کد مقاله | کد نشریه | سال انتشار | مقاله انگلیسی | نسخه تمام متن |
---|---|---|---|---|
781039 | 1464574 | 2008 | 9 صفحه PDF | دانلود رایگان |
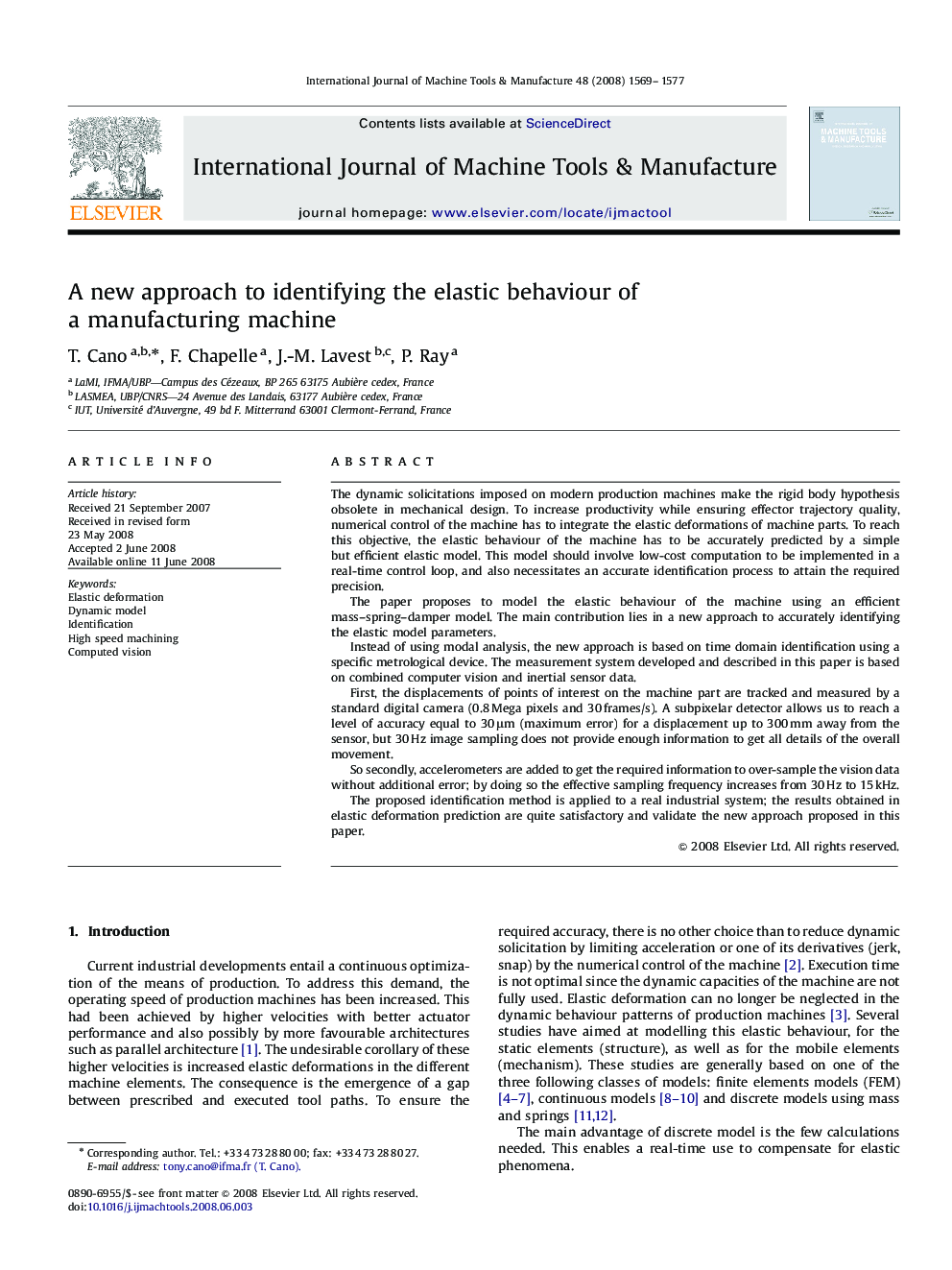
The dynamic solicitations imposed on modern production machines make the rigid body hypothesis obsolete in mechanical design. To increase productivity while ensuring effector trajectory quality, numerical control of the machine has to integrate the elastic deformations of machine parts. To reach this objective, the elastic behaviour of the machine has to be accurately predicted by a simple but efficient elastic model. This model should involve low-cost computation to be implemented in a real-time control loop, and also necessitates an accurate identification process to attain the required precision.The paper proposes to model the elastic behaviour of the machine using an efficient mass–spring–damper model. The main contribution lies in a new approach to accurately identifying the elastic model parameters.Instead of using modal analysis, the new approach is based on time domain identification using a specific metrological device. The measurement system developed and described in this paper is based on combined computer vision and inertial sensor data.First, the displacements of points of interest on the machine part are tracked and measured by a standard digital camera (0.8 Mega pixels and 30 frames/s). A subpixelar detector allows us to reach a level of accuracy equal to 30 μm (maximum error) for a displacement up to 300 mm away from the sensor, but 30 Hz image sampling does not provide enough information to get all details of the overall movement.So secondly, accelerometers are added to get the required information to over-sample the vision data without additional error; by doing so the effective sampling frequency increases from 30 Hz to 15 kHz.The proposed identification method is applied to a real industrial system; the results obtained in elastic deformation prediction are quite satisfactory and validate the new approach proposed in this paper.
Journal: International Journal of Machine Tools and Manufacture - Volume 48, Issue 14, November 2008, Pages 1569–1577