کد مقاله | کد نشریه | سال انتشار | مقاله انگلیسی | نسخه تمام متن |
---|---|---|---|---|
782045 | 1464591 | 2007 | 12 صفحه PDF | دانلود رایگان |
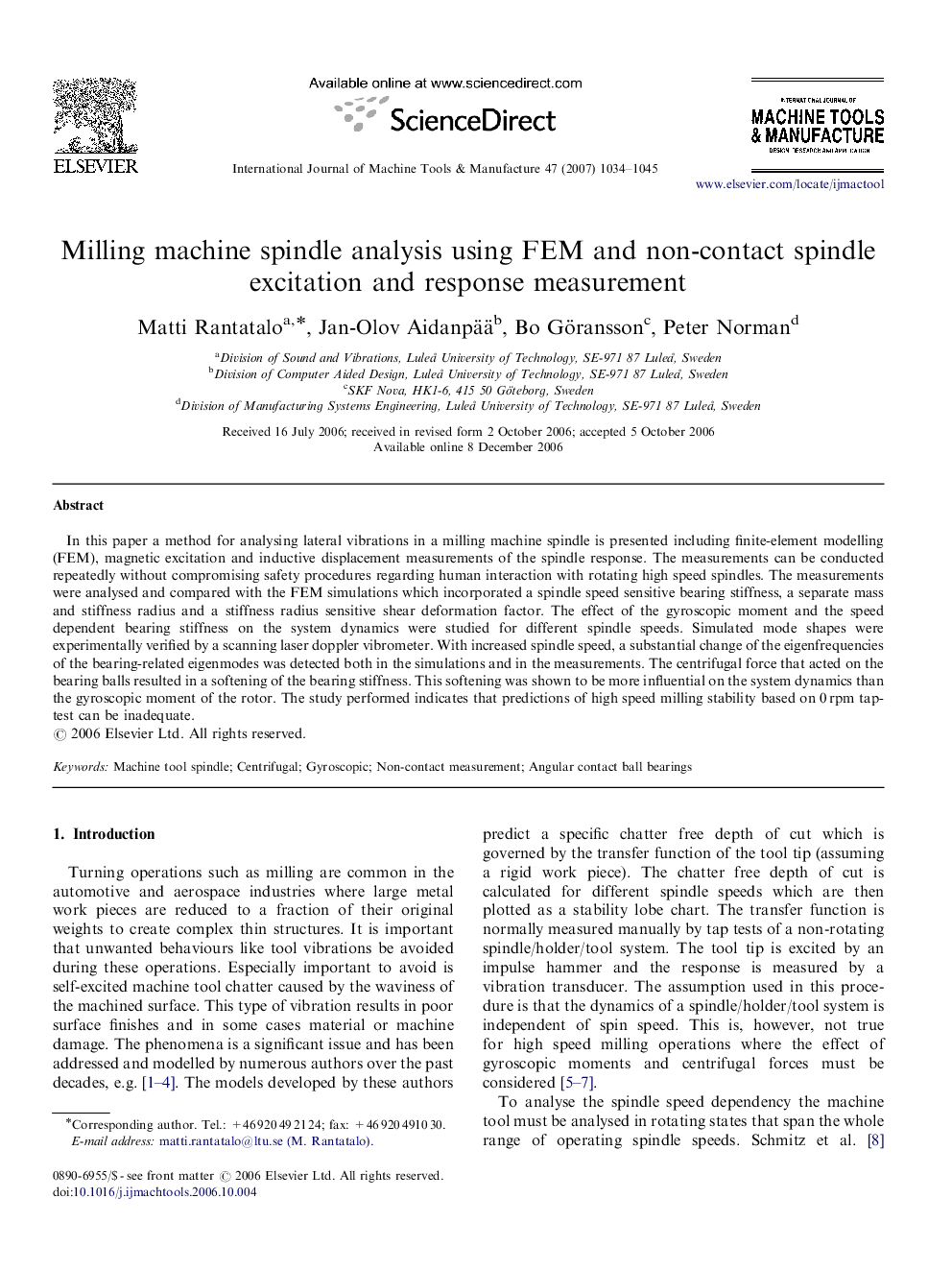
In this paper a method for analysing lateral vibrations in a milling machine spindle is presented including finite-element modelling (FEM), magnetic excitation and inductive displacement measurements of the spindle response. The measurements can be conducted repeatedly without compromising safety procedures regarding human interaction with rotating high speed spindles. The measurements were analysed and compared with the FEM simulations which incorporated a spindle speed sensitive bearing stiffness, a separate mass and stiffness radius and a stiffness radius sensitive shear deformation factor. The effect of the gyroscopic moment and the speed dependent bearing stiffness on the system dynamics were studied for different spindle speeds. Simulated mode shapes were experimentally verified by a scanning laser doppler vibrometer. With increased spindle speed, a substantial change of the eigenfrequencies of the bearing-related eigenmodes was detected both in the simulations and in the measurements. The centrifugal force that acted on the bearing balls resulted in a softening of the bearing stiffness. This softening was shown to be more influential on the system dynamics than the gyroscopic moment of the rotor. The study performed indicates that predictions of high speed milling stability based on 0 rpm tap-test can be inadequate.
Journal: International Journal of Machine Tools and Manufacture - Volume 47, Issues 7–8, June 2007, Pages 1034–1045