کد مقاله | کد نشریه | سال انتشار | مقاله انگلیسی | نسخه تمام متن |
---|---|---|---|---|
610709 | 880656 | 2009 | 6 صفحه PDF | دانلود رایگان |
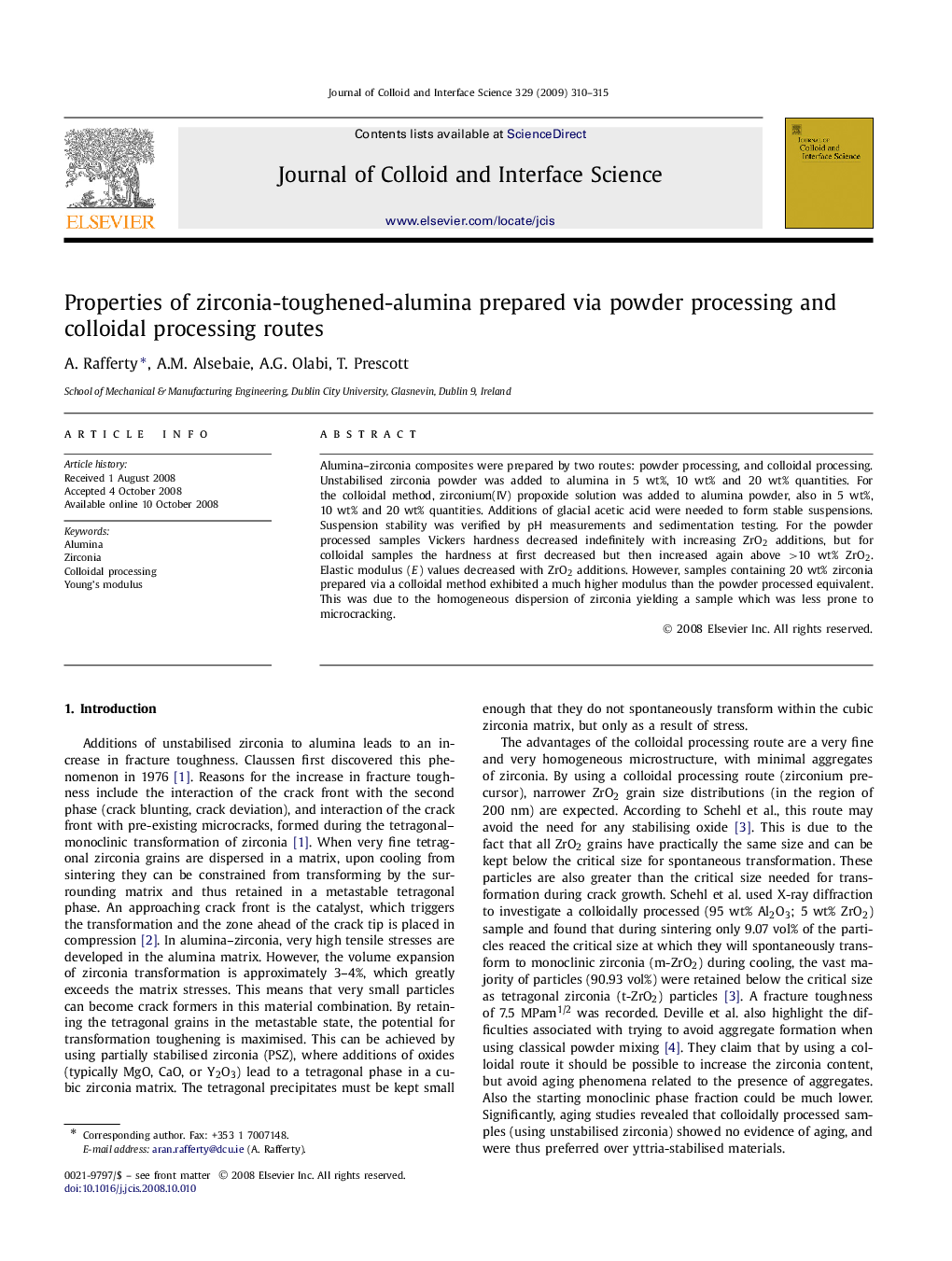
Alumina–zirconia composites were prepared by two routes: powder processing, and colloidal processing. Unstabilised zirconia powder was added to alumina in 5 wt%, 10 wt% and 20 wt% quantities. For the colloidal method, zirconium(IV) propoxide solution was added to alumina powder, also in 5 wt%, 10 wt% and 20 wt% quantities. Additions of glacial acetic acid were needed to form stable suspensions. Suspension stability was verified by pH measurements and sedimentation testing. For the powder processed samples Vickers hardness decreased indefinitely with increasing ZrO2 additions, but for colloidal samples the hardness at first decreased but then increased again above >10 wt% ZrO2. Elastic modulus (E) values decreased with ZrO2 additions. However, samples containing 20 wt% zirconia prepared via a colloidal method exhibited a much higher modulus than the powder processed equivalent. This was due to the homogeneous dispersion of zirconia yielding a sample which was less prone to microcracking.
The modulus of the 20 wt% ZrO2 powder processed sample is very low as compared to the value obtained for the colloidally processed sample. This is believed due to the presence of uncontained, catastrophic microcracking in the powder processed sample.Figure optionsDownload as PowerPoint slide
Journal: Journal of Colloid and Interface Science - Volume 329, Issue 2, 15 January 2009, Pages 310–315