کد مقاله | کد نشریه | سال انتشار | مقاله انگلیسی | نسخه تمام متن |
---|---|---|---|---|
144295 | 438927 | 2012 | 7 صفحه PDF | دانلود رایگان |
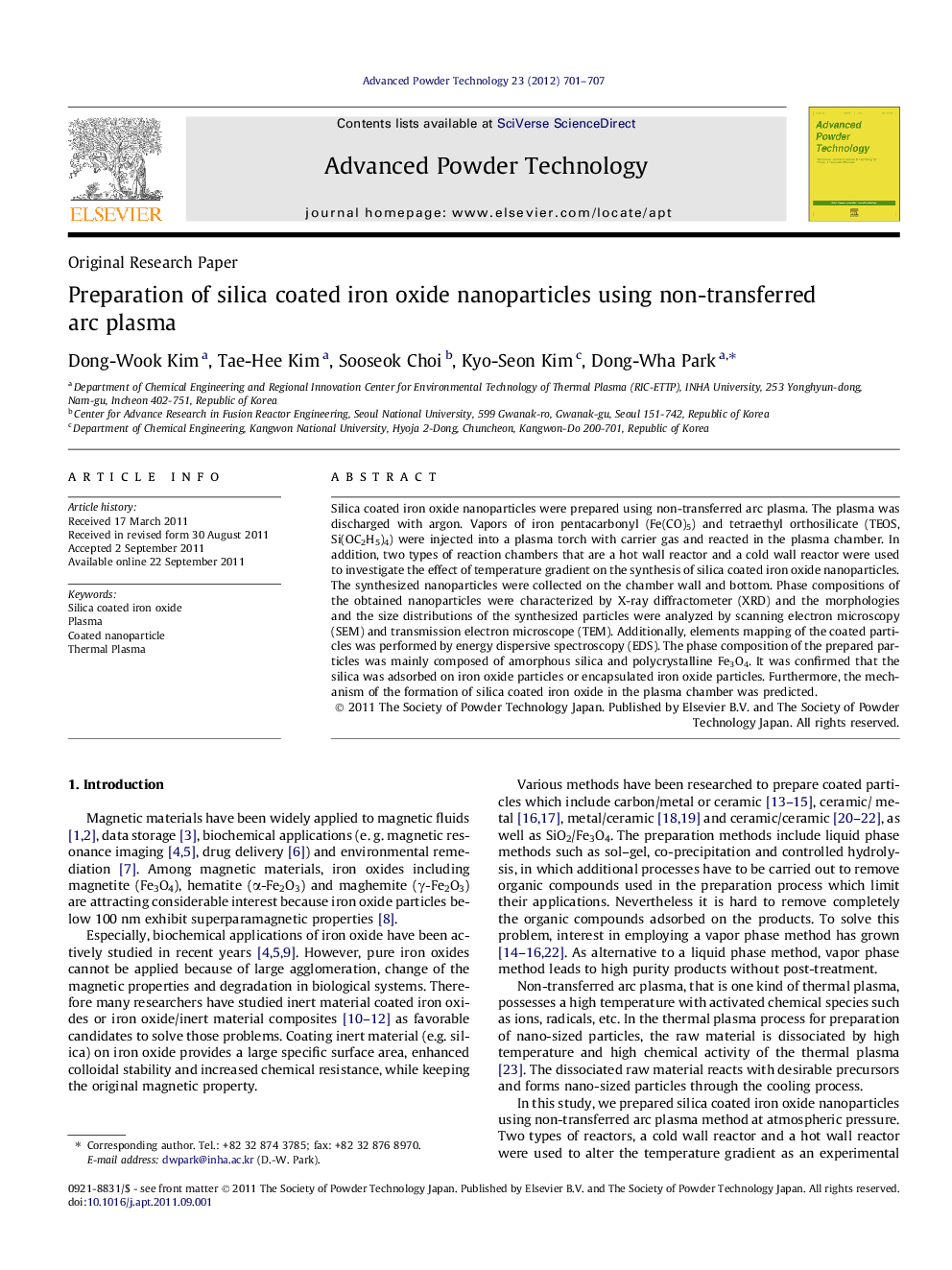
Silica coated iron oxide nanoparticles were prepared using non-transferred arc plasma. The plasma was discharged with argon. Vapors of iron pentacarbonyl (Fe(CO)5) and tetraethyl orthosilicate (TEOS, Si(OC2H5)4) were injected into a plasma torch with carrier gas and reacted in the plasma chamber. In addition, two types of reaction chambers that are a hot wall reactor and a cold wall reactor were used to investigate the effect of temperature gradient on the synthesis of silica coated iron oxide nanoparticles. The synthesized nanoparticles were collected on the chamber wall and bottom. Phase compositions of the obtained nanoparticles were characterized by X-ray diffractometer (XRD) and the morphologies and the size distributions of the synthesized particles were analyzed by scanning electron microscopy (SEM) and transmission electron microscope (TEM). Additionally, elements mapping of the coated particles was performed by energy dispersive spectroscopy (EDS). The phase composition of the prepared particles was mainly composed of amorphous silica and polycrystalline Fe3O4. It was confirmed that the silica was adsorbed on iron oxide particles or encapsulated iron oxide particles. Furthermore, the mechanism of the formation of silica coated iron oxide in the plasma chamber was predicted.
Silica/iron oxide nanocomposites were prepared using thermal plasma. Fe(CO)5 and TEOS as precursors were vaporized and then injected into plasma jet. The product contained three types of particles were observed in products; silica coated iron oxide spheres (>100 nm), iron oxide particles buried in amorphous layer (<30 nm) and agglomerated iron oxide spheres.Figure optionsDownload as PowerPoint slideHighlights
► Silica coated iron oxide nanoparticles were synthesized by thermal plasma.
► The core was iron oxide and the external layer was amorphous silica.
► Hot wall reactor was used to investigate the effect of the temperature gradient.
► The lower temperature gradient in the hot wall reactor confined the particle growth.
Journal: Advanced Powder Technology - Volume 23, Issue 6, November 2012, Pages 701–707