کد مقاله | کد نشریه | سال انتشار | مقاله انگلیسی | نسخه تمام متن |
---|---|---|---|---|
155873 | 456913 | 2012 | 9 صفحه PDF | دانلود رایگان |
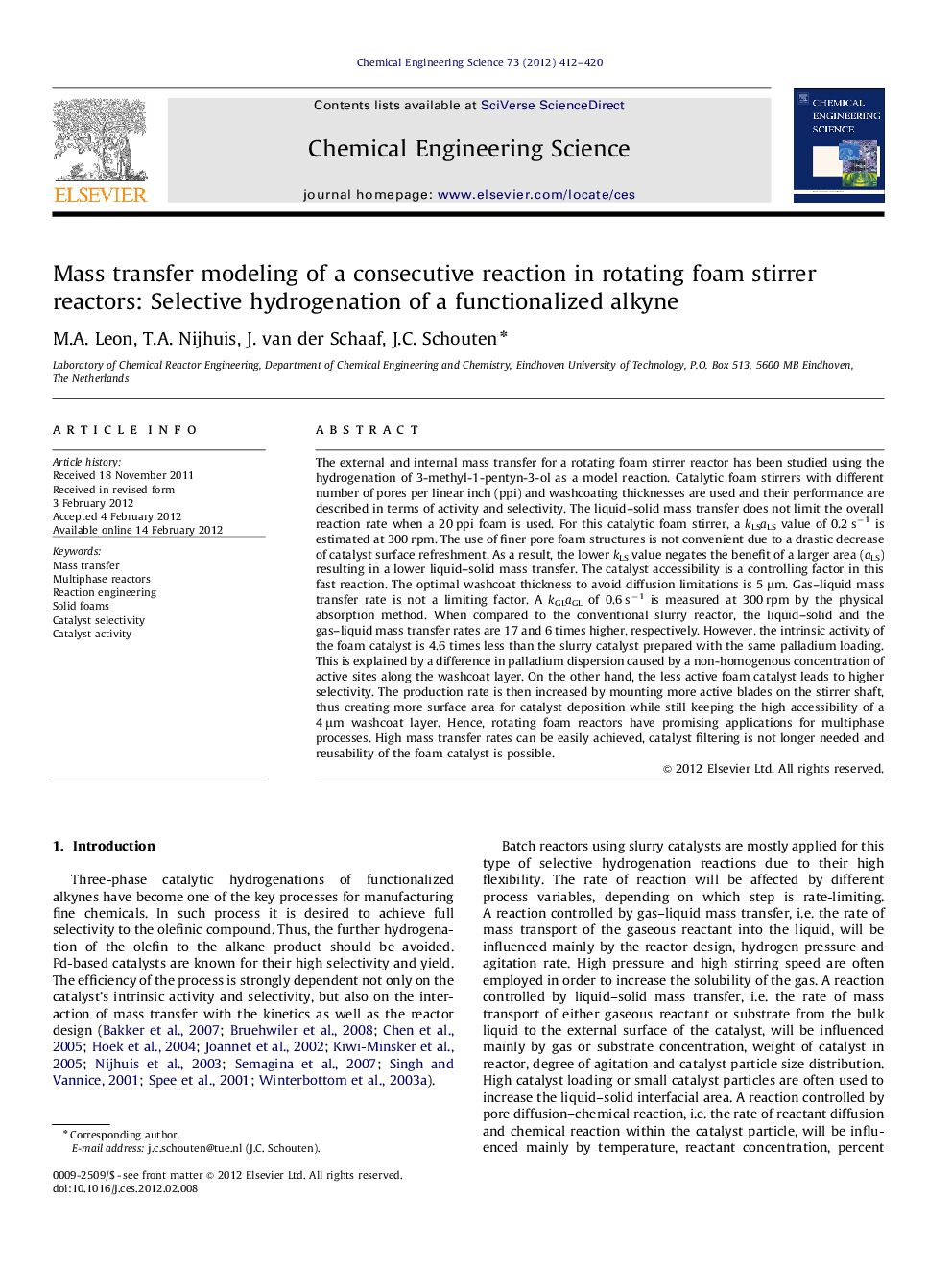
The external and internal mass transfer for a rotating foam stirrer reactor has been studied using the hydrogenation of 3-methyl-1-pentyn-3-ol as a model reaction. Catalytic foam stirrers with different number of pores per linear inch (ppi) and washcoating thicknesses are used and their performance are described in terms of activity and selectivity. The liquid–solid mass transfer does not limit the overall reaction rate when a 20 ppi foam is used. For this catalytic foam stirrer, a kLSaLS value of 0.2 s−1 is estimated at 300 rpm. The use of finer pore foam structures is not convenient due to a drastic decrease of catalyst surface refreshment. As a result, the lower kLS value negates the benefit of a larger area (aLS) resulting in a lower liquid–solid mass transfer. The catalyst accessibility is a controlling factor in this fast reaction. The optimal washcoat thickness to avoid diffusion limitations is 5 μm. Gas–liquid mass transfer rate is not a limiting factor. A kGLaGL of 0.6 s−1 is measured at 300 rpm by the physical absorption method. When compared to the conventional slurry reactor, the liquid–solid and the gas–liquid mass transfer rates are 17 and 6 times higher, respectively. However, the intrinsic activity of the foam catalyst is 4.6 times less than the slurry catalyst prepared with the same palladium loading. This is explained by a difference in palladium dispersion caused by a non-homogenous concentration of active sites along the washcoat layer. On the other hand, the less active foam catalyst leads to higher selectivity. The production rate is then increased by mounting more active blades on the stirrer shaft, thus creating more surface area for catalyst deposition while still keeping the high accessibility of a 4 μm washcoat layer. Hence, rotating foam reactors have promising applications for multiphase processes. High mass transfer rates can be easily achieved, catalyst filtering is not longer needed and reusability of the foam catalyst is possible.
► Rotating foam stirrer reactors have promising applications for multiphase processes.
► Higher mass transfer rates than in a slurry reactor can be achieved.
► Enhanced liquid–solid mass transfer due to the fast catalyst surface refreshment.
► Better gas–liquid mass transfer thanks to the formation of finely dispersed bubbles.
► Catalyst filtering is not needed and reusability of the foam catalyst is possible.
Journal: Chemical Engineering Science - Volume 73, 7 May 2012, Pages 412–420