کد مقاله | کد نشریه | سال انتشار | مقاله انگلیسی | نسخه تمام متن |
---|---|---|---|---|
778905 | 1464517 | 2013 | 9 صفحه PDF | دانلود رایگان |
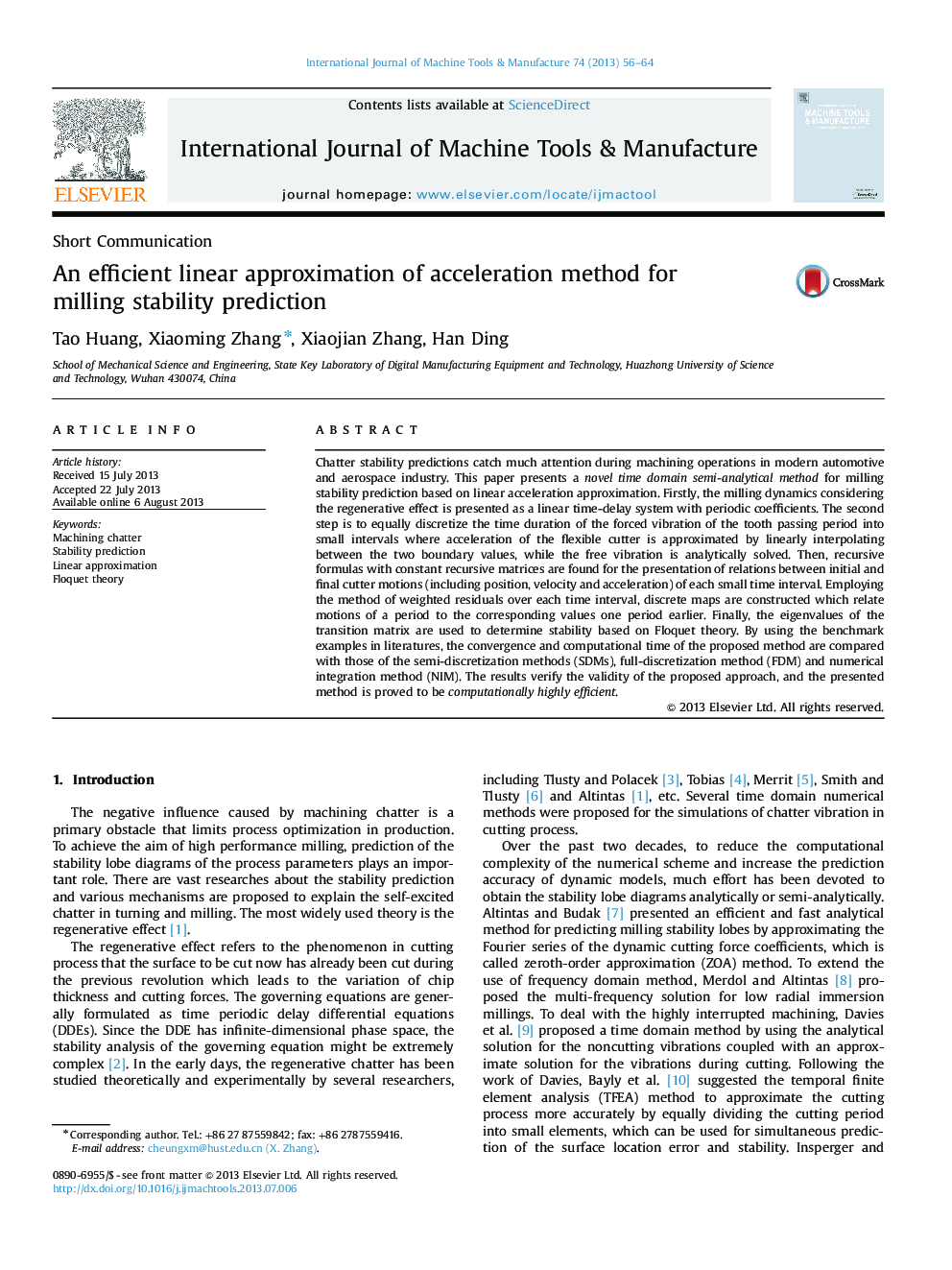
• This paper presents a novel time domain semi-analytical method for milling stability prediction based on linear acceleration approximation.
• The motion acceleration of the cutter is approximated by linearly interpolating between the two boundary values of small time interval.
• The calculation of matrix exponentials is unnecessary in the proposed method.
• The dimension of the transition matrix in this method is relatively small comparing with the existing methods.
• The results verify the validity of the proposed approach, and the presented method is proved to be highly efficient.
Chatter stability predictions catch much attention during machining operations in modern automotive and aerospace industry. This paper presents a novel time domain semi-analytical method for milling stability prediction based on linear acceleration approximation. Firstly, the milling dynamics considering the regenerative effect is presented as a linear time-delay system with periodic coefficients. The second step is to equally discretize the time duration of the forced vibration of the tooth passing period into small intervals where acceleration of the flexible cutter is approximated by linearly interpolating between the two boundary values, while the free vibration is analytically solved. Then, recursive formulas with constant recursive matrices are found for the presentation of relations between initial and final cutter motions (including position, velocity and acceleration) of each small time interval. Employing the method of weighted residuals over each time interval, discrete maps are constructed which relate motions of a period to the corresponding values one period earlier. Finally, the eigenvalues of the transition matrix are used to determine stability based on Floquet theory. By using the benchmark examples in literatures, the convergence and computational time of the proposed method are compared with those of the semi-discretization methods (SDMs), full-discretization method (FDM) and numerical integration method (NIM). The results verify the validity of the proposed approach, and the presented method is proved to be computationally highly efficient.
Journal: International Journal of Machine Tools and Manufacture - Volume 74, November 2013, Pages 56–64