کد مقاله | کد نشریه | سال انتشار | مقاله انگلیسی | نسخه تمام متن |
---|---|---|---|---|
778901 | 1464517 | 2013 | 10 صفحه PDF | دانلود رایگان |
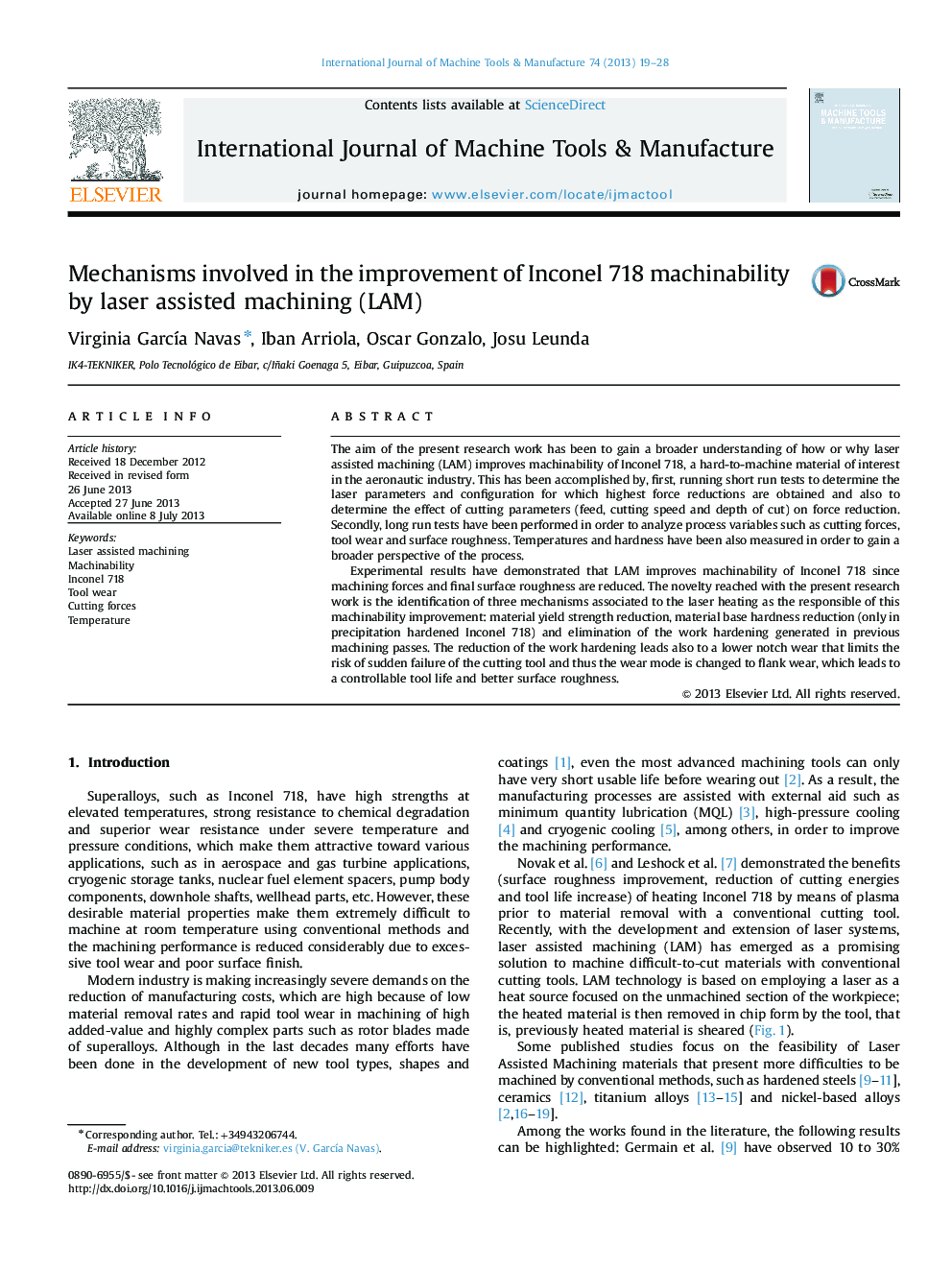
• Mechanisms responsible of machinability improvement in LAM of Inconel 718: yield strength reduction, annealing and elimination of work hardening.
• LAM improves machinability of Inconel 718; machining forces and final surface roughness are reduced.
• In LAM tool wear mode is changed to flank wear (notch and chipping are avoided).
The aim of the present research work has been to gain a broader understanding of how or why laser assisted machining (LAM) improves machinability of Inconel 718, a hard-to-machine material of interest in the aeronautic industry. This has been accomplished by, first, running short run tests to determine the laser parameters and configuration for which highest force reductions are obtained and also to determine the effect of cutting parameters (feed, cutting speed and depth of cut) on force reduction. Secondly, long run tests have been performed in order to analyze process variables such as cutting forces, tool wear and surface roughness. Temperatures and hardness have been also measured in order to gain a broader perspective of the process.Experimental results have demonstrated that LAM improves machinability of Inconel 718 since machining forces and final surface roughness are reduced. The novelty reached with the present research work is the identification of three mechanisms associated to the laser heating as the responsible of this machinability improvement: material yield strength reduction, material base hardness reduction (only in precipitation hardened Inconel 718) and elimination of the work hardening generated in previous machining passes. The reduction of the work hardening leads also to a lower notch wear that limits the risk of sudden failure of the cutting tool and thus the wear mode is changed to flank wear, which leads to a controllable tool life and better surface roughness.
Journal: International Journal of Machine Tools and Manufacture - Volume 74, November 2013, Pages 19–28