کد مقاله | کد نشریه | سال انتشار | مقاله انگلیسی | نسخه تمام متن |
---|---|---|---|---|
413795 | 680677 | 2012 | 10 صفحه PDF | دانلود رایگان |
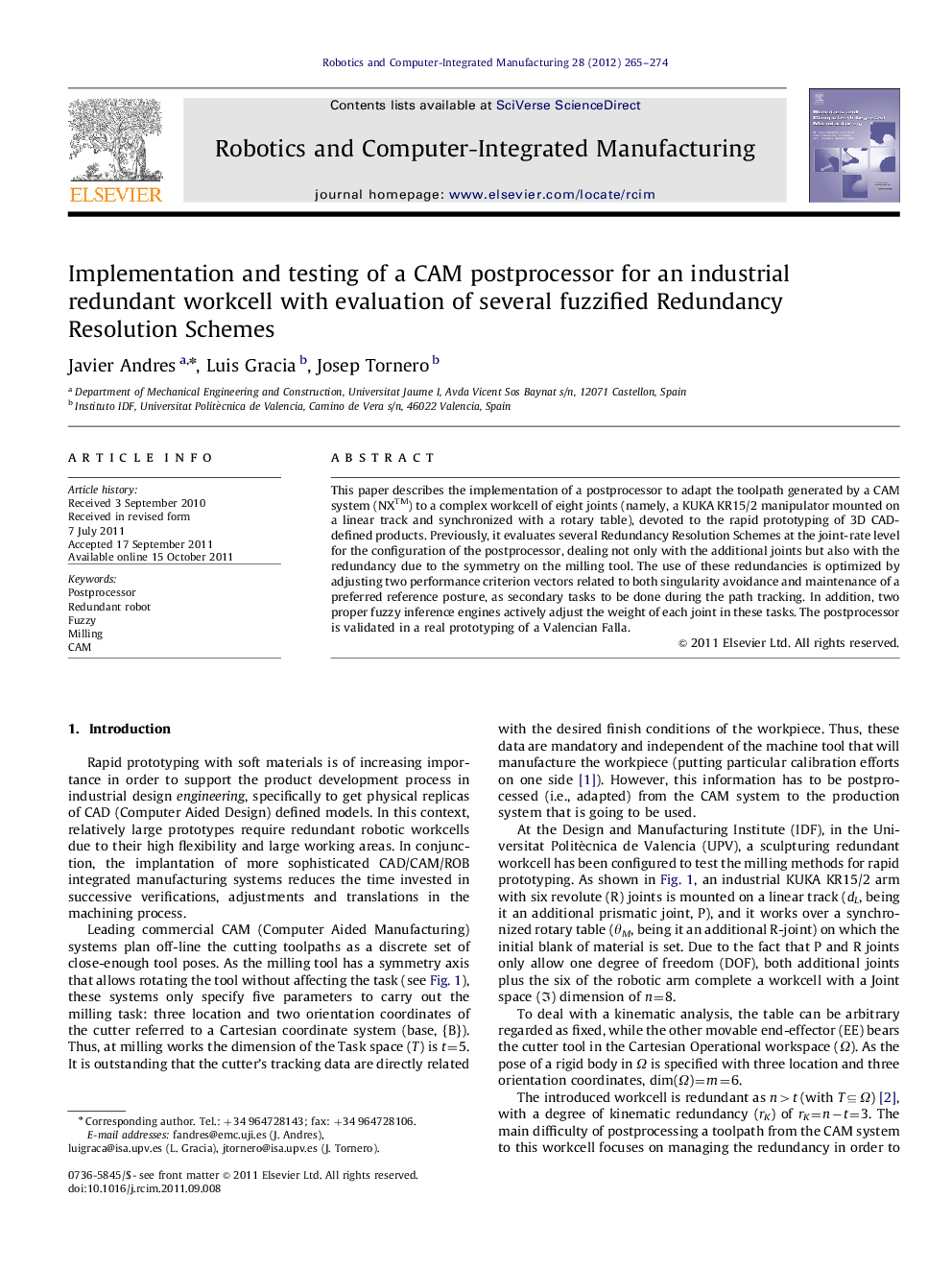
This paper describes the implementation of a postprocessor to adapt the toolpath generated by a CAM system (NXTM) to a complex workcell of eight joints (namely, a KUKA KR15/2 manipulator mounted on a linear track and synchronized with a rotary table), devoted to the rapid prototyping of 3D CAD-defined products. Previously, it evaluates several Redundancy Resolution Schemes at the joint-rate level for the configuration of the postprocessor, dealing not only with the additional joints but also with the redundancy due to the symmetry on the milling tool. The use of these redundancies is optimized by adjusting two performance criterion vectors related to both singularity avoidance and maintenance of a preferred reference posture, as secondary tasks to be done during the path tracking. In addition, two proper fuzzy inference engines actively adjust the weight of each joint in these tasks. The postprocessor is validated in a real prototyping of a Valencian Falla.
► We develop a postprocessor to adapt the toolpath generated by a CAM system.
► We consider an industrial redundant workcell of eight joints.
► Redundancy is used to avoid singularity and to maintain a preferred reference posture.
► We use fuzzy logic to adjust the weight of each joint in the secondary tasks.
► The approach is validated in a real prototyping of a Valencian Falla.
Journal: Robotics and Computer-Integrated Manufacturing - Volume 28, Issue 2, April 2012, Pages 265–274