کد مقاله | کد نشریه | سال انتشار | مقاله انگلیسی | نسخه تمام متن |
---|---|---|---|---|
7176481 | 1466712 | 2018 | 8 صفحه PDF | دانلود رایگان |
عنوان انگلیسی مقاله ISI
Application of electrolyte injection to the electro-chemical discharge machining (ECDM) on the optical glass
دانلود مقاله + سفارش ترجمه
دانلود مقاله ISI انگلیسی
رایگان برای ایرانیان
کلمات کلیدی
موضوعات مرتبط
مهندسی و علوم پایه
سایر رشته های مهندسی
مهندسی صنعتی و تولید
پیش نمایش صفحه اول مقاله
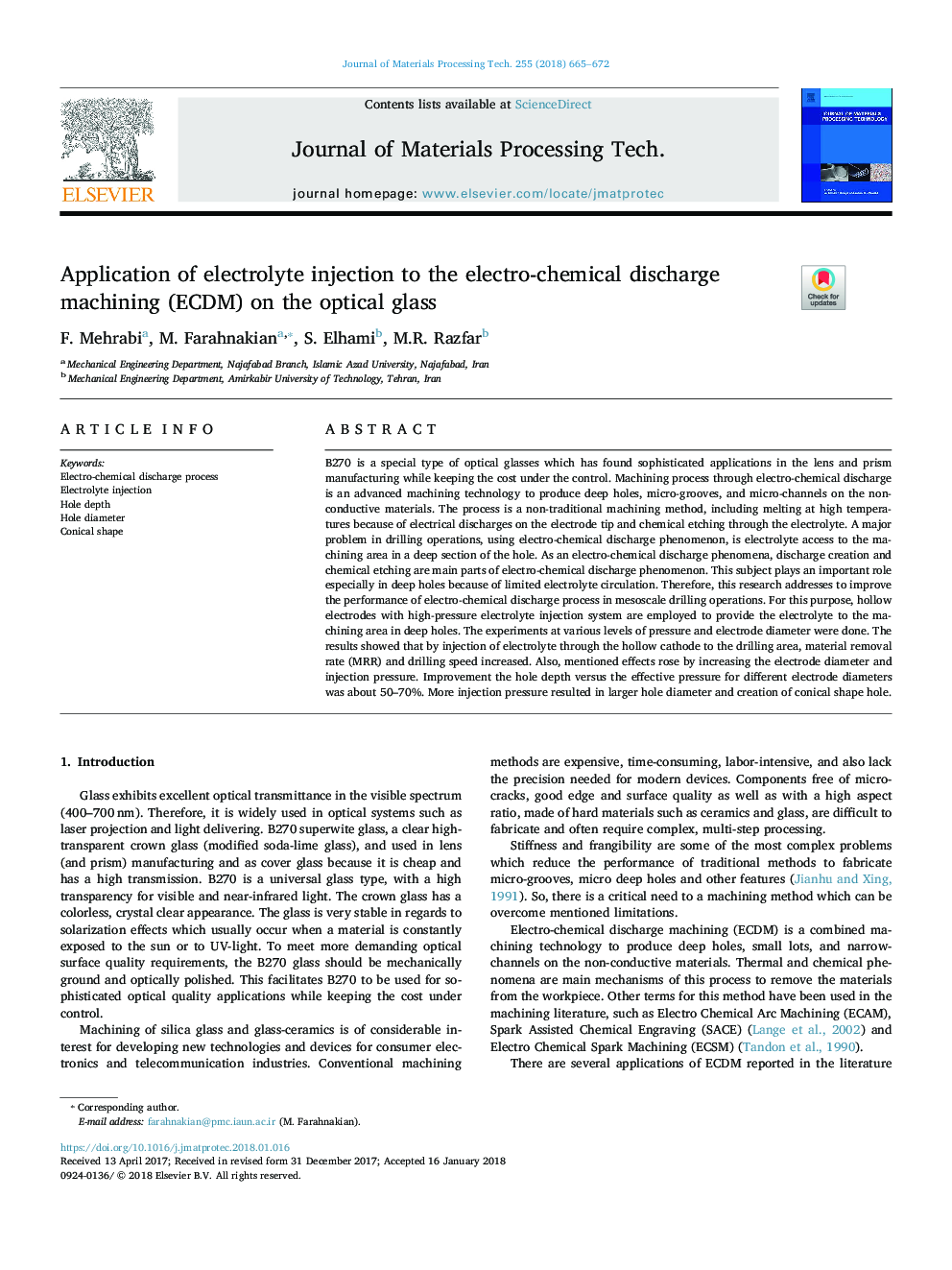
چکیده انگلیسی
B270 is a special type of optical glasses which has found sophisticated applications in the lens and prism manufacturing while keeping the cost under the control. Machining process through electro-chemical discharge is an advanced machining technology to produce deep holes, micro-grooves, and micro-channels on the non-conductive materials. The process is a non-traditional machining method, including melting at high temperatures because of electrical discharges on the electrode tip and chemical etching through the electrolyte. A major problem in drilling operations, using electro-chemical discharge phenomenon, is electrolyte access to the machining area in a deep section of the hole. As an electro-chemical discharge phenomena, discharge creation and chemical etching are main parts of electro-chemical discharge phenomenon. This subject plays an important role especially in deep holes because of limited electrolyte circulation. Therefore, this research addresses to improve the performance of electro-chemical discharge process in mesoscale drilling operations. For this purpose, hollow electrodes with high-pressure electrolyte injection system are employed to provide the electrolyte to the machining area in deep holes. The experiments at various levels of pressure and electrode diameter were done. The results showed that by injection of electrolyte through the hollow cathode to the drilling area, material removal rate (MRR) and drilling speed increased. Also, mentioned effects rose by increasing the electrode diameter and injection pressure. Improvement the hole depth versus the effective pressure for different electrode diameters was about 50-70%. More injection pressure resulted in larger hole diameter and creation of conical shape hole.
ناشر
Database: Elsevier - ScienceDirect (ساینس دایرکت)
Journal: Journal of Materials Processing Technology - Volume 255, May 2018, Pages 665-672
Journal: Journal of Materials Processing Technology - Volume 255, May 2018, Pages 665-672
نویسندگان
F. Mehrabi, M. Farahnakian, S. Elhami, M.R. Razfar,