کد مقاله | کد نشریه | سال انتشار | مقاله انگلیسی | نسخه تمام متن |
---|---|---|---|---|
5469238 | 1519226 | 2017 | 13 صفحه PDF | دانلود رایگان |
عنوان انگلیسی مقاله ISI
Optical polishing process: Analysis and optimization using response surface methodology (RSM) for large diameter fused silica flat substrates
دانلود مقاله + سفارش ترجمه
دانلود مقاله ISI انگلیسی
رایگان برای ایرانیان
کلمات کلیدی
موضوعات مرتبط
مهندسی و علوم پایه
سایر رشته های مهندسی
مهندسی صنعتی و تولید
پیش نمایش صفحه اول مقاله
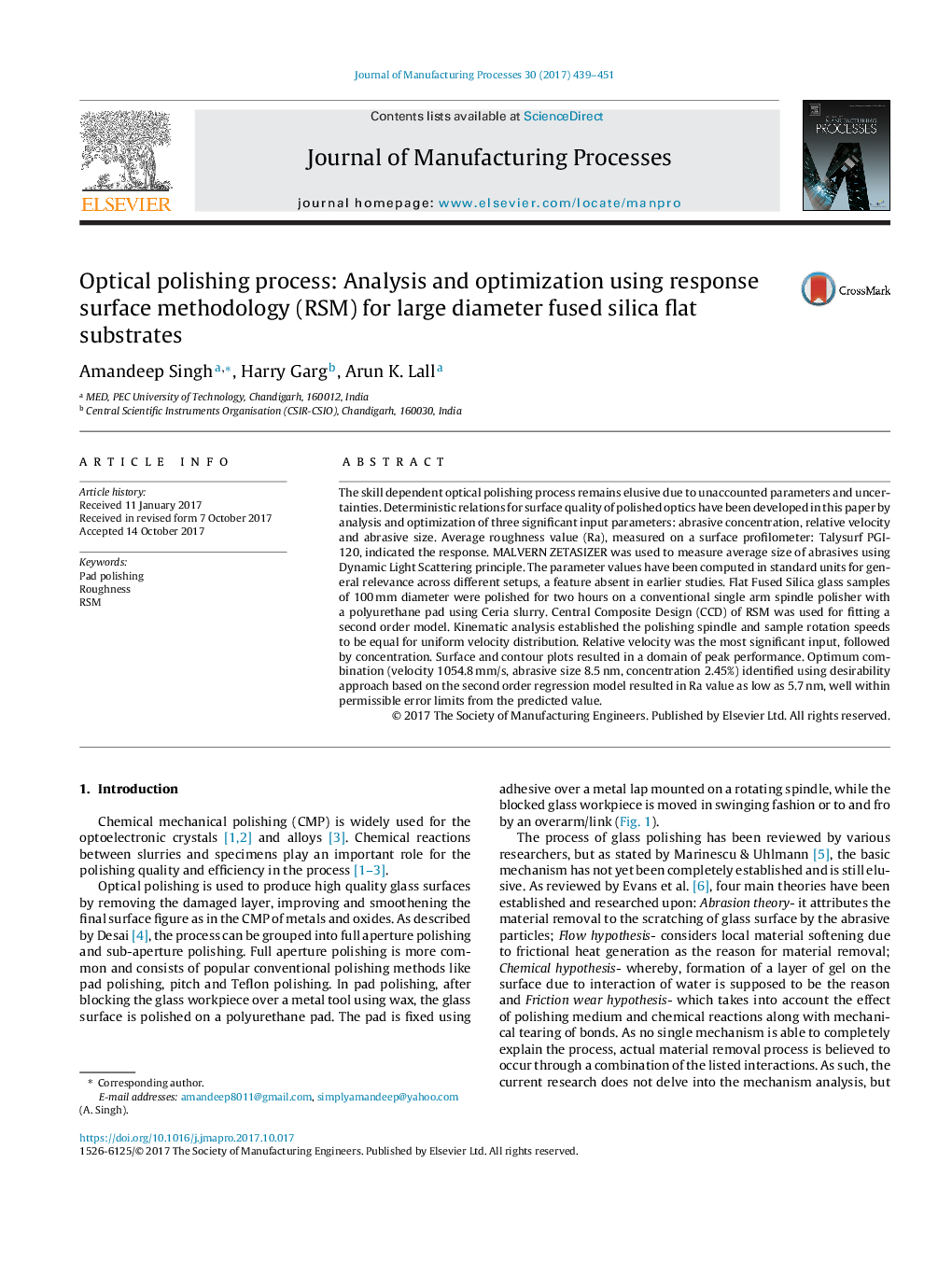
چکیده انگلیسی
The skill dependent optical polishing process remains elusive due to unaccounted parameters and uncertainties. Deterministic relations for surface quality of polished optics have been developed in this paper by analysis and optimization of three significant input parameters: abrasive concentration, relative velocity and abrasive size. Average roughness value (Ra), measured on a surface profilometer: Talysurf PGI-120, indicated the response. MALVERN ZETASIZER was used to measure average size of abrasives using Dynamic Light Scattering principle. The parameter values have been computed in standard units for general relevance across different setups, a feature absent in earlier studies. Flat Fused Silica glass samples of 100Â mm diameter were polished for two hours on a conventional single arm spindle polisher with a polyurethane pad using Ceria slurry. Central Composite Design (CCD) of RSM was used for fitting a second order model. Kinematic analysis established the polishing spindle and sample rotation speeds to be equal for uniform velocity distribution. Relative velocity was the most significant input, followed by concentration. Surface and contour plots resulted in a domain of peak performance. Optimum combination (velocity 1054.8Â mm/s, abrasive size 8.5Â nm, concentration 2.45%) identified using desirability approach based on the second order regression model resulted in Ra value as low as 5.7Â nm, well within permissible error limits from the predicted value.
ناشر
Database: Elsevier - ScienceDirect (ساینس دایرکت)
Journal: Journal of Manufacturing Processes - Volume 30, December 2017, Pages 439-451
Journal: Journal of Manufacturing Processes - Volume 30, December 2017, Pages 439-451
نویسندگان
Amandeep Singh, Harry Garg, Arun K. Lall,