کد مقاله | کد نشریه | سال انتشار | مقاله انگلیسی | نسخه تمام متن |
---|---|---|---|---|
737485 | 1461897 | 2013 | 10 صفحه PDF | دانلود رایگان |
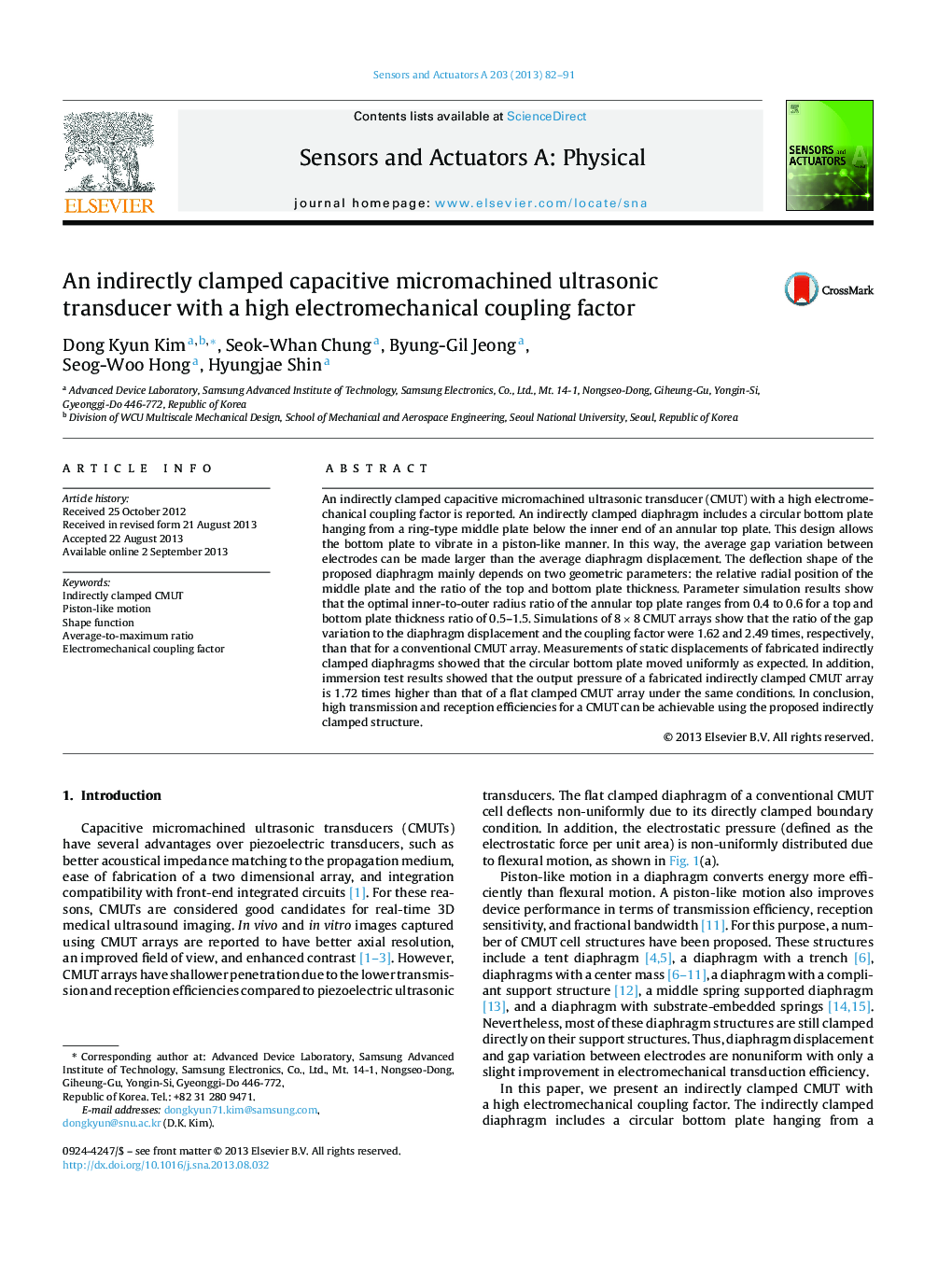
• An indirectly clamped capacitive micromachined ultrasonic transducer is presented.
• The gap variation between the electrodes can be larger than the diaphragm displacement due to the piston-like motion of the indirectly clamped diaphragm.
• Shape factors and average-to-maximum ratios are introduced to evaluate quantitatively the uniformity of the diaphragm deformation.
• This cell structure provides a high electromechanical coupling factor.
An indirectly clamped capacitive micromachined ultrasonic transducer (CMUT) with a high electromechanical coupling factor is reported. An indirectly clamped diaphragm includes a circular bottom plate hanging from a ring-type middle plate below the inner end of an annular top plate. This design allows the bottom plate to vibrate in a piston-like manner. In this way, the average gap variation between electrodes can be made larger than the average diaphragm displacement. The deflection shape of the proposed diaphragm mainly depends on two geometric parameters: the relative radial position of the middle plate and the ratio of the top and bottom plate thickness. Parameter simulation results show that the optimal inner-to-outer radius ratio of the annular top plate ranges from 0.4 to 0.6 for a top and bottom plate thickness ratio of 0.5–1.5. Simulations of 8 × 8 CMUT arrays show that the ratio of the gap variation to the diaphragm displacement and the coupling factor were 1.62 and 2.49 times, respectively, than that for a conventional CMUT array. Measurements of static displacements of fabricated indirectly clamped diaphragms showed that the circular bottom plate moved uniformly as expected. In addition, immersion test results showed that the output pressure of a fabricated indirectly clamped CMUT array is 1.72 times higher than that of a flat clamped CMUT array under the same conditions. In conclusion, high transmission and reception efficiencies for a CMUT can be achievable using the proposed indirectly clamped structure.
Journal: Sensors and Actuators A: Physical - Volume 203, 1 December 2013, Pages 82–91