کد مقاله | کد نشریه | سال انتشار | مقاله انگلیسی | نسخه تمام متن |
---|---|---|---|---|
618476 | 1455028 | 2011 | 8 صفحه PDF | دانلود رایگان |
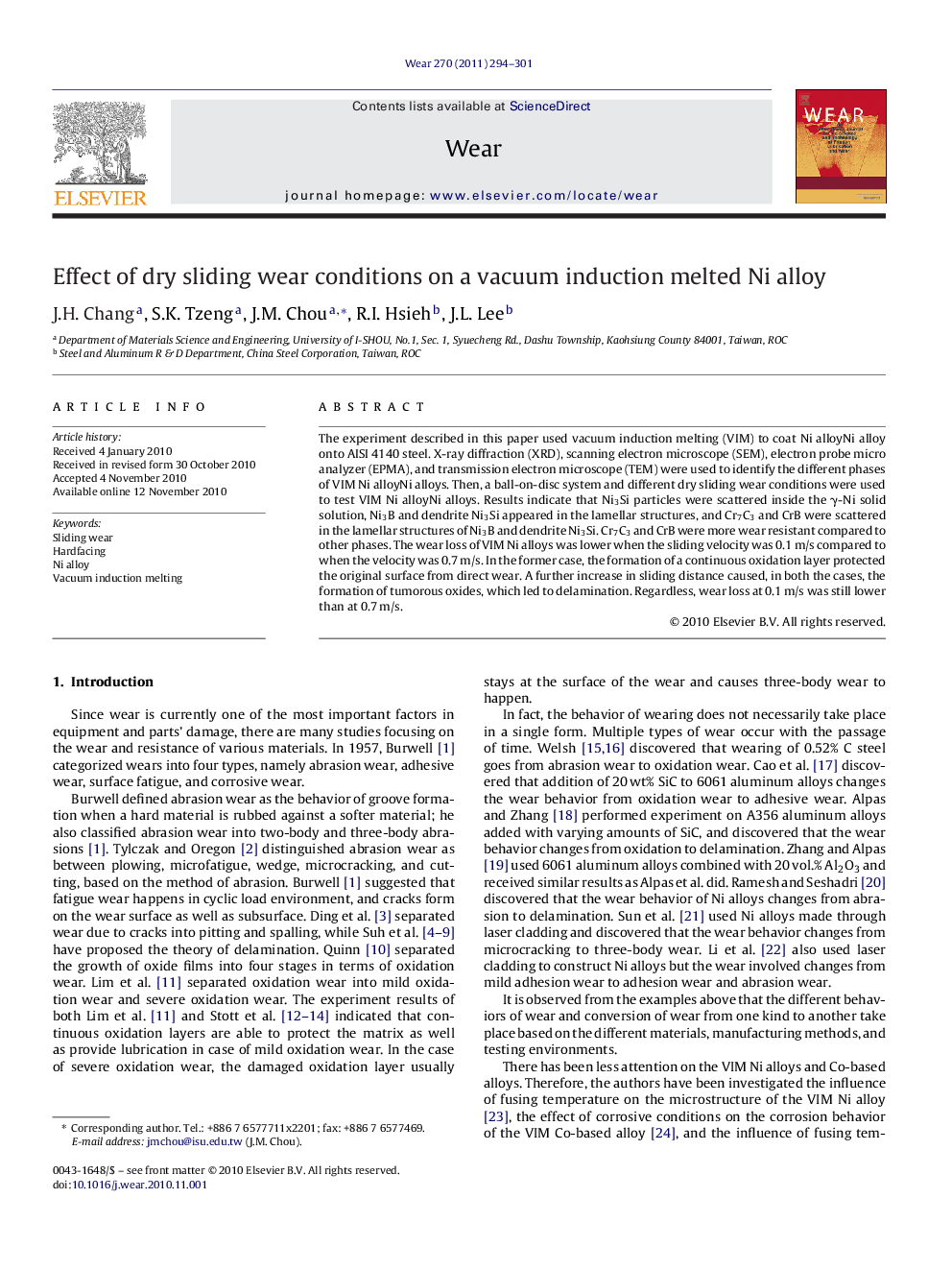
The experiment described in this paper used vacuum induction melting (VIM) to coat Ni alloyNi alloy onto AISI 4140 steel. X-ray diffraction (XRD), scanning electron microscope (SEM), electron probe micro analyzer (EPMA), and transmission electron microscope (TEM) were used to identify the different phases of VIM Ni alloyNi alloys. Then, a ball-on-disc system and different dry sliding wear conditions were used to test VIM Ni alloyNi alloys. Results indicate that Ni3Si particles were scattered inside the γ-Ni solid solution, Ni3B and dendrite Ni3Si appeared in the lamellar structures, and Cr7C3 and CrB were scattered in the lamellar structures of Ni3B and dendrite Ni3Si. Cr7C3 and CrB were more wear resistant compared to other phases. The wear loss of VIM Ni alloys was lower when the sliding velocity was 0.1 m/s compared to when the velocity was 0.7 m/s. In the former case, the formation of a continuous oxidation layer protected the original surface from direct wear. A further increase in sliding distance caused, in both the cases, the formation of tumorous oxides, which led to delamination. Regardless, wear loss at 0.1 m/s was still lower than at 0.7 m/s.
Research highlights▶ The microstructure of VIM Ni alloys contains γ-Ni, Ni3Si, Ni3B, Cr7C3, and CrB. Also, Ni3Si particles were scattered inside the γ-Ni solid solution, Ni3B and dendrite Ni3Si appeared in the lamellar structures, and Cr7C3 and CrB were scattered in the lamellar structures of Ni3B and dendrite Ni3Si. Cr7C3 and CrB were more wear resistant compared to other phases. ▶ The wear loss of VIM Ni alloys was lower when the sliding velocity was 0.1 m/s compared to when the velocity was 0.7 m/s. This is due to the fact that the ability of wear at 0.1 m/s is already lower than that at 0.7 m/s. ▶ As the sliding distance increases, the worn surface of 0.1 m/s forms a continuous oxidation layer that protects the original surface. On the contrary, tumorous oxides that result in delamination form on the worn surface of 0.7 m/s. Although this also happens in the case of 0.1 m/s when sliding distance reaches 10,000 m, the quantity of wear loss is still smaller than that in the case of 0.7 m/s.
Journal: Wear - Volume 270, Issues 3–4, 12 January 2011, Pages 294–301