کد مقاله | کد نشریه | سال انتشار | مقاله انگلیسی | نسخه تمام متن |
---|---|---|---|---|
783157 | 1464110 | 2012 | 10 صفحه PDF | دانلود رایگان |
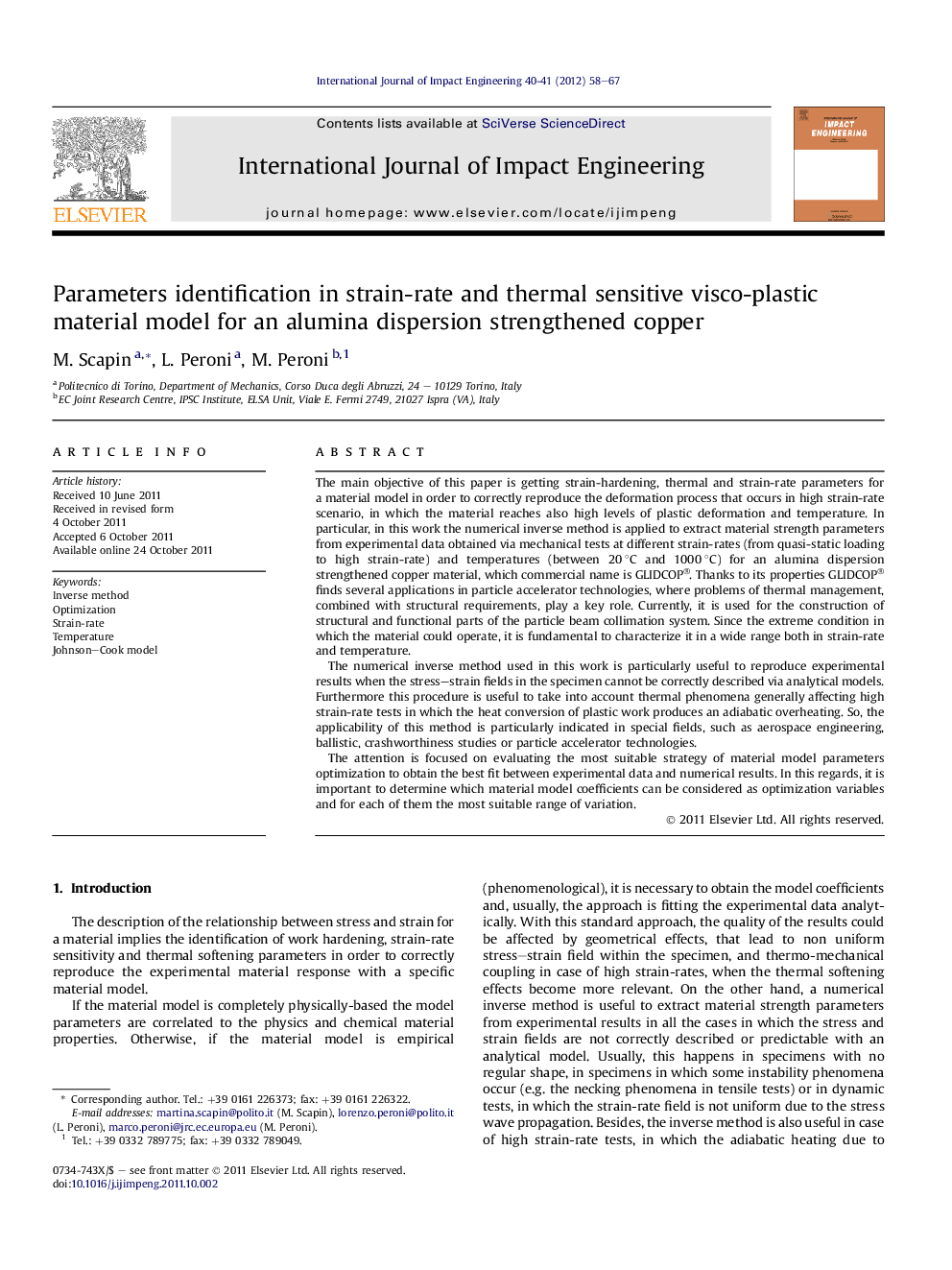
The main objective of this paper is getting strain-hardening, thermal and strain-rate parameters for a material model in order to correctly reproduce the deformation process that occurs in high strain-rate scenario, in which the material reaches also high levels of plastic deformation and temperature. In particular, in this work the numerical inverse method is applied to extract material strength parameters from experimental data obtained via mechanical tests at different strain-rates (from quasi-static loading to high strain-rate) and temperatures (between 20 °C and 1000 °C) for an alumina dispersion strengthened copper material, which commercial name is GLIDCOP®. Thanks to its properties GLIDCOP® finds several applications in particle accelerator technologies, where problems of thermal management, combined with structural requirements, play a key role. Currently, it is used for the construction of structural and functional parts of the particle beam collimation system. Since the extreme condition in which the material could operate, it is fundamental to characterize it in a wide range both in strain-rate and temperature.The numerical inverse method used in this work is particularly useful to reproduce experimental results when the stress–strain fields in the specimen cannot be correctly described via analytical models. Furthermore this procedure is useful to take into account thermal phenomena generally affecting high strain-rate tests in which the heat conversion of plastic work produces an adiabatic overheating. So, the applicability of this method is particularly indicated in special fields, such as aerospace engineering, ballistic, crashworthiness studies or particle accelerator technologies.The attention is focused on evaluating the most suitable strategy of material model parameters optimization to obtain the best fit between experimental data and numerical results. In this regards, it is important to determine which material model coefficients can be considered as optimization variables and for each of them the most suitable range of variation.
► We investigate the mechanical behavior of alumina dispersion strengthened copper.
► Compression tests in a wide range in temperatures and strain-rates are performed.
► A numerical inverse method is applied for the investigation process.
► The parameters identification is focused on the Johnson–Cook material model.
Journal: International Journal of Impact Engineering - Volumes 40–41, February–March 2012, Pages 58–67