کد مقاله | کد نشریه | سال انتشار | مقاله انگلیسی | نسخه تمام متن |
---|---|---|---|---|
236674 | 465682 | 2013 | 12 صفحه PDF | دانلود رایگان |
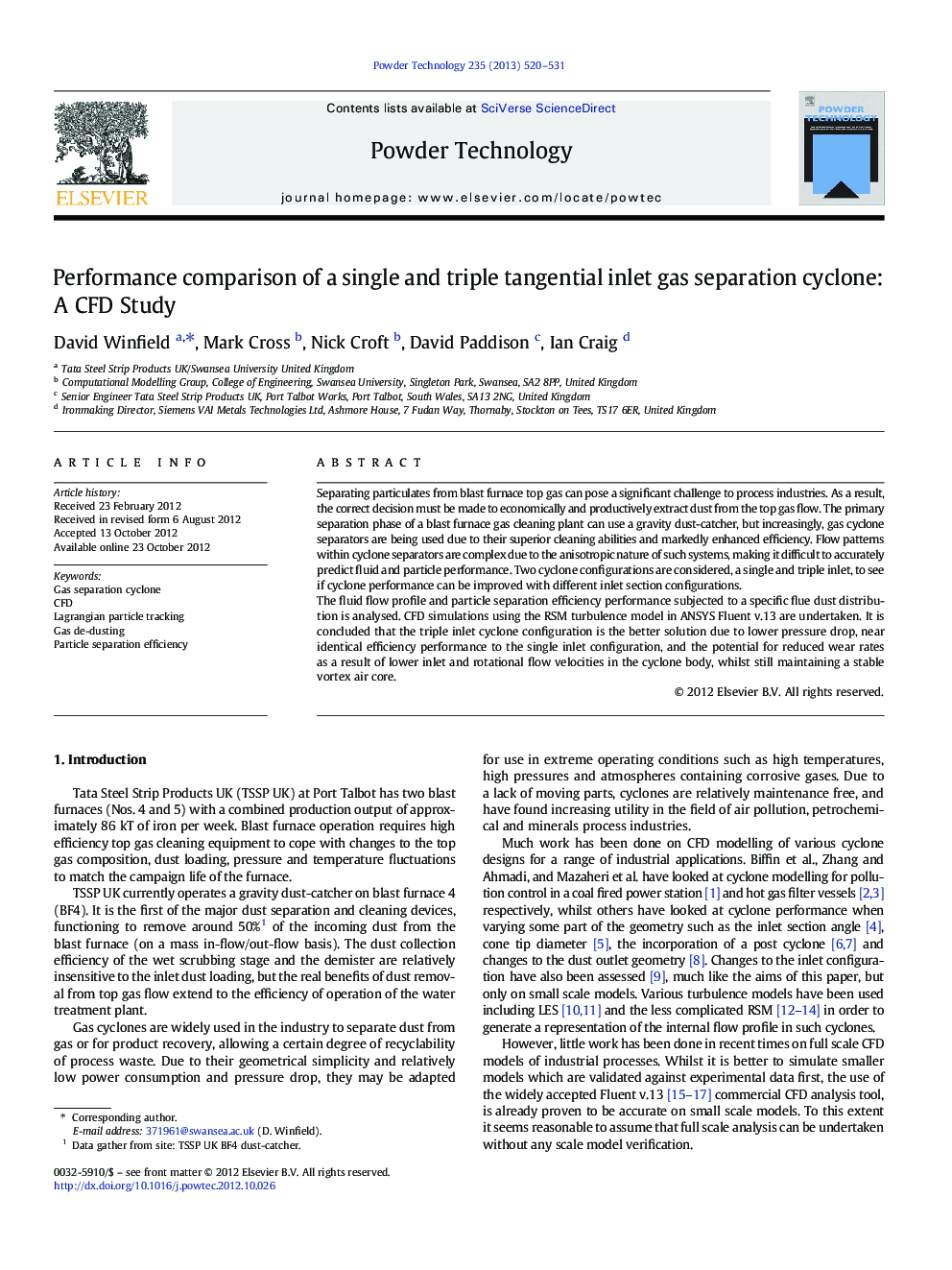
Separating particulates from blast furnace top gas can pose a significant challenge to process industries. As a result, the correct decision must be made to economically and productively extract dust from the top gas flow. The primary separation phase of a blast furnace gas cleaning plant can use a gravity dust-catcher, but increasingly, gas cyclone separators are being used due to their superior cleaning abilities and markedly enhanced efficiency. Flow patterns within cyclone separators are complex due to the anisotropic nature of such systems, making it difficult to accurately predict fluid and particle performance. Two cyclone configurations are considered, a single and triple inlet, to see if cyclone performance can be improved with different inlet section configurations.The fluid flow profile and particle separation efficiency performance subjected to a specific flue dust distribution is analysed. CFD simulations using the RSM turbulence model in ANSYS Fluent v.13 are undertaken. It is concluded that the triple inlet cyclone configuration is the better solution due to lower pressure drop, near identical efficiency performance to the single inlet configuration, and the potential for reduced wear rates as a result of lower inlet and rotational flow velocities in the cyclone body, whilst still maintaining a stable vortex air core.
CFD analysis cross section of the velocity flow field of the single inlet and triple inlet gas cyclone showing the differences in the stability and oscillation of the low pressure air core found within the internal flow structures that aid with particle separation and cyclone efficiency predictions.Figure optionsDownload as PowerPoint slideHighlights
► Accurately analyse the two cyclone designs with the help of Siemens VAI.
► A firm conclusion that the triple inlet cyclone is the better choice.
► Triple inlet cyclone performs well at lower pressure drops.
Journal: Powder Technology - Volume 235, February 2013, Pages 520–531