کد مقاله | کد نشریه | سال انتشار | مقاله انگلیسی | نسخه تمام متن |
---|---|---|---|---|
779078 | 1464605 | 2006 | 15 صفحه PDF | دانلود رایگان |
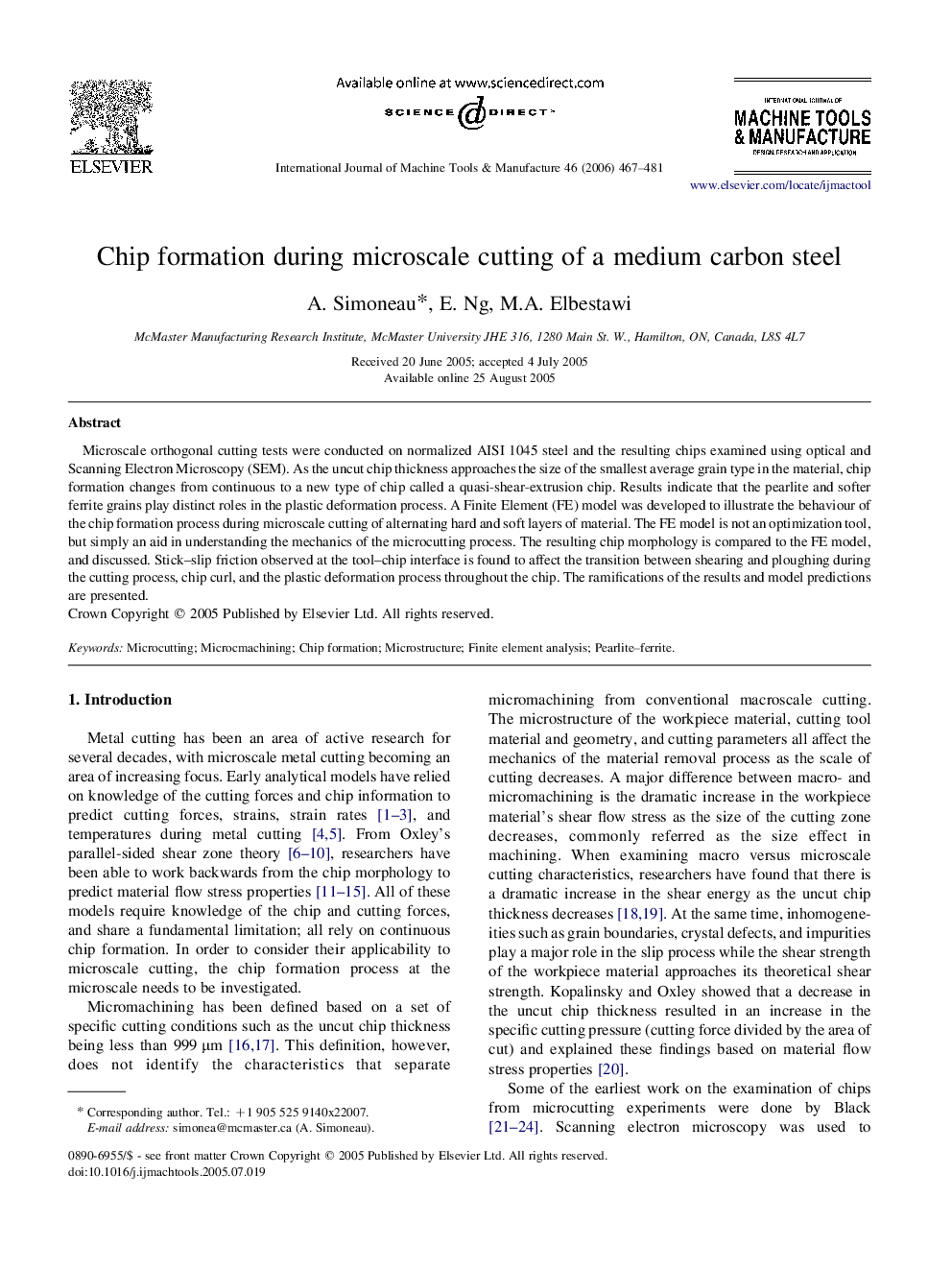
Microscale orthogonal cutting tests were conducted on normalized AISI 1045 steel and the resulting chips examined using optical and Scanning Electron Microscopy (SEM). As the uncut chip thickness approaches the size of the smallest average grain type in the material, chip formation changes from continuous to a new type of chip called a quasi-shear-extrusion chip. Results indicate that the pearlite and softer ferrite grains play distinct roles in the plastic deformation process. A Finite Element (FE) model was developed to illustrate the behaviour of the chip formation process during microscale cutting of alternating hard and soft layers of material. The FE model is not an optimization tool, but simply an aid in understanding the mechanics of the microcutting process. The resulting chip morphology is compared to the FE model, and discussed. Stick–slip friction observed at the tool–chip interface is found to affect the transition between shearing and ploughing during the cutting process, chip curl, and the plastic deformation process throughout the chip. The ramifications of the results and model predictions are presented.
Journal: International Journal of Machine Tools and Manufacture - Volume 46, Issue 5, April 2006, Pages 467–481