کد مقاله | کد نشریه | سال انتشار | مقاله انگلیسی | نسخه تمام متن |
---|---|---|---|---|
619211 | 881844 | 2009 | 8 صفحه PDF | دانلود رایگان |
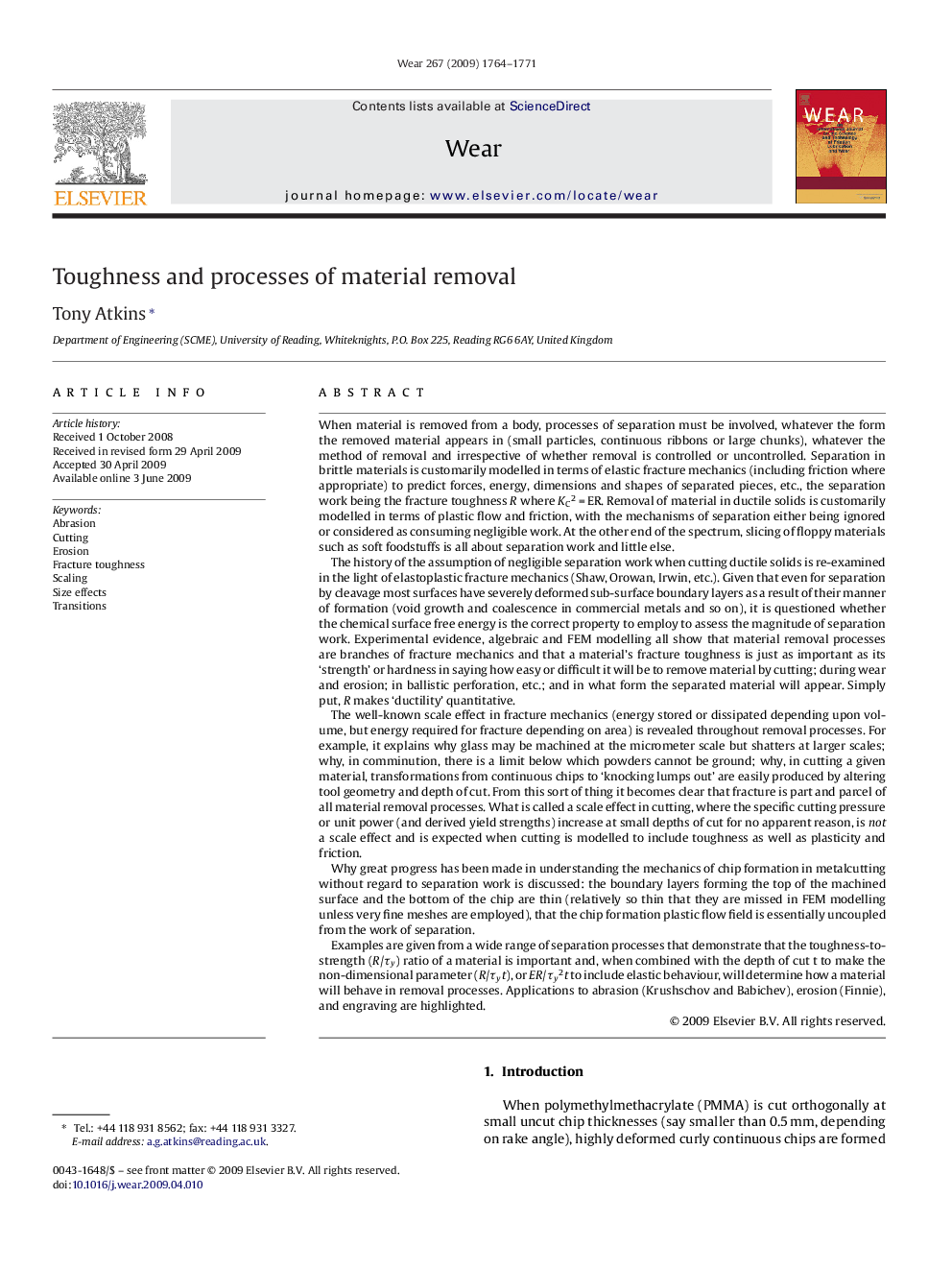
When material is removed from a body, processes of separation must be involved, whatever the form the removed material appears in (small particles, continuous ribbons or large chunks), whatever the method of removal and irrespective of whether removal is controlled or uncontrolled. Separation in brittle materials is customarily modelled in terms of elastic fracture mechanics (including friction where appropriate) to predict forces, energy, dimensions and shapes of separated pieces, etc., the separation work being the fracture toughness R where KC2 = ER. Removal of material in ductile solids is customarily modelled in terms of plastic flow and friction, with the mechanisms of separation either being ignored or considered as consuming negligible work. At the other end of the spectrum, slicing of floppy materials such as soft foodstuffs is all about separation work and little else.The history of the assumption of negligible separation work when cutting ductile solids is re-examined in the light of elastoplastic fracture mechanics (Shaw, Orowan, Irwin, etc.). Given that even for separation by cleavage most surfaces have severely deformed sub-surface boundary layers as a result of their manner of formation (void growth and coalescence in commercial metals and so on), it is questioned whether the chemical surface free energy is the correct property to employ to assess the magnitude of separation work. Experimental evidence, algebraic and FEM modelling all show that material removal processes are branches of fracture mechanics and that a material's fracture toughness is just as important as its ‘strength’ or hardness in saying how easy or difficult it will be to remove material by cutting; during wear and erosion; in ballistic perforation, etc.; and in what form the separated material will appear. Simply put, R makes ‘ductility’ quantitative.The well-known scale effect in fracture mechanics (energy stored or dissipated depending upon volume, but energy required for fracture depending on area) is revealed throughout removal processes. For example, it explains why glass may be machined at the micrometer scale but shatters at larger scales; why, in comminution, there is a limit below which powders cannot be ground; why, in cutting a given material, transformations from continuous chips to ‘knocking lumps out’ are easily produced by altering tool geometry and depth of cut. From this sort of thing it becomes clear that fracture is part and parcel of all material removal processes. What is called a scale effect in cutting, where the specific cutting pressure or unit power (and derived yield strengths) increase at small depths of cut for no apparent reason, is not a scale effect and is expected when cutting is modelled to include toughness as well as plasticity and friction.Why great progress has been made in understanding the mechanics of chip formation in metalcutting without regard to separation work is discussed: the boundary layers forming the top of the machined surface and the bottom of the chip are thin (relatively so thin that they are missed in FEM modelling unless very fine meshes are employed), that the chip formation plastic flow field is essentially uncoupled from the work of separation.Examples are given from a wide range of separation processes that demonstrate that the toughness-to-strength (R/τy) ratio of a material is important and, when combined with the depth of cut t to make the non-dimensional parameter (R/τyt), or ER/τy2t to include elastic behaviour, will determine how a material will behave in removal processes. Applications to abrasion (Krushschov and Babichev), erosion (Finnie), and engraving are highlighted.
Journal: Wear - Volume 267, Issue 11, 29 October 2009, Pages 1764–1771