کد مقاله | کد نشریه | سال انتشار | مقاله انگلیسی | نسخه تمام متن |
---|---|---|---|---|
781717 | 1464525 | 2013 | 16 صفحه PDF | دانلود رایگان |
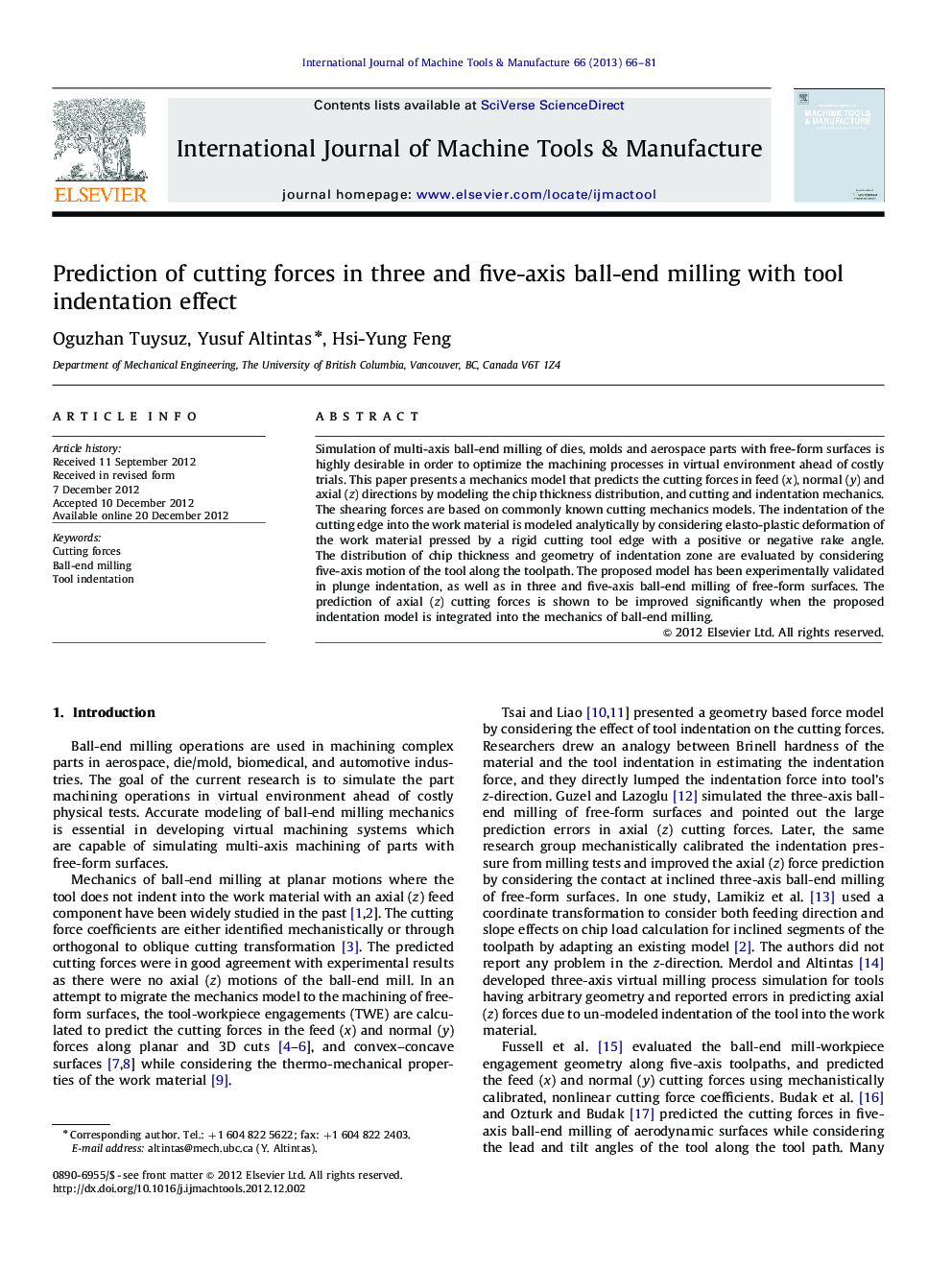
Simulation of multi-axis ball-end milling of dies, molds and aerospace parts with free-form surfaces is highly desirable in order to optimize the machining processes in virtual environment ahead of costly trials. This paper presents a mechanics model that predicts the cutting forces in feed (x), normal (y) and axial (z) directions by modeling the chip thickness distribution, and cutting and indentation mechanics. The shearing forces are based on commonly known cutting mechanics models. The indentation of the cutting edge into the work material is modeled analytically by considering elasto-plastic deformation of the work material pressed by a rigid cutting tool edge with a positive or negative rake angle. The distribution of chip thickness and geometry of indentation zone are evaluated by considering five-axis motion of the tool along the toolpath. The proposed model has been experimentally validated in plunge indentation, as well as in three and five-axis ball-end milling of free-form surfaces. The prediction of axial (z) cutting forces is shown to be improved significantly when the proposed indentation model is integrated into the mechanics of ball-end milling.
► An improved axial cutting force model for 5-axis ball-end milling is presented.
► A new analytical indentation force model has been proposed.
► The effect of tool inclination on chip thickness has been modeled.
► Cutting edge indentation has also been modeled through finite element analysis.
Journal: International Journal of Machine Tools and Manufacture - Volume 66, March 2013, Pages 66–81