کد مقاله | کد نشریه | سال انتشار | مقاله انگلیسی | نسخه تمام متن |
---|---|---|---|---|
739538 | 894099 | 2012 | 8 صفحه PDF | دانلود رایگان |
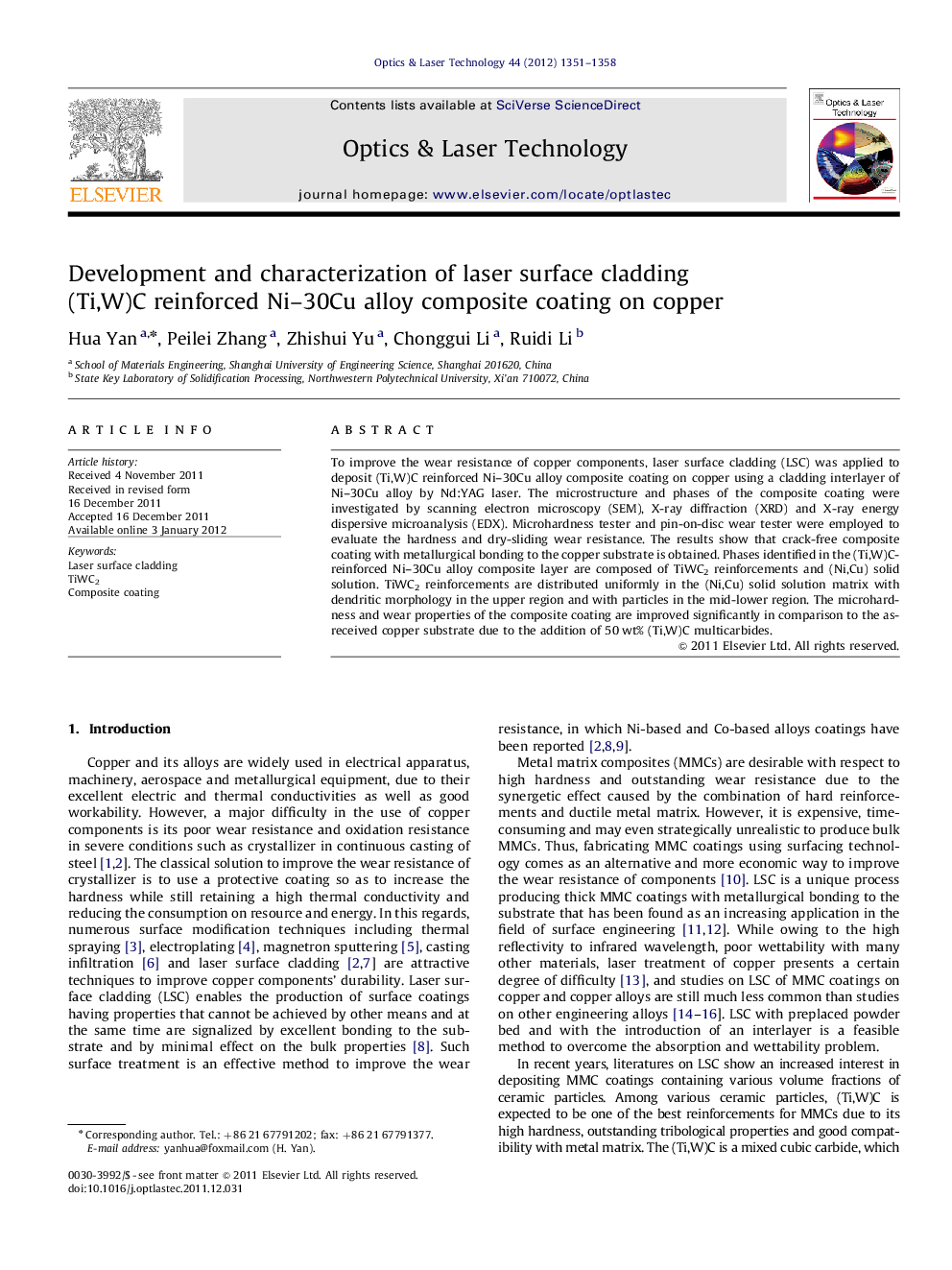
To improve the wear resistance of copper components, laser surface cladding (LSC) was applied to deposit (Ti,W)C reinforced Ni–30Cu alloy composite coating on copper using a cladding interlayer of Ni–30Cu alloy by Nd:YAG laser. The microstructure and phases of the composite coating were investigated by scanning electron microscopy (SEM), X-ray diffraction (XRD) and X-ray energy dispersive microanalysis (EDX). Microhardness tester and pin-on-disc wear tester were employed to evaluate the hardness and dry-sliding wear resistance. The results show that crack-free composite coating with metallurgical bonding to the copper substrate is obtained. Phases identified in the (Ti,W)C-reinforced Ni–30Cu alloy composite layer are composed of TiWC2 reinforcements and (Ni,Cu) solid solution. TiWC2 reinforcements are distributed uniformly in the (Ni,Cu) solid solution matrix with dendritic morphology in the upper region and with particles in the mid-lower region. The microhardness and wear properties of the composite coating are improved significantly in comparison to the as-received copper substrate due to the addition of 50 wt% (Ti,W)C multicarbides.
► (Ti,W)C reinforced Ni-based alloy composite coating was successfully fabricated on copper by cladding an interlayer.
► Average hardness value about 811.8HV0.1 of the MMC layer was obtained, almost 9 times that of the copper substrate.
► The relative wear resistance of the MMC coating was about 20 times than that of the copper.
Journal: Optics & Laser Technology - Volume 44, Issue 5, July 2012, Pages 1351–1358