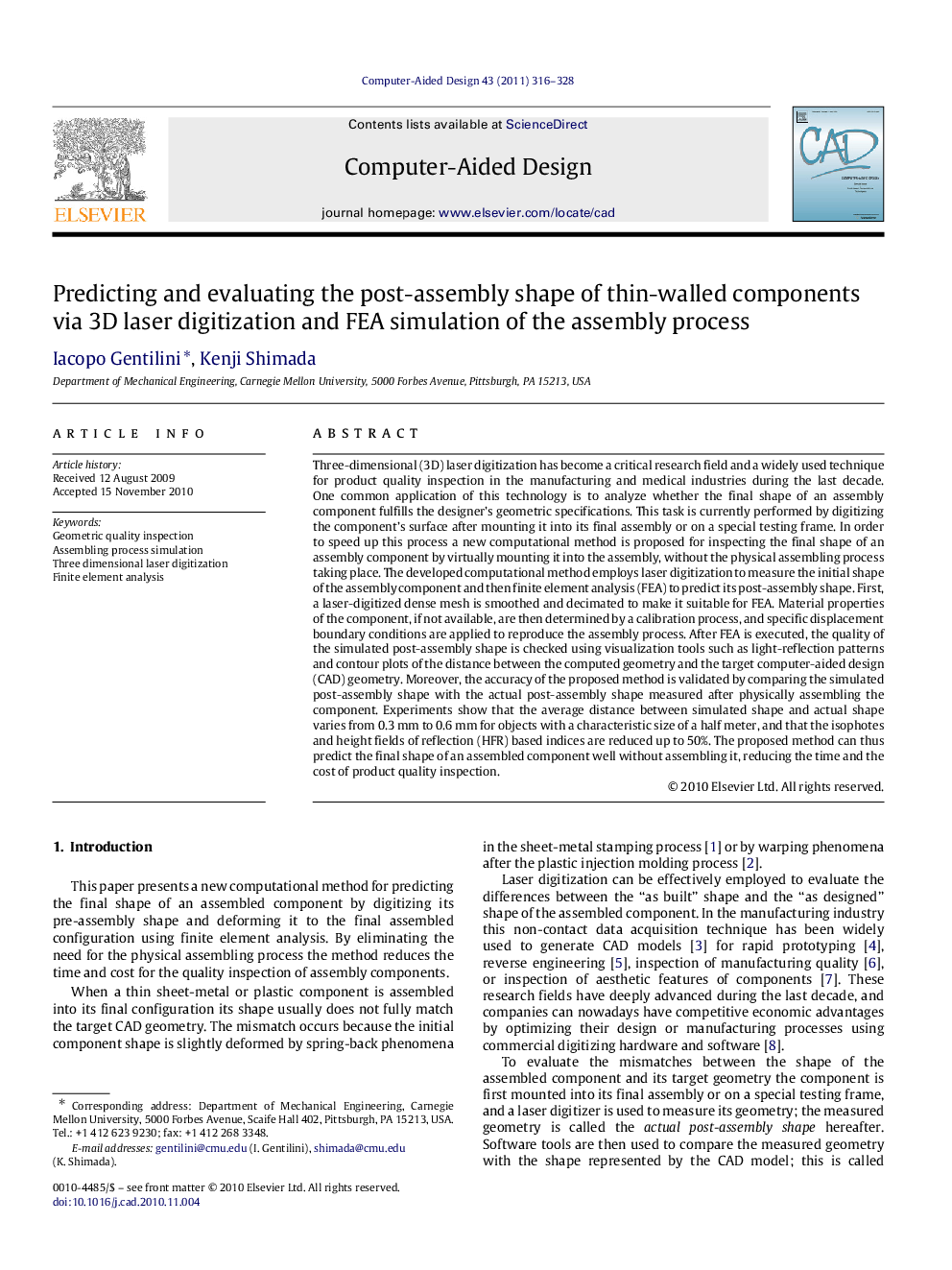
Three-dimensional (3D) laser digitization has become a critical research field and a widely used technique for product quality inspection in the manufacturing and medical industries during the last decade. One common application of this technology is to analyze whether the final shape of an assembly component fulfills the designer’s geometric specifications. This task is currently performed by digitizing the component’s surface after mounting it into its final assembly or on a special testing frame. In order to speed up this process a new computational method is proposed for inspecting the final shape of an assembly component by virtually mounting it into the assembly, without the physical assembling process taking place. The developed computational method employs laser digitization to measure the initial shape of the assembly component and then finite element analysis (FEA) to predict its post-assembly shape. First, a laser-digitized dense mesh is smoothed and decimated to make it suitable for FEA. Material properties of the component, if not available, are then determined by a calibration process, and specific displacement boundary conditions are applied to reproduce the assembly process. After FEA is executed, the quality of the simulated post-assembly shape is checked using visualization tools such as light-reflection patterns and contour plots of the distance between the computed geometry and the target computer-aided design (CAD) geometry. Moreover, the accuracy of the proposed method is validated by comparing the simulated post-assembly shape with the actual post-assembly shape measured after physically assembling the component. Experiments show that the average distance between simulated shape and actual shape varies from 0.3 mm to 0.6 mm for objects with a characteristic size of a half meter, and that the isophotes and height fields of reflection (HFR) based indices are reduced up to 50%. The proposed method can thus predict the final shape of an assembled component well without assembling it, reducing the time and the cost of product quality inspection.
Figure optionsDownload as PowerPoint slideResearch highlights
► Shape prediction of thin-walled assembly components via FEA and 3D laser digitization.
► No need for the physical assembling process to take place in future practice.
► Shape comparison by evaluating average distance between actual and predicted meshes.
► Geometric quality inspection by evaluating height fields of reflection based indices.
Journal: Computer-Aided Design - Volume 43, Issue 3, March 2011, Pages 316–328