کد مقاله | کد نشریه | سال انتشار | مقاله انگلیسی | نسخه تمام متن |
---|---|---|---|---|
514521 | 866753 | 2013 | 18 صفحه PDF | دانلود رایگان |
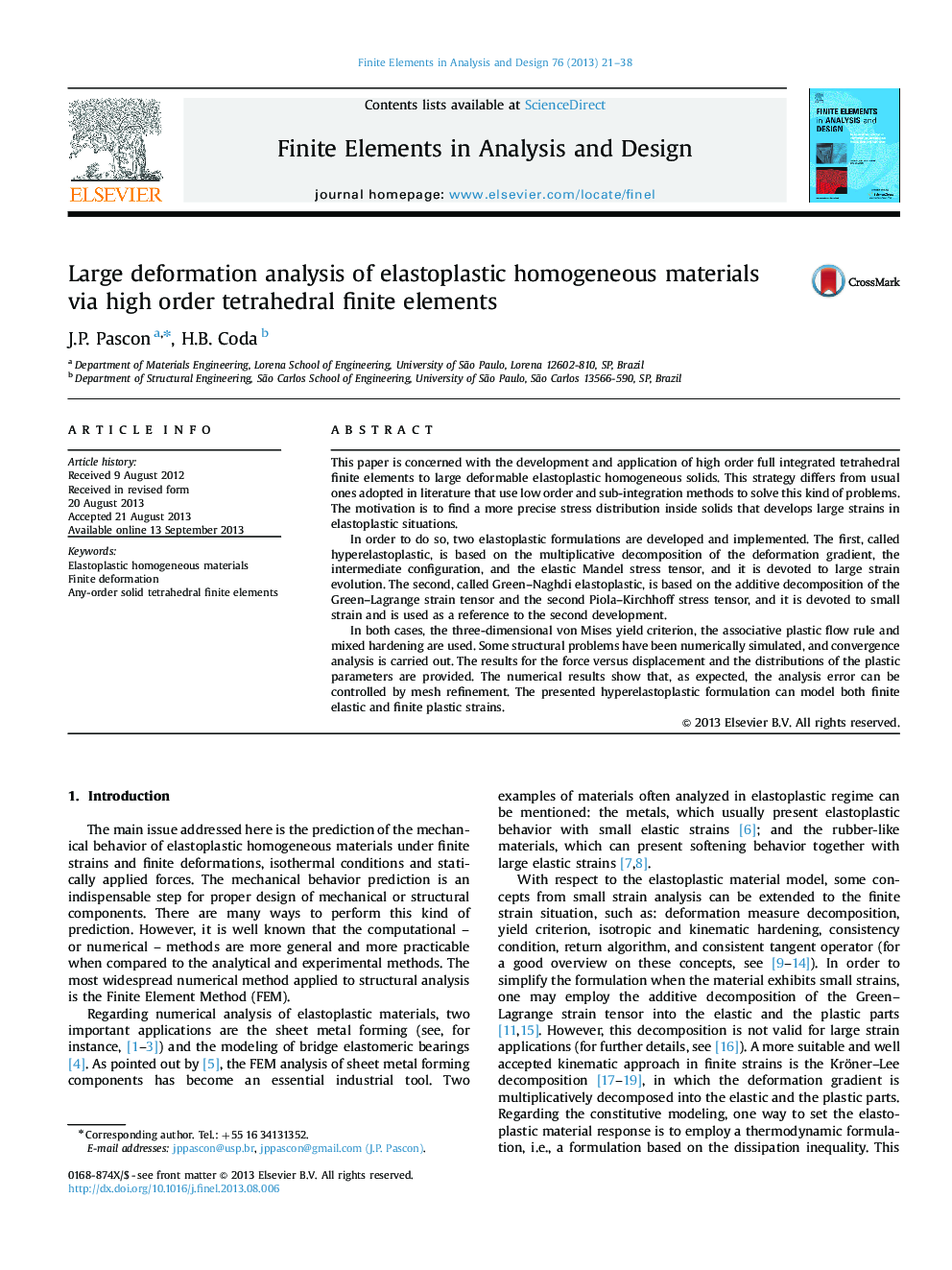
• Analysis of homogeneous elastoplastic materials under static, isothermal and large deformation conditions.
• Parallel processing enables the use of high order, fully integrated solid tetrahedral finite elements.
• These elements present locking-free behavior and reliable stress fields for mechanical problems.
This paper is concerned with the development and application of high order full integrated tetrahedral finite elements to large deformable elastoplastic homogeneous solids. This strategy differs from usual ones adopted in literature that use low order and sub-integration methods to solve this kind of problems. The motivation is to find a more precise stress distribution inside solids that develops large strains in elastoplastic situations.In order to do so, two elastoplastic formulations are developed and implemented. The first, called hyperelastoplastic, is based on the multiplicative decomposition of the deformation gradient, the intermediate configuration, and the elastic Mandel stress tensor, and it is devoted to large strain evolution. The second, called Green–Naghdi elastoplastic, is based on the additive decomposition of the Green–Lagrange strain tensor and the second Piola–Kirchhoff stress tensor, and it is devoted to small strain and is used as a reference to the second development.In both cases, the three-dimensional von Mises yield criterion, the associative plastic flow rule and mixed hardening are used. Some structural problems have been numerically simulated, and convergence analysis is carried out. The results for the force versus displacement and the distributions of the plastic parameters are provided. The numerical results show that, as expected, the analysis error can be controlled by mesh refinement. The presented hyperelastoplastic formulation can model both finite elastic and finite plastic strains.
Journal: Finite Elements in Analysis and Design - Volume 76, 15 November 2013, Pages 21–38