کد مقاله | کد نشریه | سال انتشار | مقاله انگلیسی | نسخه تمام متن |
---|---|---|---|---|
780409 | 1464485 | 2016 | 14 صفحه PDF | دانلود رایگان |
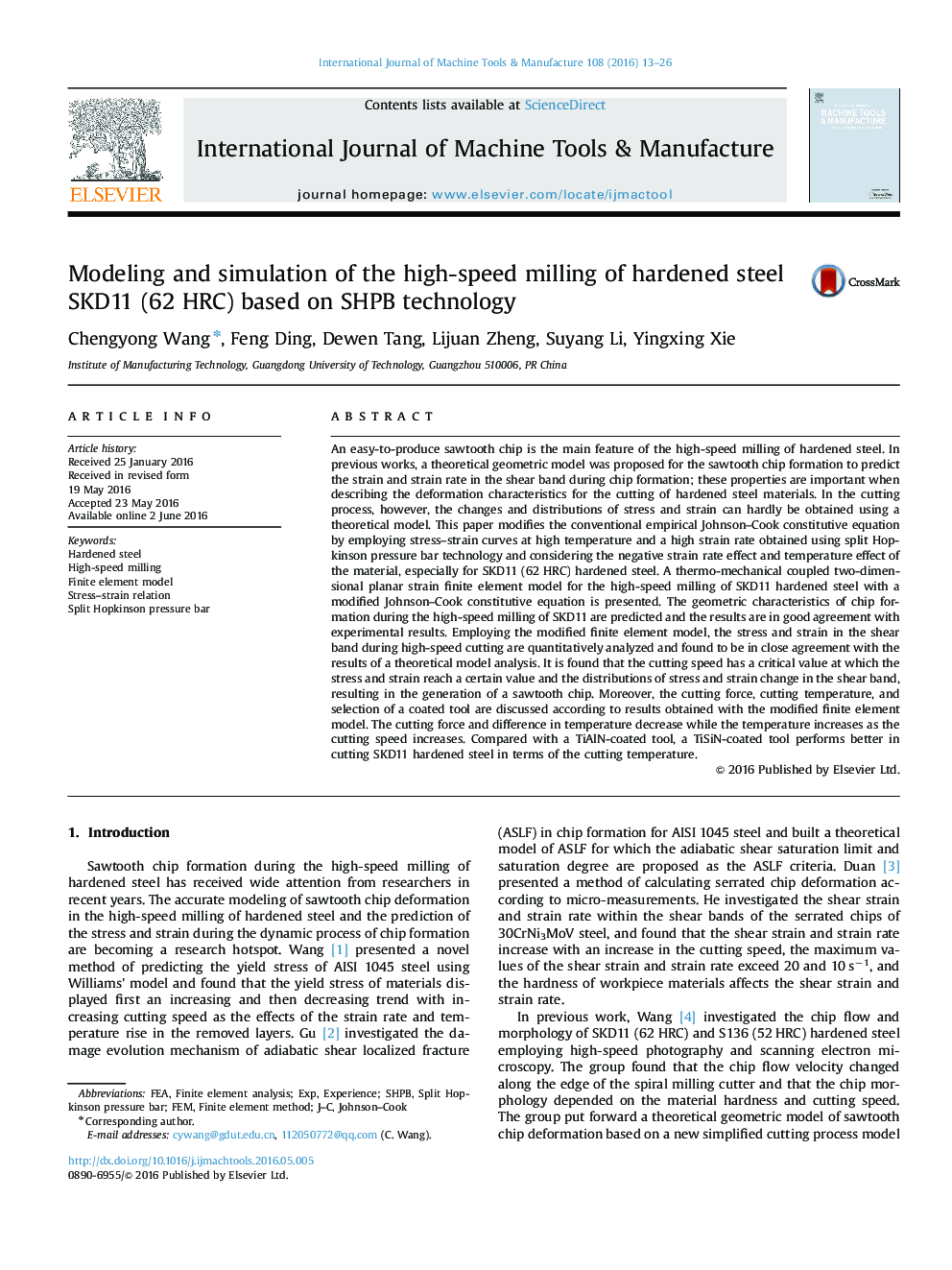
• A stress–strain curve of hardened steel material is obtained with SHPB technology.
• A negative strain rate effect and temperature effect are considered.
• The conventional empirical Johnson–Cook constitutive equation is thus modified.
• A 2D finite element model for high-speed milling predicts chip formation.
• Stress–strain is obtained in the shear band during continuous chip transformation.
An easy-to-produce sawtooth chip is the main feature of the high-speed milling of hardened steel. In previous works, a theoretical geometric model was proposed for the sawtooth chip formation to predict the strain and strain rate in the shear band during chip formation; these properties are important when describing the deformation characteristics for the cutting of hardened steel materials. In the cutting process, however, the changes and distributions of stress and strain can hardly be obtained using a theoretical model. This paper modifies the conventional empirical Johnson–Cook constitutive equation by employing stress–strain curves at high temperature and a high strain rate obtained using split Hopkinson pressure bar technology and considering the negative strain rate effect and temperature effect of the material, especially for SKD11 (62 HRC) hardened steel. A thermo-mechanical coupled two-dimensional planar strain finite element model for the high-speed milling of SKD11 hardened steel with a modified Johnson–Cook constitutive equation is presented. The geometric characteristics of chip formation during the high-speed milling of SKD11 are predicted and the results are in good agreement with experimental results. Employing the modified finite element model, the stress and strain in the shear band during high-speed cutting are quantitatively analyzed and found to be in close agreement with the results of a theoretical model analysis. It is found that the cutting speed has a critical value at which the stress and strain reach a certain value and the distributions of stress and strain change in the shear band, resulting in the generation of a sawtooth chip. Moreover, the cutting force, cutting temperature, and selection of a coated tool are discussed according to results obtained with the modified finite element model. The cutting force and difference in temperature decrease while the temperature increases as the cutting speed increases. Compared with a TiAlN-coated tool, a TiSiN-coated tool performs better in cutting SKD11 hardened steel in terms of the cutting temperature.
Journal: International Journal of Machine Tools and Manufacture - Volume 108, September 2016, Pages 13–26