کد مقاله | کد نشریه | سال انتشار | مقاله انگلیسی | نسخه تمام متن |
---|---|---|---|---|
235964 | 465654 | 2014 | 10 صفحه PDF | دانلود رایگان |
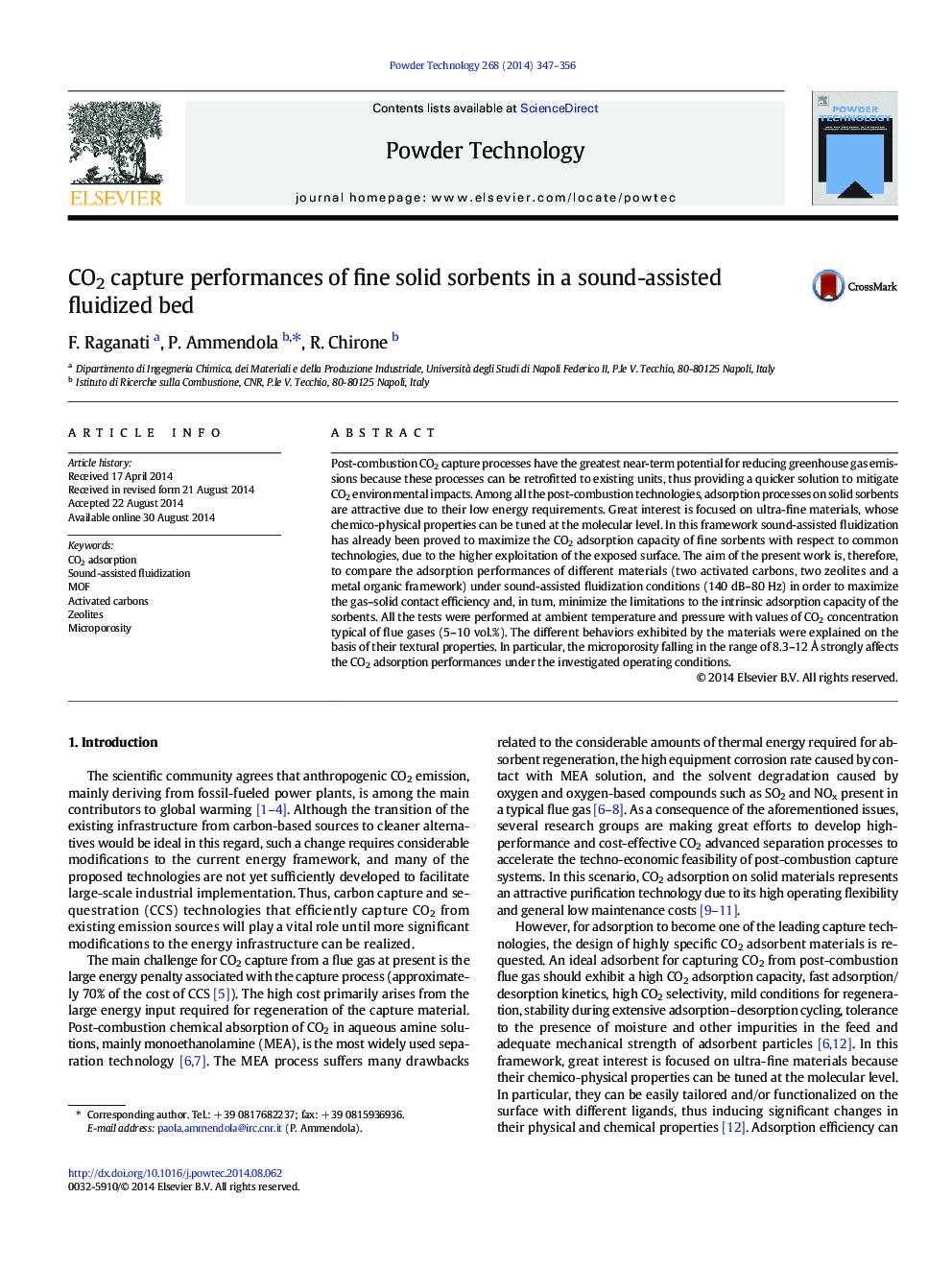
• Sound-assisted fluidization is able to maximize fine material CO2 adsorption capacity.
• HKUST-1 has the best adsorption capacity, activated carbons and the zeolites follow.
• No correlation exists between adsorption capacity and BET or total pore volume.
• Adsorption process is mainly affected by a specific microporosity (8.3–12 Å).
• Larger micropores or mesopores are not relevant for post-combustion CO2 capture.
Post-combustion CO2 capture processes have the greatest near-term potential for reducing greenhouse gas emissions because these processes can be retrofitted to existing units, thus providing a quicker solution to mitigate CO2 environmental impacts. Among all the post-combustion technologies, adsorption processes on solid sorbents are attractive due to their low energy requirements. Great interest is focused on ultra-fine materials, whose chemico-physical properties can be tuned at the molecular level. In this framework sound-assisted fluidization has already been proved to maximize the CO2 adsorption capacity of fine sorbents with respect to common technologies, due to the higher exploitation of the exposed surface. The aim of the present work is, therefore, to compare the adsorption performances of different materials (two activated carbons, two zeolites and a metal organic framework) under sound-assisted fluidization conditions (140 dB–80 Hz) in order to maximize the gas–solid contact efficiency and, in turn, minimize the limitations to the intrinsic adsorption capacity of the sorbents. All the tests were performed at ambient temperature and pressure with values of CO2 concentration typical of flue gases (5–10 vol.%). The different behaviors exhibited by the materials were explained on the basis of their textural properties. In particular, the microporosity falling in the range of 8.3–12 Å strongly affects the CO2 adsorption performances under the investigated operating conditions.
Figure optionsDownload as PowerPoint slide
Journal: Powder Technology - Volume 268, December 2014, Pages 347–356