کد مقاله | کد نشریه | سال انتشار | مقاله انگلیسی | نسخه تمام متن |
---|---|---|---|---|
237922 | 465732 | 2011 | 11 صفحه PDF | دانلود رایگان |
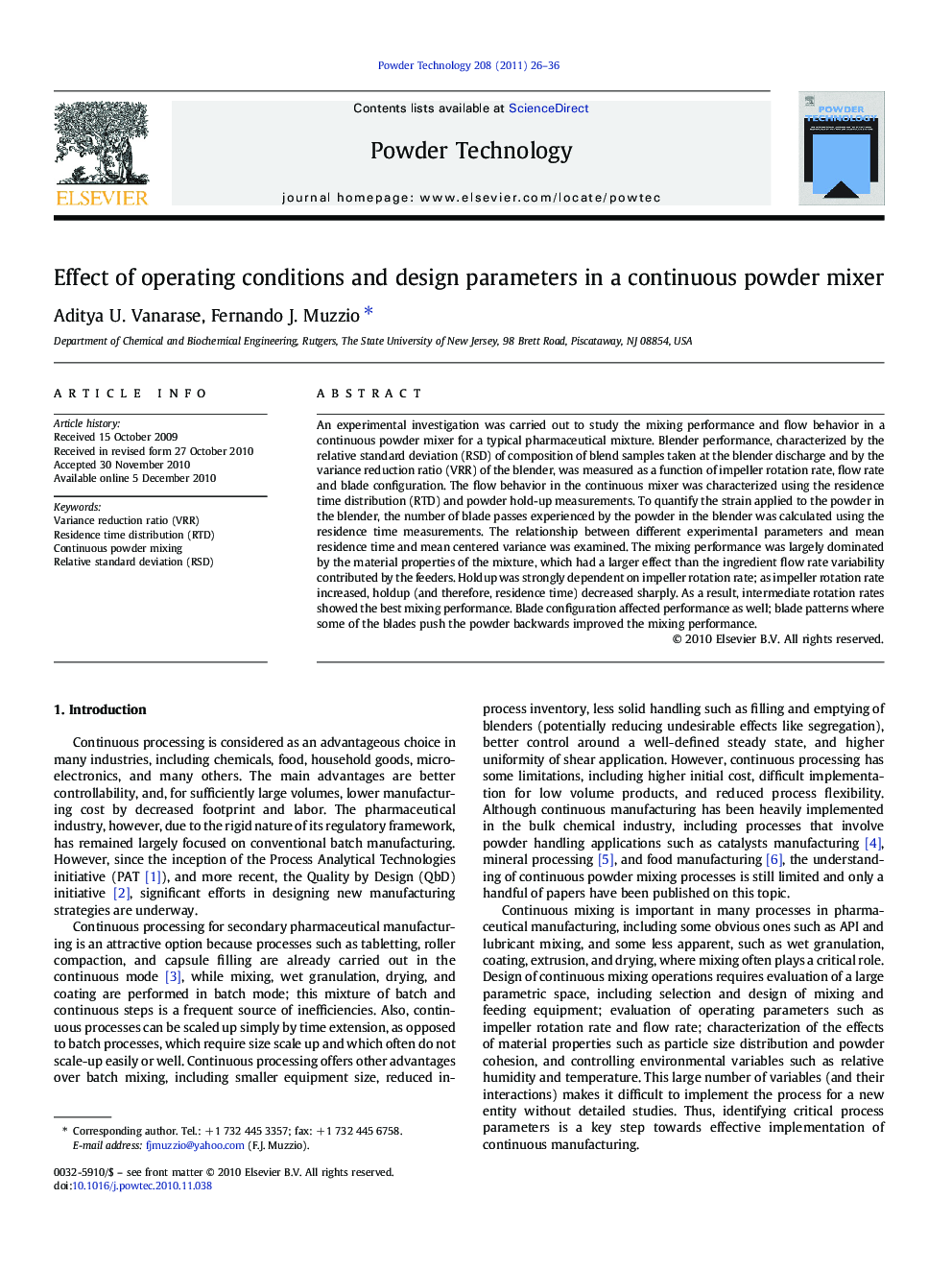
An experimental investigation was carried out to study the mixing performance and flow behavior in a continuous powder mixer for a typical pharmaceutical mixture. Blender performance, characterized by the relative standard deviation (RSD) of composition of blend samples taken at the blender discharge and by the variance reduction ratio (VRR) of the blender, was measured as a function of impeller rotation rate, flow rate and blade configuration. The flow behavior in the continuous mixer was characterized using the residence time distribution (RTD) and powder hold-up measurements. To quantify the strain applied to the powder in the blender, the number of blade passes experienced by the powder in the blender was calculated using the residence time measurements. The relationship between different experimental parameters and mean residence time and mean centered variance was examined. The mixing performance was largely dominated by the material properties of the mixture, which had a larger effect than the ingredient flow rate variability contributed by the feeders. Holdup was strongly dependent on impeller rotation rate; as impeller rotation rate increased, holdup (and therefore, residence time) decreased sharply. As a result, intermediate rotation rates showed the best mixing performance. Blade configuration affected performance as well; blade patterns where some of the blades push the powder backwards improved the mixing performance.
Graphical AbstractIn this paper, a commercial continuous mixer, Gericke GCM-250, was integrated with loss-in-weight feeders. The flow behavior and mixing performance of the continuous mixer was characterized for a model pharmaceutical mixture. Based on the experimental investigation, recommendations were made for process parameters and design aspects of the blender.Figure optionsDownload as PowerPoint slideResearch Highlights
► Mixing performance dominated by powder material properties than flowrate variability.
► As impeller speed increased, holdup (and therefore residence time) decreased sharply.
► Intermediate rotation rates showed the best mixing performance.
► Alternate blade configuration showed better mixing performance.
Journal: Powder Technology - Volume 208, Issue 1, 10 March 2011, Pages 26–36