کد مقاله | کد نشریه | سال انتشار | مقاله انگلیسی | نسخه تمام متن |
---|---|---|---|---|
803072 | 1467769 | 2013 | 8 صفحه PDF | دانلود رایگان |
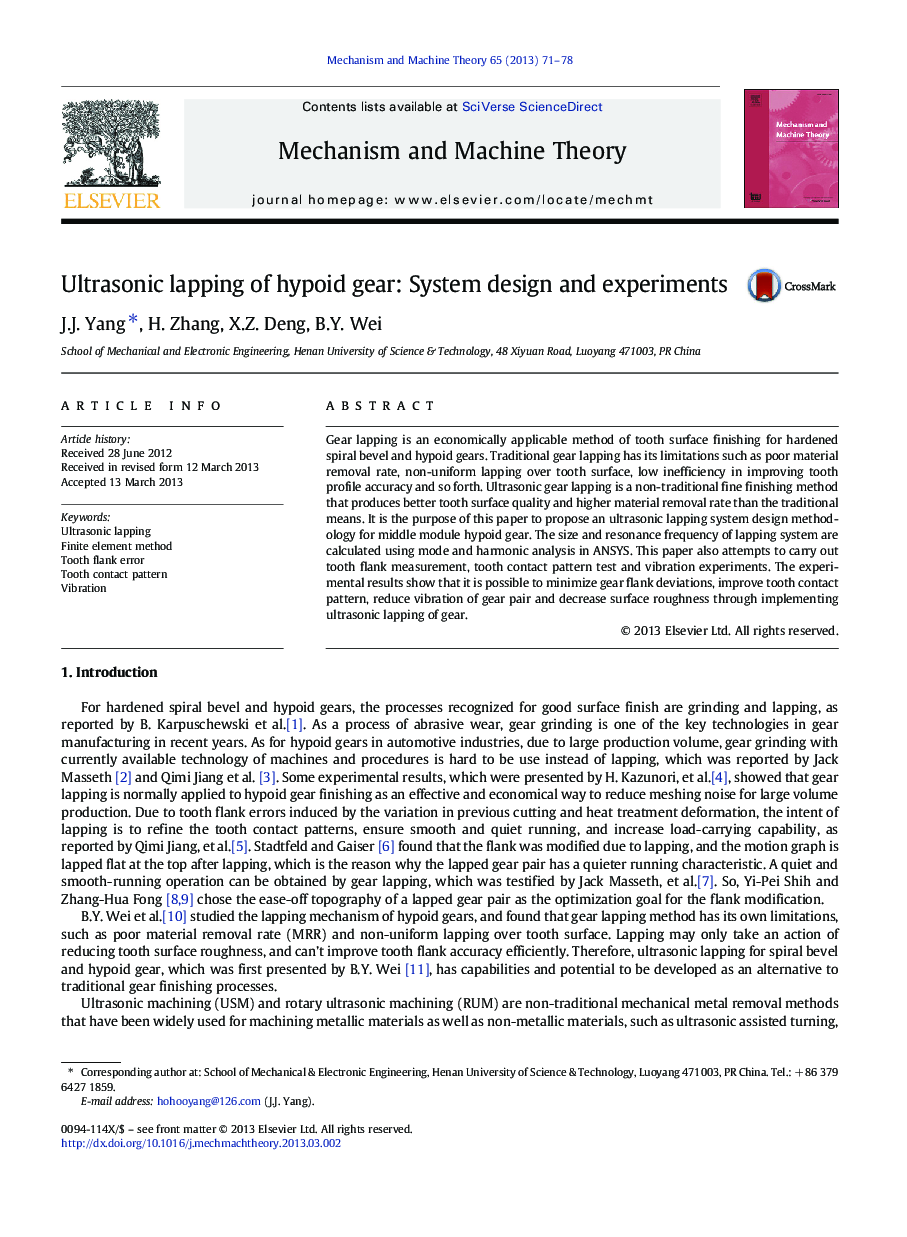
• The design method of ultrasonic lapping system for middle module hypoid gear.
• The tooth flank deviations were reduced after ultrasonic lapping. Compared with traditional gear lapping, the lapping effect is better.
• Ultrasonic gear lapping produced better contact patterns of tooth surface.
• The acceleration amplitude was reduced after ultrasonic gear lapping. Compared with traditional gear lapping, the surface quality of gear is improved.
Gear lapping is an economically applicable method of tooth surface finishing for hardened spiral bevel and hypoid gears. Traditional gear lapping has its limitations such as poor material removal rate, non-uniform lapping over tooth surface, low inefficiency in improving tooth profile accuracy and so forth. Ultrasonic gear lapping is a non-traditional fine finishing method that produces better tooth surface quality and higher material removal rate than the traditional means. It is the purpose of this paper to propose an ultrasonic lapping system design methodology for middle module hypoid gear. The size and resonance frequency of lapping system are calculated using mode and harmonic analysis in ANSYS. This paper also attempts to carry out tooth flank measurement, tooth contact pattern test and vibration experiments. The experimental results show that it is possible to minimize gear flank deviations, improve tooth contact pattern, reduce vibration of gear pair and decrease surface roughness through implementing ultrasonic lapping of gear.
The basic components of ULG system include ultrasonic generator, resonance transducer, ultrasonic horn and pinion, as is shown in Fig. 1.Ultrasonic generator is used to create ultrasonic frequency electric current. The resonance transducer acts as the source of mechanical oscillations, transforming the electric power received from the ultrasonic generator into mechanical vibration. In the present work, the 4 pieces of PZT-4 piezoelectric ceramics chosen as the transducer, are pressed together tightly by a prestressed bolt. However, the vibration amplitude of the transducer is not enough to realize gear lapping process. To overcome this disadvantage, a wave-guide focusing device known as a horn fitted onto the end of the transducer, is used to amplify the vibration amplitude generated by transducer so that the amplitude at the gear surface is enough for gear lapping. The conical horn shape has been taken as a domain with a hole at the tip for the purpose of fixing pinion. The pinion is fixed to the horn by the screw at the end of pinion axis, and excited by the ultrasonic vibration in the way of torsional or longitudinal vibration to increase the lapping efficiency. The displacement curve of longitudinal vibration (dash line in Fig. 1) is predesigned. Three nodal planes exist in ULG set-up, at which the vibration displacement is zero (shown in Fig. 1).Figure optionsDownload as PowerPoint slide
Journal: Mechanism and Machine Theory - Volume 65, July 2013, Pages 71–78