کد مقاله | کد نشریه | سال انتشار | مقاله انگلیسی | نسخه تمام متن |
---|---|---|---|---|
6464800 | 438916 | 2016 | 7 صفحه PDF | دانلود رایگان |
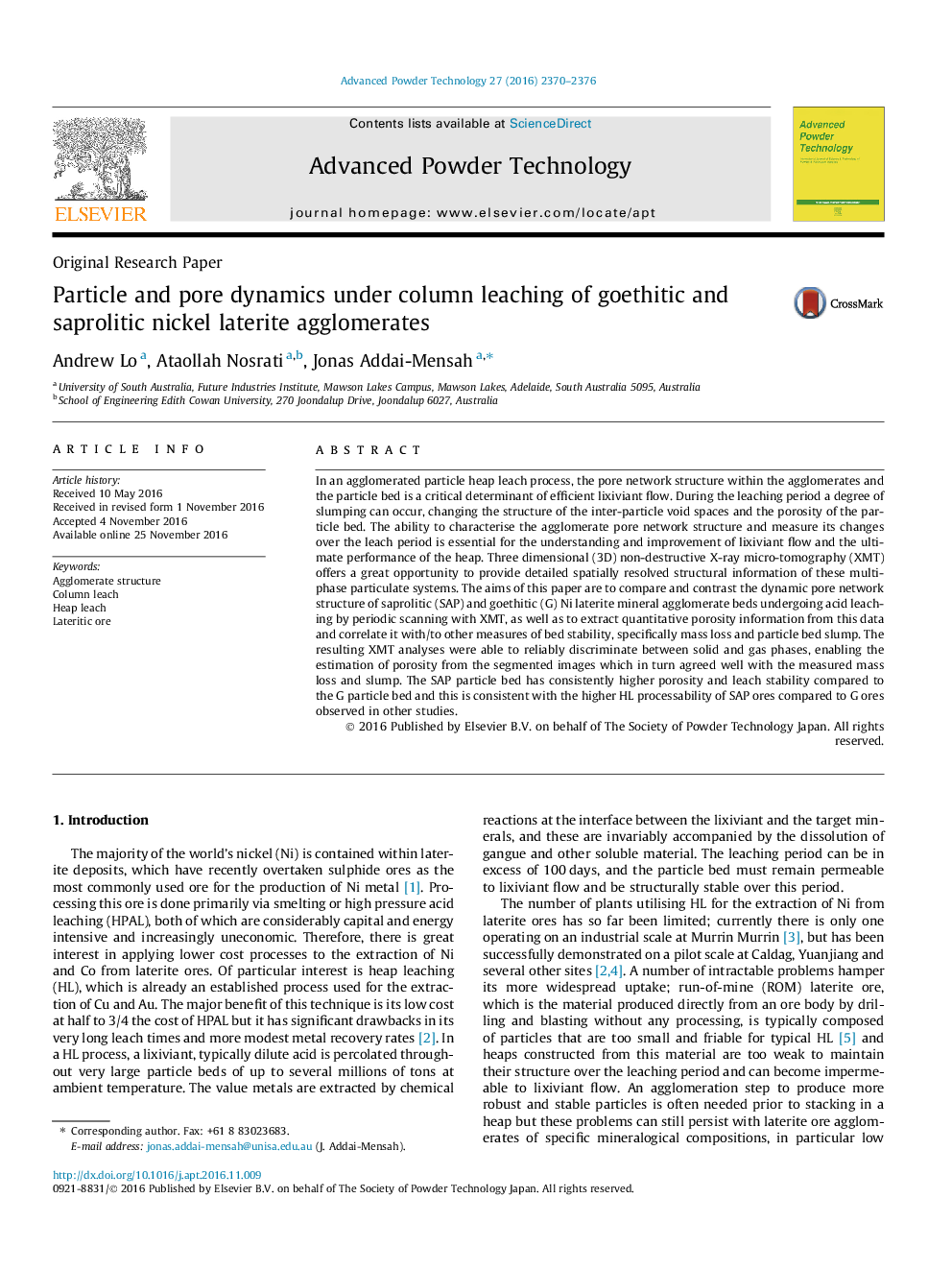
- Dynamic pore network of Ni laterite agglomerates during column leaching is studied.
- Micro tomography is used to obtain spatial images and porosity of the particle beds.
- High leaching bed porosity coincides with low slump and particle erosion.
- Leached bed porosity was higher for saprolitic than goethitic particles.
In an agglomerated particle heap leach process, the pore network structure within the agglomerates and the particle bed is a critical determinant of efficient lixiviant flow. During the leaching period a degree of slumping can occur, changing the structure of the inter-particle void spaces and the porosity of the particle bed. The ability to characterise the agglomerate pore network structure and measure its changes over the leach period is essential for the understanding and improvement of lixiviant flow and the ultimate performance of the heap. Three dimensional (3D) non-destructive X-ray micro-tomography (XMT) offers a great opportunity to provide detailed spatially resolved structural information of these multiphase particulate systems. The aims of this paper are to compare and contrast the dynamic pore network structure of saprolitic (SAP) and goethitic (G) Ni laterite mineral agglomerate beds undergoing acid leaching by periodic scanning with XMT, as well as to extract quantitative porosity information from this data and correlate it with/to other measures of bed stability, specifically mass loss and particle bed slump. The resulting XMT analyses were able to reliably discriminate between solid and gas phases, enabling the estimation of porosity from the segmented images which in turn agreed well with the measured mass loss and slump. The SAP particle bed has consistently higher porosity and leach stability compared to the G particle bed and this is consistent with the higher HL processability of SAP ores compared to G ores observed in other studies.
191
Journal: Advanced Powder Technology - Volume 27, Issue 6, November 2016, Pages 2370-2376