کد مقاله | کد نشریه | سال انتشار | مقاله انگلیسی | نسخه تمام متن |
---|---|---|---|---|
496565 | 862864 | 2012 | 12 صفحه PDF | دانلود رایگان |
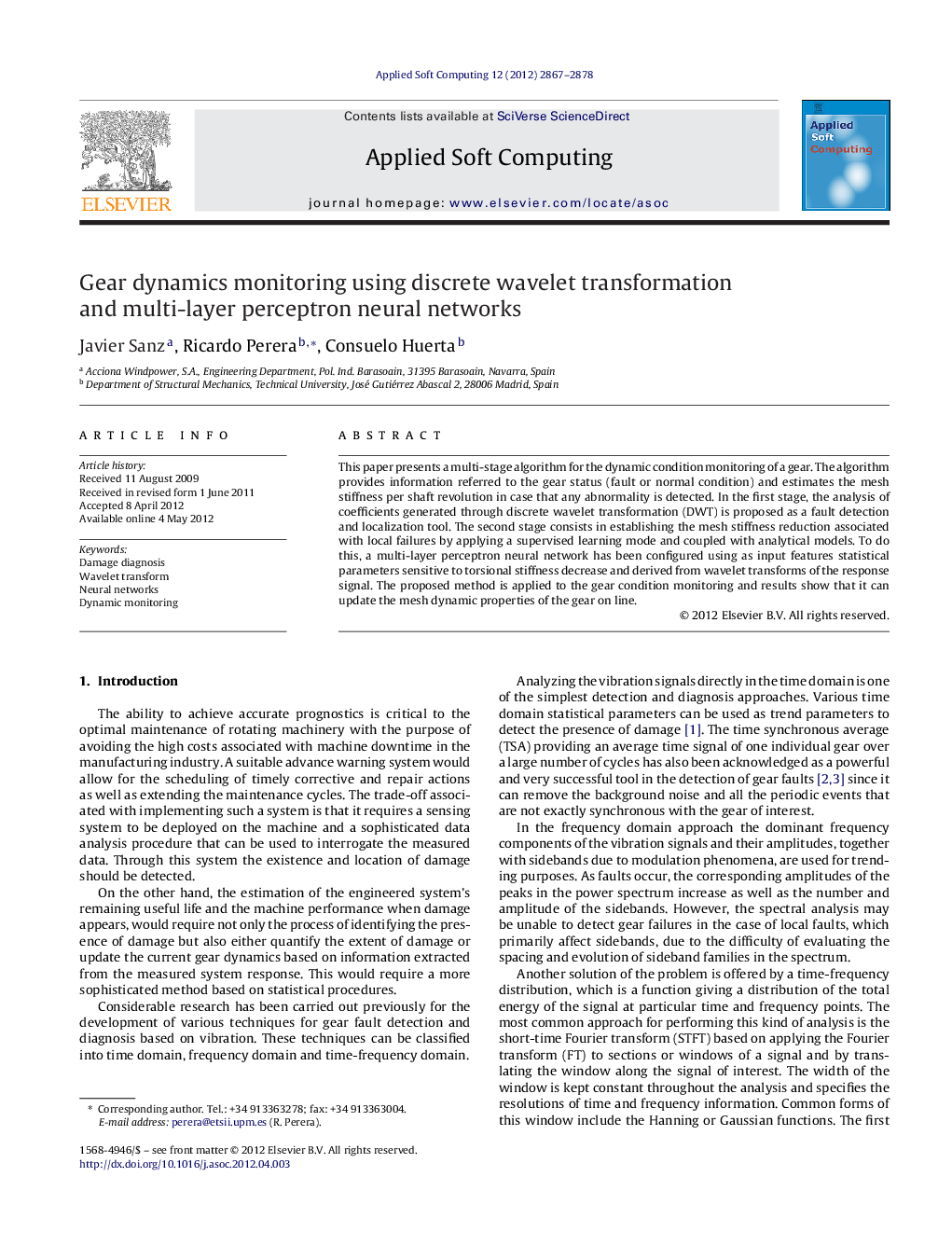
This paper presents a multi-stage algorithm for the dynamic condition monitoring of a gear. The algorithm provides information referred to the gear status (fault or normal condition) and estimates the mesh stiffness per shaft revolution in case that any abnormality is detected. In the first stage, the analysis of coefficients generated through discrete wavelet transformation (DWT) is proposed as a fault detection and localization tool. The second stage consists in establishing the mesh stiffness reduction associated with local failures by applying a supervised learning mode and coupled with analytical models. To do this, a multi-layer perceptron neural network has been configured using as input features statistical parameters sensitive to torsional stiffness decrease and derived from wavelet transforms of the response signal. The proposed method is applied to the gear condition monitoring and results show that it can update the mesh dynamic properties of the gear on line.
Figure optionsDownload as PowerPoint slideHighlights
► A method for the dynamic monitoring in rotating machinery has been proposed.
► Wavelet transforms and neural networks allow detection and location of defects.
► Statistical parameters extracted from wavelet coefficients are used for defect quantification.
► Statistical parameters feed a neural network to automate the damage quantification procedure.
Journal: Applied Soft Computing - Volume 12, Issue 9, September 2012, Pages 2867–2878