کد مقاله | کد نشریه | سال انتشار | مقاله انگلیسی | نسخه تمام متن |
---|---|---|---|---|
5470296 | 1519294 | 2017 | 6 صفحه PDF | دانلود رایگان |
عنوان انگلیسی مقاله ISI
Component Mode Synthesis Approach for Micro End Mill Dynamics Considering Machine Tool Compliance
دانلود مقاله + سفارش ترجمه
دانلود مقاله ISI انگلیسی
رایگان برای ایرانیان
کلمات کلیدی
موضوعات مرتبط
مهندسی و علوم پایه
سایر رشته های مهندسی
مهندسی صنعتی و تولید
پیش نمایش صفحه اول مقاله
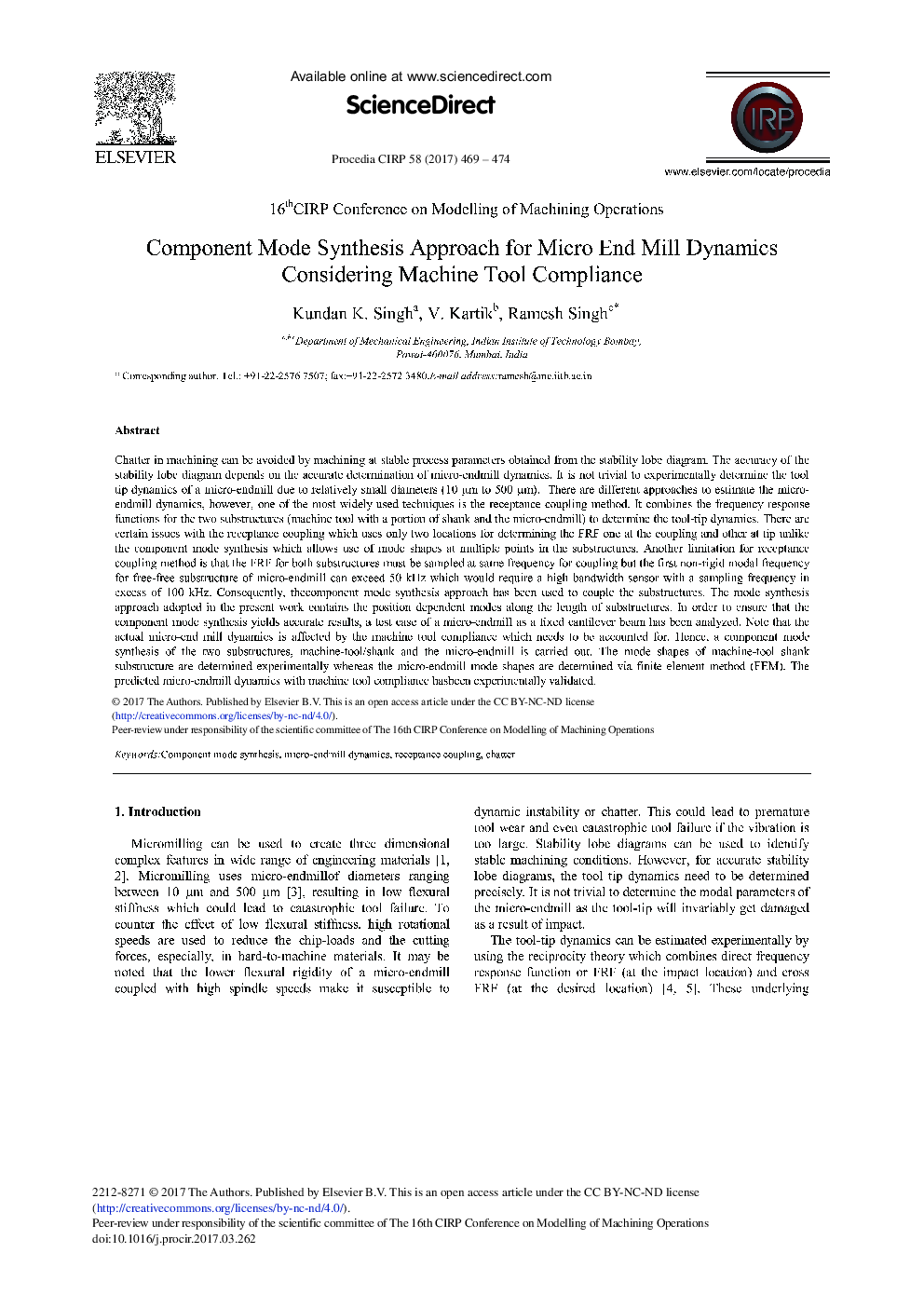
چکیده انگلیسی
Chatter in machining can be avoided by machining at stable process parameters obtained from the stability lobe diagram. The accuracy of the stability lobe diagram depends on the accurate determination of micro-endmill dynamics. It is not trivial to experimentally determine the tool tip dynamics of a micro-endmill due to relatively small diameters (10 μm to 500 μm). There are different approaches to estimate the micro-endmill dynamics, however, one of the most widely used techniques is the receptance coupling method. It combines the frequency response functions for the two substructures (machine tool with a portion of shank and the micro-endmill) to determine the tool-tip dynamics. There are certain issues with the receptance coupling which uses only two locations for determining the FRF one at the coupling and other at tip unlike the component mode synthesis which allows use of mode shapes at multiple points in the substructures. Another limitation for receptance coupling method is that the FRF for both substructures must be sampled at same frequency for coupling but the first non-rigid modal frequency for free-free substructure of micro-endmill can exceed 50 kHz which would require a high bandwidth sensor with a sampling frequency in excess of 100 kHz. Consequently, the component mode synthesis approach has been used to couple the substructures. The mode synthesis approach adopted in the present work contains the position dependent modes along the length of substructures. In order to ensure that the component mode synthesis yields accurate results, a test case of a micro-endmill as a fixed cantilever beam has been analyzed. Note that the actual micro-end mill dynamics is affected by the machine tool compliance which needs to be accounted for. Hence, a component mode synthesis of the two substructures, machine-tool/shank and the micro-endmill is carried out. The mode shapes of machine-tool shank substructure are determined experimentally whereas the micro-endmill mode shapes are determined via finite element method (FEM). The predicted micro-endmill dynamics with machine tool compliance has been experimentally validated.
ناشر
Database: Elsevier - ScienceDirect (ساینس دایرکت)
Journal: Procedia CIRP - Volume 58, 2017, Pages 469-474
Journal: Procedia CIRP - Volume 58, 2017, Pages 469-474
نویسندگان
Kundan K. Singh, V. Kartik, Ramesh Singh,