کد مقاله | کد نشریه | سال انتشار | مقاله انگلیسی | نسخه تمام متن |
---|---|---|---|---|
804426 | 1467843 | 2016 | 20 صفحه PDF | دانلود رایگان |
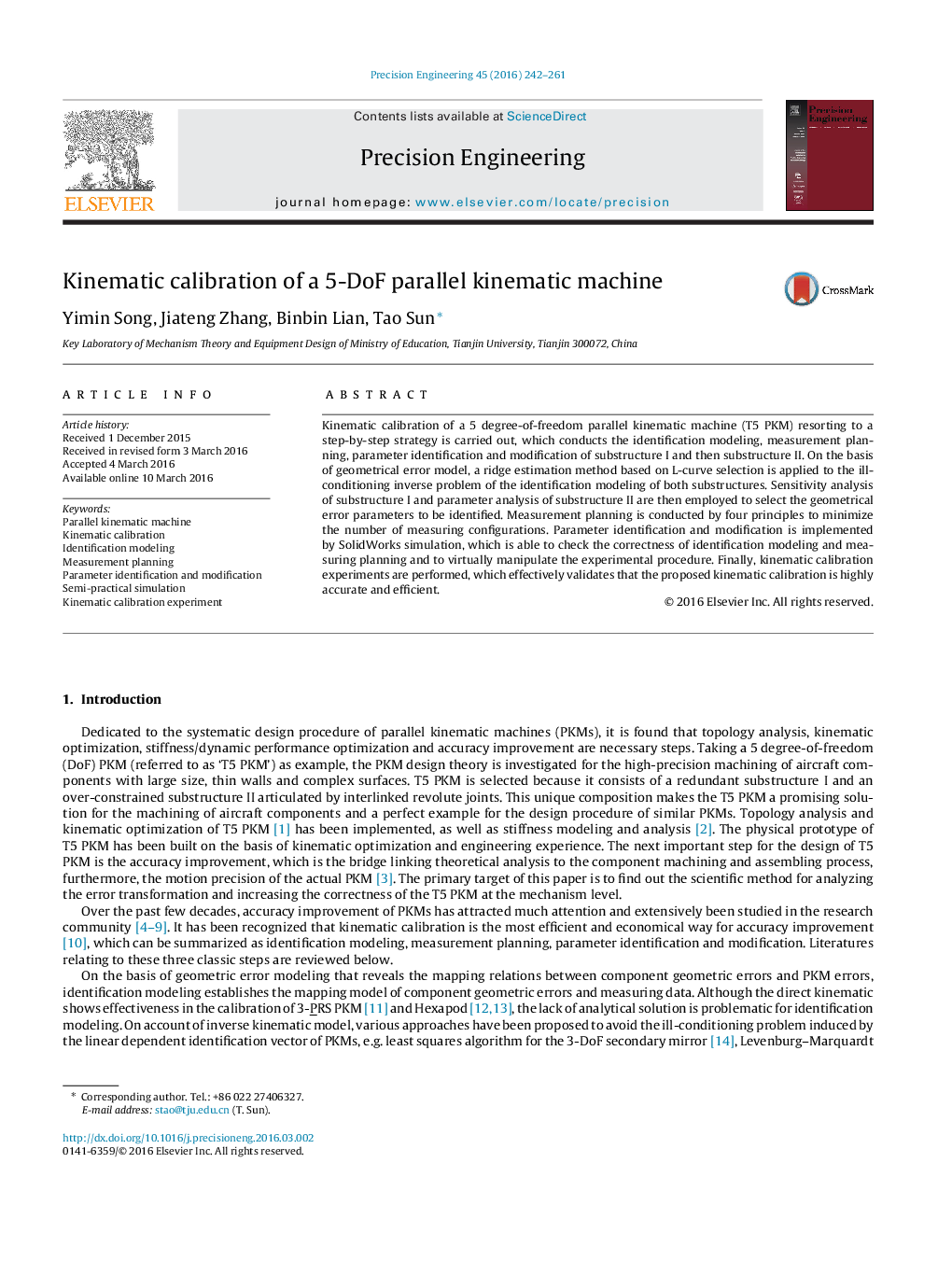
• Ridge estimation and L-curve selection are adopted in identification modeling.
• Sensitivity analysis and parameter analysis are conducted for reducing parameters.
• Four principles are proposed for the external measurement planning.
• Semi-practical verification method by simulation in SolidWorks was implemented.
• Kinematic calibration experiment and verification was executed.
Kinematic calibration of a 5 degree-of-freedom parallel kinematic machine (T5 PKM) resorting to a step-by-step strategy is carried out, which conducts the identification modeling, measurement planning, parameter identification and modification of substructure I and then substructure II. On the basis of geometrical error model, a ridge estimation method based on L-curve selection is applied to the ill-conditioning inverse problem of the identification modeling of both substructures. Sensitivity analysis of substructure I and parameter analysis of substructure II are then employed to select the geometrical error parameters to be identified. Measurement planning is conducted by four principles to minimize the number of measuring configurations. Parameter identification and modification is implemented by SolidWorks simulation, which is able to check the correctness of identification modeling and measuring planning and to virtually manipulate the experimental procedure. Finally, kinematic calibration experiments are performed, which effectively validates that the proposed kinematic calibration is highly accurate and efficient.
Journal: Precision Engineering - Volume 45, July 2016, Pages 242–261