کد مقاله | کد نشریه | سال انتشار | مقاله انگلیسی | نسخه تمام متن |
---|---|---|---|---|
831630 | 908108 | 2011 | 7 صفحه PDF | دانلود رایگان |
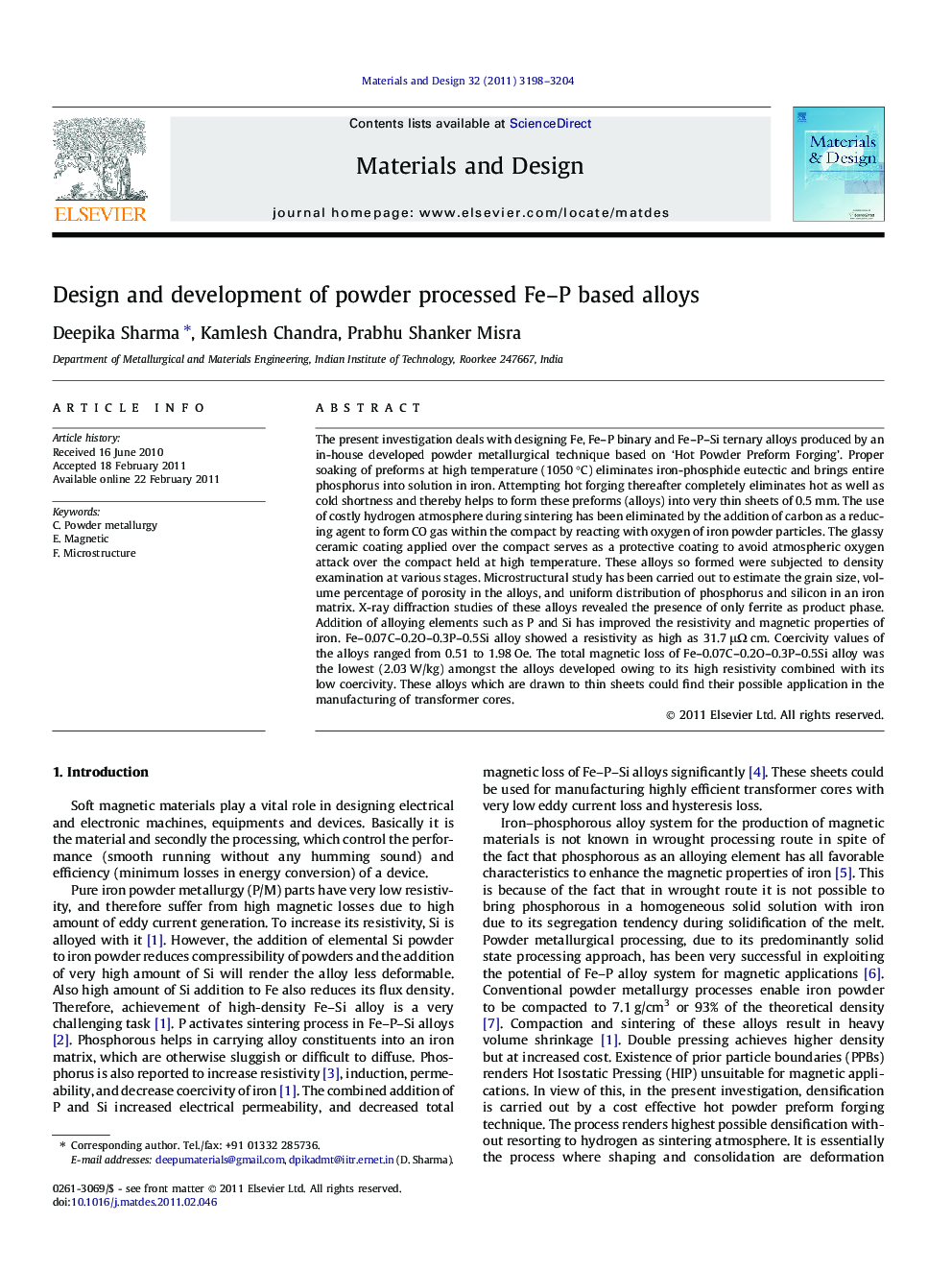
The present investigation deals with designing Fe, Fe–P binary and Fe–P–Si ternary alloys produced by an in-house developed powder metallurgical technique based on ‘Hot Powder Preform Forging’. Proper soaking of preforms at high temperature (1050 °C) eliminates iron-phosphide eutectic and brings entire phosphorus into solution in iron. Attempting hot forging thereafter completely eliminates hot as well as cold shortness and thereby helps to form these preforms (alloys) into very thin sheets of 0.5 mm. The use of costly hydrogen atmosphere during sintering has been eliminated by the addition of carbon as a reducing agent to form CO gas within the compact by reacting with oxygen of iron powder particles. The glassy ceramic coating applied over the compact serves as a protective coating to avoid atmospheric oxygen attack over the compact held at high temperature. These alloys so formed were subjected to density examination at various stages. Microstructural study has been carried out to estimate the grain size, volume percentage of porosity in the alloys, and uniform distribution of phosphorus and silicon in an iron matrix. X-ray diffraction studies of these alloys revealed the presence of only ferrite as product phase. Addition of alloying elements such as P and Si has improved the resistivity and magnetic properties of iron. Fe–0.07C–0.2O–0.3P–0.5Si alloy showed a resistivity as high as 31.7 μΩ cm. Coercivity values of the alloys ranged from 0.51 to 1.98 Oe. The total magnetic loss of Fe–0.07C–0.2O–0.3P–0.5Si alloy was the lowest (2.03 W/kg) amongst the alloys developed owing to its high resistivity combined with its low coercivity. These alloys which are drawn to thin sheets could find their possible application in the manufacturing of transformer cores.
► The forming technique does not require any binder. Thus the system remains uncontaminated.
► The use of ceramic protective coating eliminates the need of hydrogen protective atmosphere during heating.
► Combined application of glassy ceramic coating and use of graphite as a reducing agent has lead to economy in P/M processing.
► The technology developed in the present investigation showed very low coercivity and total loss values.
Journal: Materials & Design - Volume 32, Issue 6, June 2011, Pages 3198–3204