کد مقاله | کد نشریه | سال انتشار | مقاله انگلیسی | نسخه تمام متن |
---|---|---|---|---|
1751149 | 1018409 | 2011 | 5 صفحه PDF | دانلود رایگان |
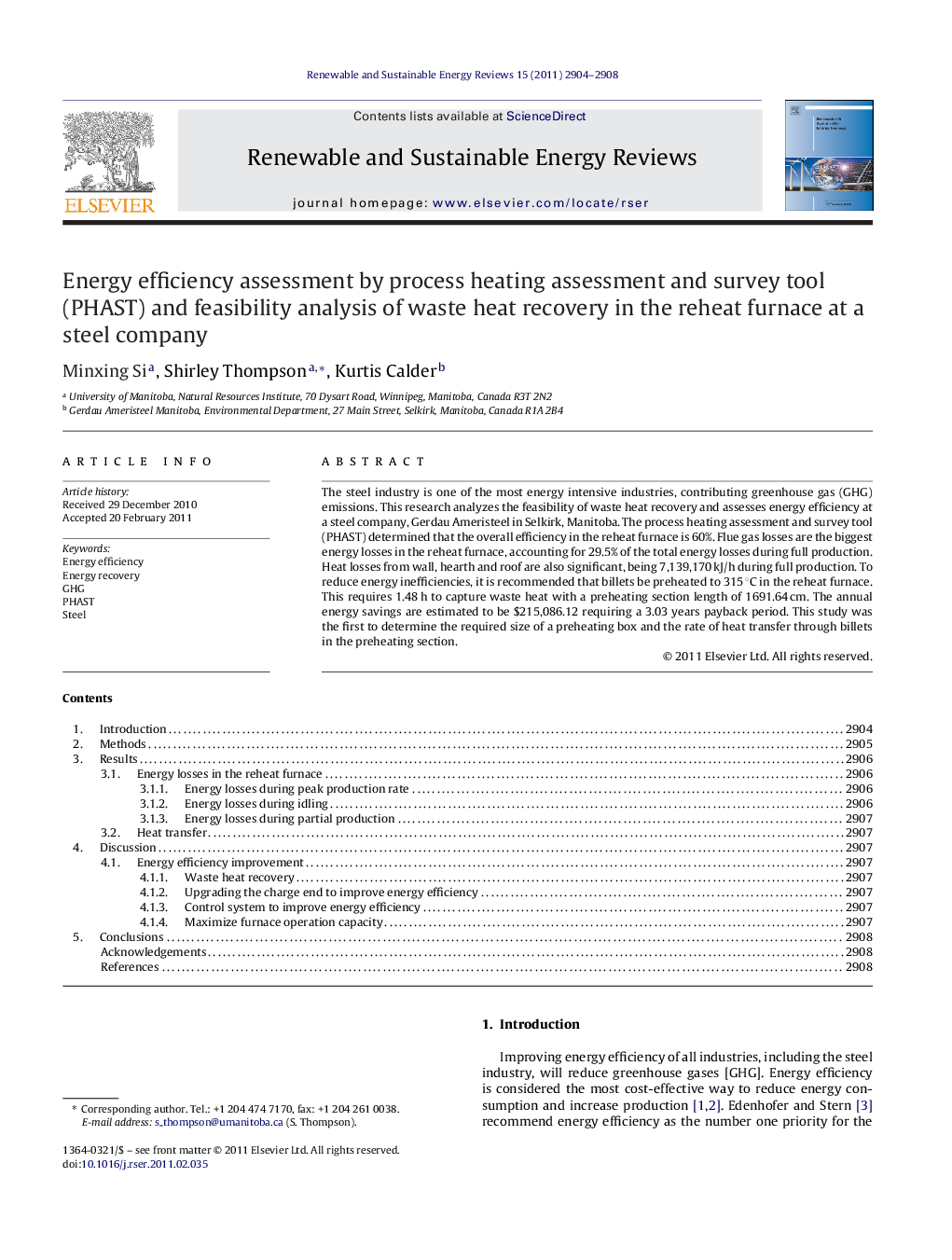
The steel industry is one of the most energy intensive industries, contributing greenhouse gas (GHG) emissions. This research analyzes the feasibility of waste heat recovery and assesses energy efficiency at a steel company, Gerdau Ameristeel in Selkirk, Manitoba. The process heating assessment and survey tool (PHAST) determined that the overall efficiency in the reheat furnace is 60%. Flue gas losses are the biggest energy losses in the reheat furnace, accounting for 29.5% of the total energy losses during full production. Heat losses from wall, hearth and roof are also significant, being 7,139,170 kJ/h during full production. To reduce energy inefficiencies, it is recommended that billets be preheated to 315 °C in the reheat furnace. This requires 1.48 h to capture waste heat with a preheating section length of 1691.64 cm. The annual energy savings are estimated to be $215,086.12 requiring a 3.03 years payback period. This study was the first to determine the required size of a preheating box and the rate of heat transfer through billets in the preheating section.
Journal: Renewable and Sustainable Energy Reviews - Volume 15, Issue 6, August 2011, Pages 2904–2908