کد مقاله | کد نشریه | سال انتشار | مقاله انگلیسی | نسخه تمام متن |
---|---|---|---|---|
782118 | 1464976 | 2016 | 14 صفحه PDF | دانلود رایگان |
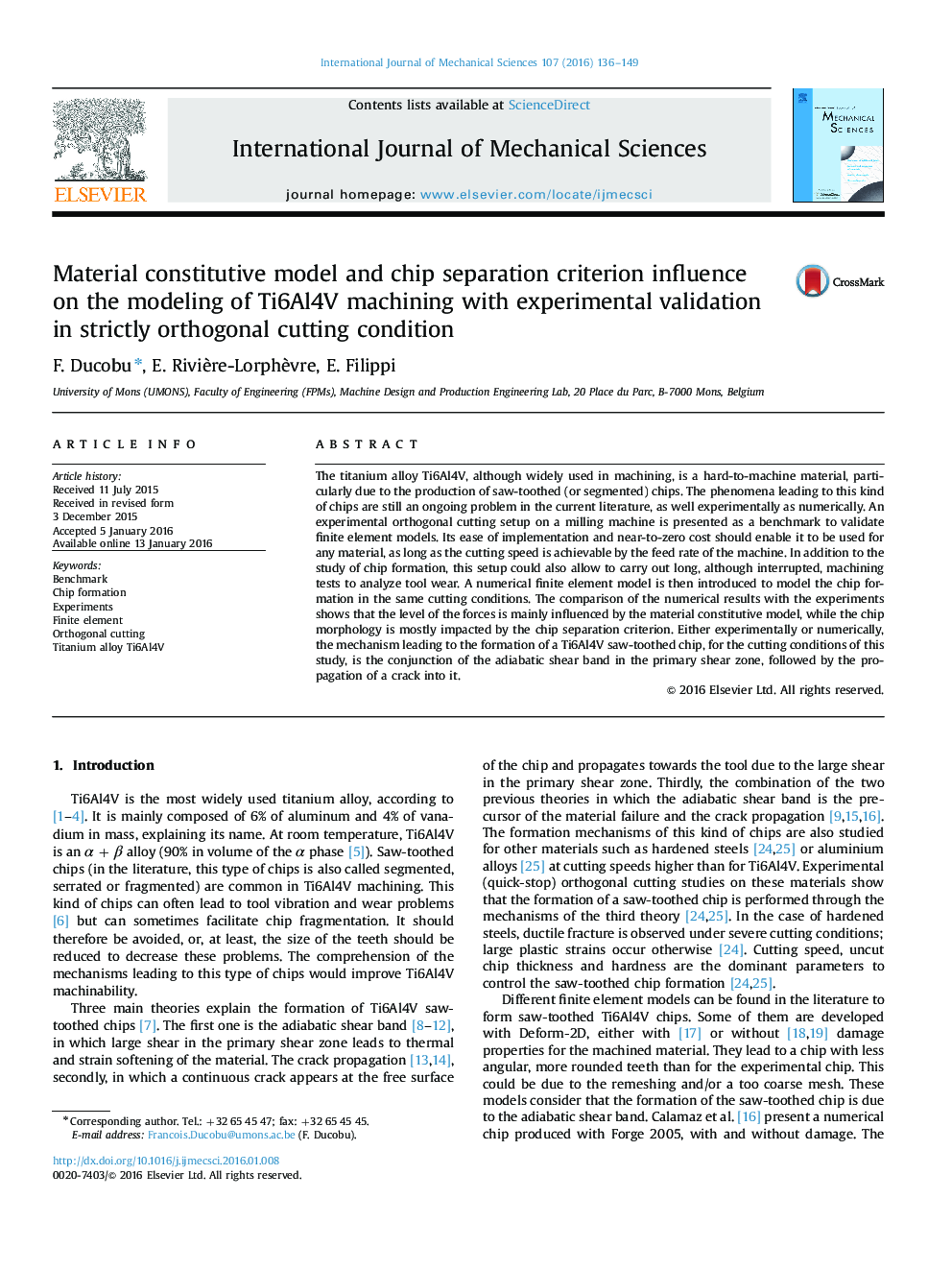
• Experimental benchmark for orthogonal cutting finite element models.
• Simple orthogonal cutting setup without chip deformation prior to observation.
• Comparison and improvement of a finite element model for Ti6Al4V.
• Behavior law mainly influences forces level and chip separation, chip morphology.
• Ti6Al4V saw-toothed chip formed by adiabatic shear band and crack propagation.
The titanium alloy Ti6Al4V, although widely used in machining, is a hard-to-machine material, particularly due to the production of saw-toothed (or segmented) chips. The phenomena leading to this kind of chips are still an ongoing problem in the current literature, as well experimentally as numerically. An experimental orthogonal cutting setup on a milling machine is presented as a benchmark to validate finite element models. Its ease of implementation and near-to-zero cost should enable it to be used for any material, as long as the cutting speed is achievable by the feed rate of the machine. In addition to the study of chip formation, this setup could also allow to carry out long, although interrupted, machining tests to analyze tool wear. A numerical finite element model is then introduced to model the chip formation in the same cutting conditions. The comparison of the numerical results with the experiments shows that the level of the forces is mainly influenced by the material constitutive model, while the chip morphology is mostly impacted by the chip separation criterion. Either experimentally or numerically, the mechanism leading to the formation of a Ti6Al4V saw-toothed chip, for the cutting conditions of this study, is the conjunction of the adiabatic shear band in the primary shear zone, followed by the propagation of a crack into it.
Journal: International Journal of Mechanical Sciences - Volume 107, March 2016, Pages 136–149