کد مقاله | کد نشریه | سال انتشار | مقاله انگلیسی | نسخه تمام متن |
---|---|---|---|---|
1798313 | 1524818 | 2016 | 7 صفحه PDF | دانلود رایگان |
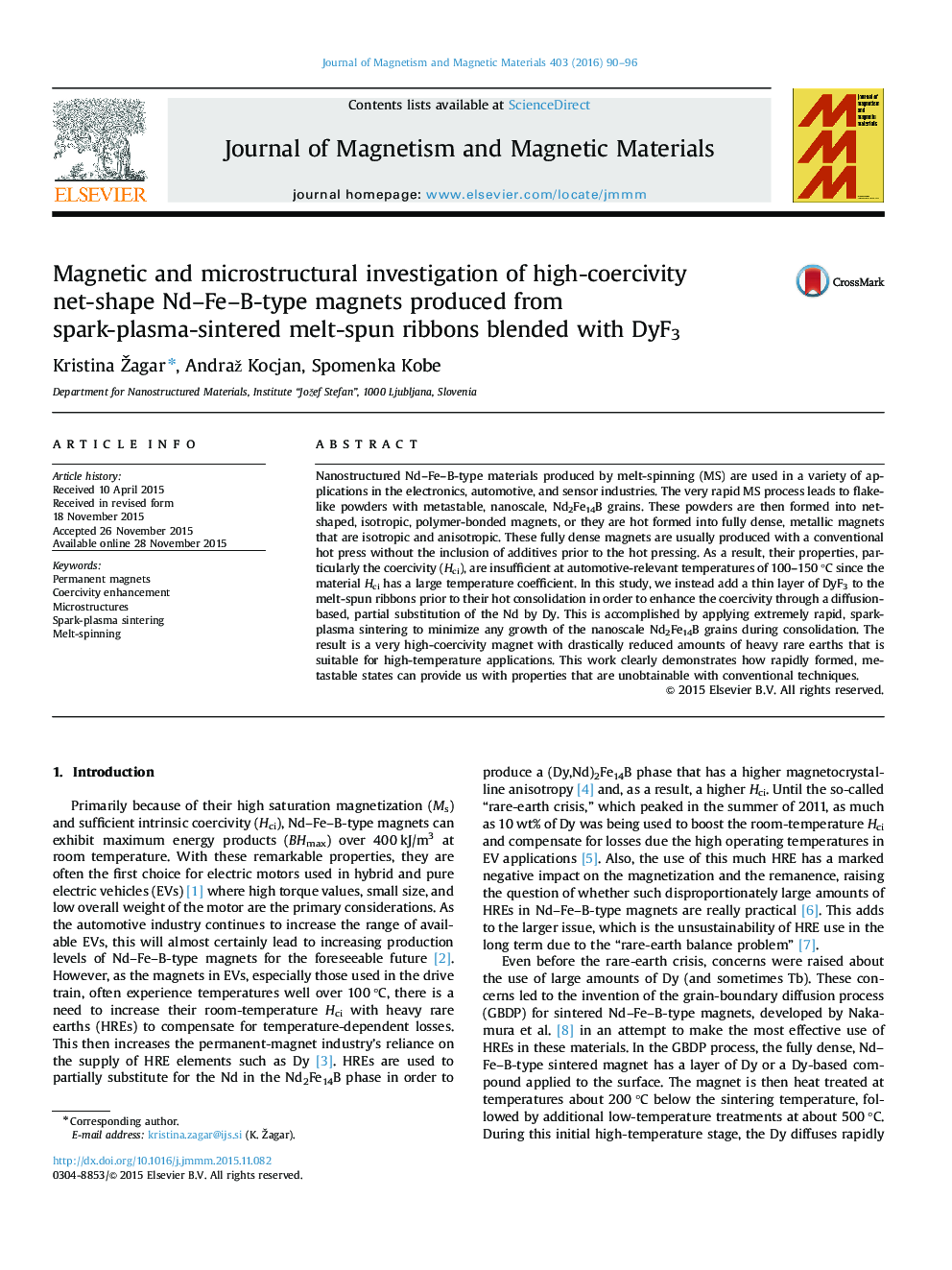
• We produced high coercivity magnets with drastically reduced amounts of HRE.
• Microstructural analysis was conducted of the “free” and “wheel” side of Dy-treated Nd2Fe14B ribbons.
• Dy-diffusion mechanism into ribbons depending on processing parameters is shown.
Nanostructured Nd–Fe–B-type materials produced by melt-spinning (MS) are used in a variety of applications in the electronics, automotive, and sensor industries. The very rapid MS process leads to flake-like powders with metastable, nanoscale, Nd2Fe14B grains. These powders are then formed into net-shaped, isotropic, polymer-bonded magnets, or they are hot formed into fully dense, metallic magnets that are isotropic and anisotropic. These fully dense magnets are usually produced with a conventional hot press without the inclusion of additives prior to the hot pressing. As a result, their properties, particularly the coercivity (Hci), are insufficient at automotive-relevant temperatures of 100–150 °C since the material Hci has a large temperature coefficient. In this study, we instead add a thin layer of DyF3 to the melt-spun ribbons prior to their hot consolidation in order to enhance the coercivity through a diffusion-based, partial substitution of the Nd by Dy. This is accomplished by applying extremely rapid, spark-plasma sintering to minimize any growth of the nanoscale Nd2Fe14B grains during consolidation. The result is a very high-coercivity magnet with drastically reduced amounts of heavy rare earths that is suitable for high-temperature applications. This work clearly demonstrates how rapidly formed, metastable states can provide us with properties that are unobtainable with conventional techniques.
Figure optionsDownload as PowerPoint slide
Journal: Journal of Magnetism and Magnetic Materials - Volume 403, 1 April 2016, Pages 90–96