کد مقاله | کد نشریه | سال انتشار | مقاله انگلیسی | نسخه تمام متن |
---|---|---|---|---|
778906 | 1464517 | 2013 | 9 صفحه PDF | دانلود رایگان |
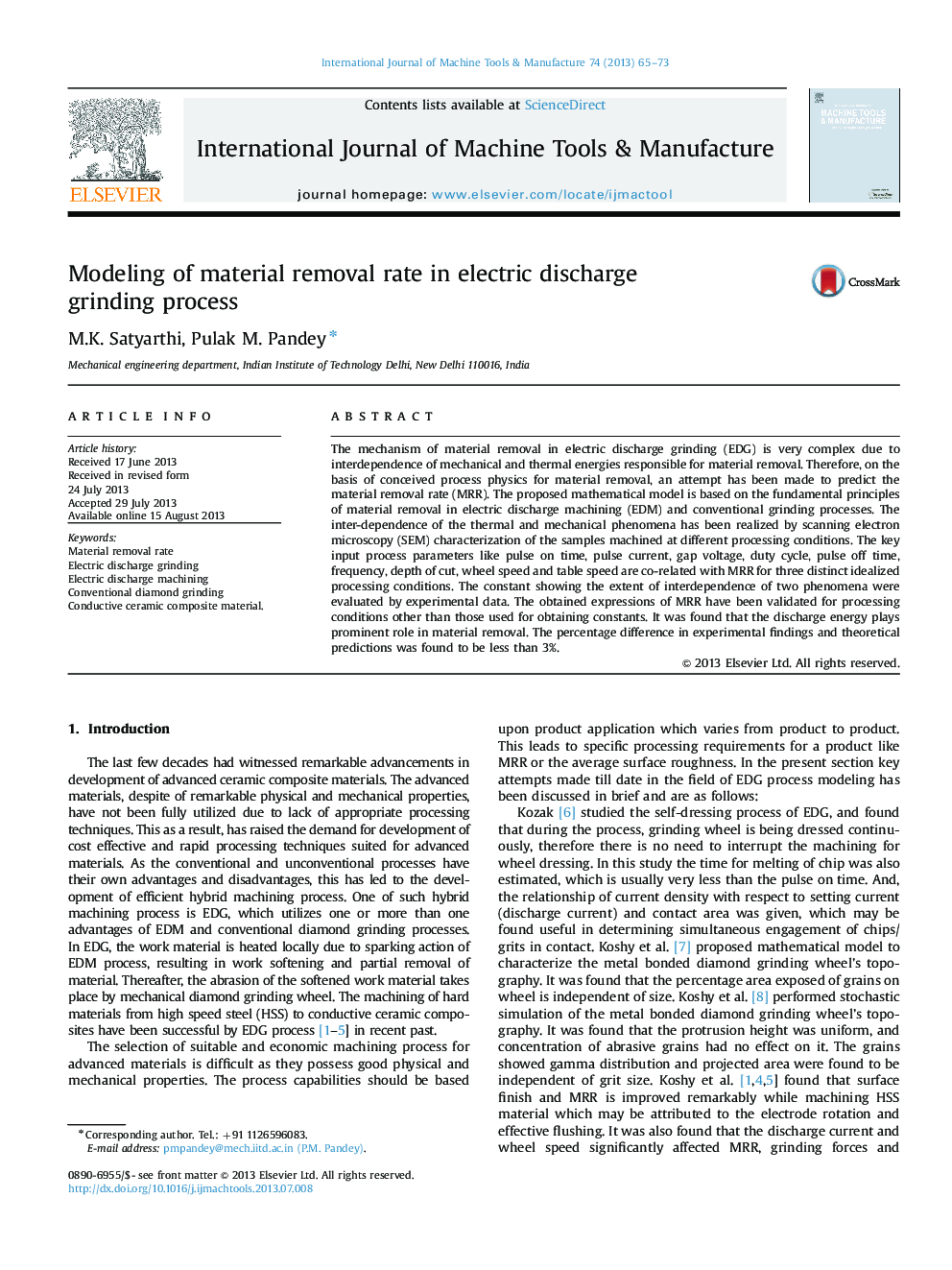
• The material removal rate for EDG has been modelled based on material removal rates for grinding and EDM processes.
• The dominance of machining mode (grinding, EDM or combination of the two) has been identified for MRR.
• The white layer has been considered to be proportional to discharge energy of a spark.
• The various constants of the MRR model were determined by non-linear estimation of processing conditions and responses.
• The maximum difference in predicted values of MRR and experimental value of MRR was found to be 2.75%.
The mechanism of material removal in electric discharge grinding (EDG) is very complex due to interdependence of mechanical and thermal energies responsible for material removal. Therefore, on the basis of conceived process physics for material removal, an attempt has been made to predict the material removal rate (MRR). The proposed mathematical model is based on the fundamental principles of material removal in electric discharge machining (EDM) and conventional grinding processes. The inter-dependence of the thermal and mechanical phenomena has been realized by scanning electron microscopy (SEM) characterization of the samples machined at different processing conditions. The key input process parameters like pulse on time, pulse current, gap voltage, duty cycle, pulse off time, frequency, depth of cut, wheel speed and table speed are co-related with MRR for three distinct idealized processing conditions. The constant showing the extent of interdependence of two phenomena were evaluated by experimental data. The obtained expressions of MRR have been validated for processing conditions other than those used for obtaining constants. It was found that the discharge energy plays prominent role in material removal. The percentage difference in experimental findings and theoretical predictions was found to be less than 3%.
Journal: International Journal of Machine Tools and Manufacture - Volume 74, November 2013, Pages 65–73