کد مقاله | کد نشریه | سال انتشار | مقاله انگلیسی | نسخه تمام متن |
---|---|---|---|---|
236900 | 465687 | 2013 | 6 صفحه PDF | دانلود رایگان |
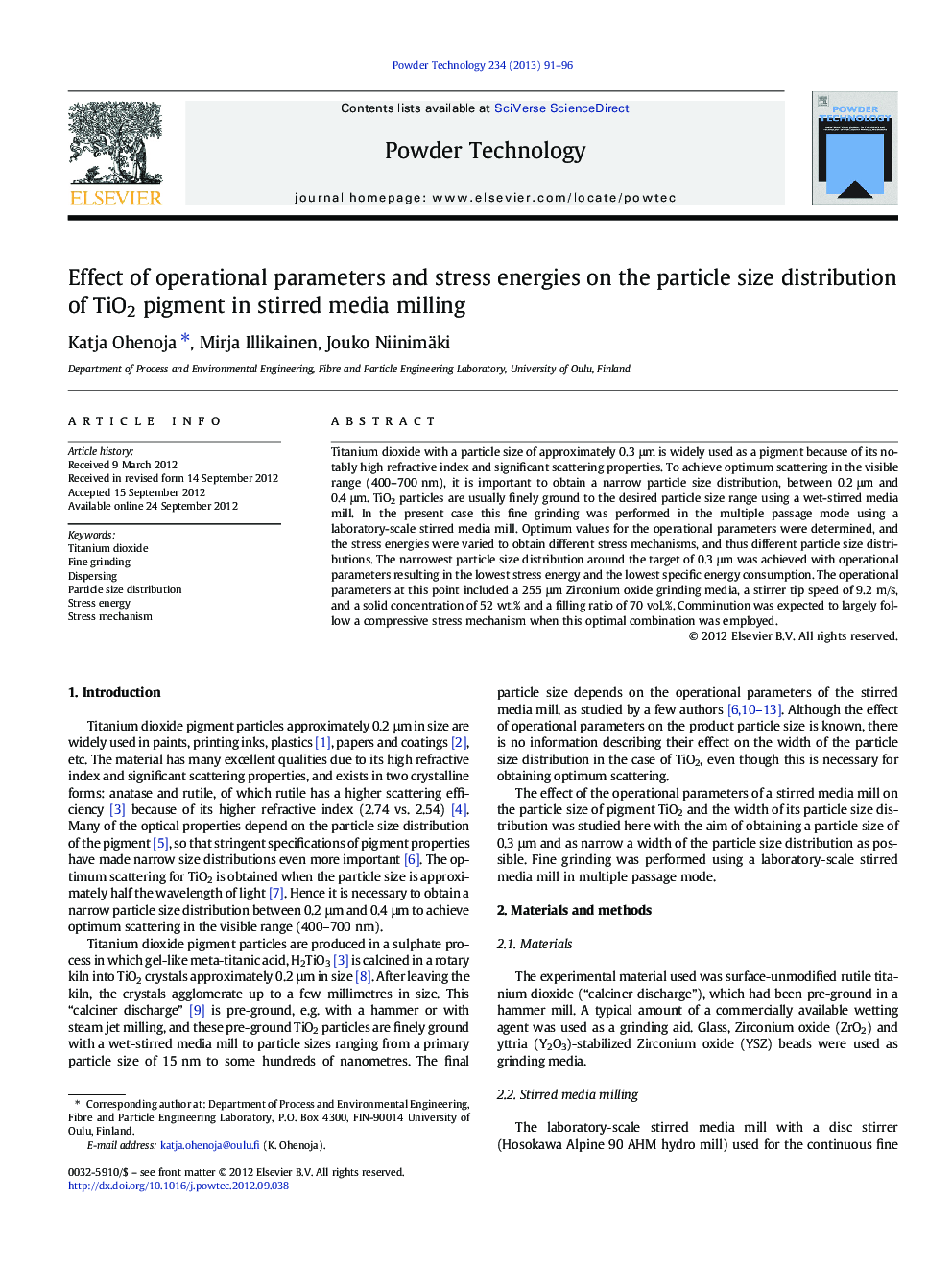
Titanium dioxide with a particle size of approximately 0.3 μm is widely used as a pigment because of its notably high refractive index and significant scattering properties. To achieve optimum scattering in the visible range (400–700 nm), it is important to obtain a narrow particle size distribution, between 0.2 μm and 0.4 μm. TiO2 particles are usually finely ground to the desired particle size range using a wet-stirred media mill. In the present case this fine grinding was performed in the multiple passage mode using a laboratory-scale stirred media mill. Optimum values for the operational parameters were determined, and the stress energies were varied to obtain different stress mechanisms, and thus different particle size distributions. The narrowest particle size distribution around the target of 0.3 μm was achieved with operational parameters resulting in the lowest stress energy and the lowest specific energy consumption. The operational parameters at this point included a 255 μm Zirconium oxide grinding media, a stirrer tip speed of 9.2 m/s, and a solid concentration of 52 wt.% and a filling ratio of 70 vol.%. Comminution was expected to largely follow a compressive stress mechanism when this optimal combination was employed.
Stirred media milling of TiO2 particles were performed. The stress energies were varied to obtain different stress mechanisms, and thus, different particle size distributions. The target particle size with the narrowest particle size distribution was obtained most energy efficiently by using low stress energy, likely due to the compressive stress mechanism.Figure optionsDownload as PowerPoint slideHighlights
► Stirred media milling of TiO2 particles
► The stress energy of grinding media is varied by operational parameters.
► Different stress energies caused different stress mechanisms.
► Optimal particle size distribution with compressive stress mechanism.
► Target particle size with the narrowest particle size distribution
Journal: Powder Technology - Volume 234, January 2013, Pages 91–96