کد مقاله | کد نشریه | سال انتشار | مقاله انگلیسی | نسخه تمام متن |
---|---|---|---|---|
784427 | 1464527 | 2013 | 11 صفحه PDF | دانلود رایگان |
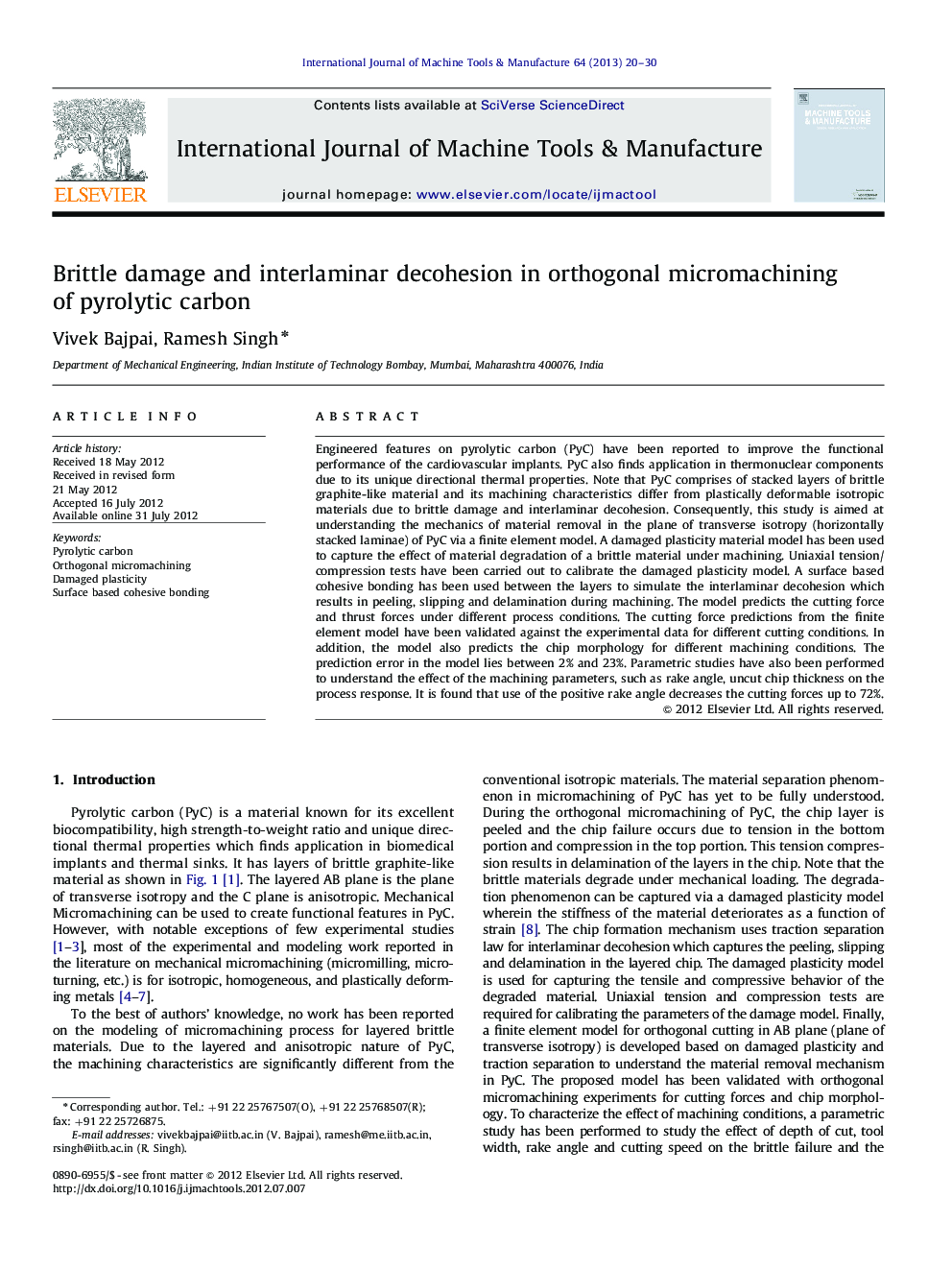
Engineered features on pyrolytic carbon (PyC) have been reported to improve the functional performance of the cardiovascular implants. PyC also finds application in thermonuclear components due to its unique directional thermal properties. Note that PyC comprises of stacked layers of brittle graphite-like material and its machining characteristics differ from plastically deformable isotropic materials due to brittle damage and interlaminar decohesion. Consequently, this study is aimed at understanding the mechanics of material removal in the plane of transverse isotropy (horizontally stacked laminae) of PyC via a finite element model. A damaged plasticity material model has been used to capture the effect of material degradation of a brittle material under machining. Uniaxial tension/compression tests have been carried out to calibrate the damaged plasticity model. A surface based cohesive bonding has been used between the layers to simulate the interlaminar decohesion which results in peeling, slipping and delamination during machining. The model predicts the cutting force and thrust forces under different process conditions. The cutting force predictions from the finite element model have been validated against the experimental data for different cutting conditions. In addition, the model also predicts the chip morphology for different machining conditions. The prediction error in the model lies between 2% and 23%. Parametric studies have also been performed to understand the effect of the machining parameters, such as rake angle, uncut chip thickness on the process response. It is found that use of the positive rake angle decreases the cutting forces up to 72%.
► Insight into brittle failure and interlaminar decohesion during micromachining of PyC.
► Peeling, slipping, debonding and progressive damage have been modeled.
► Rake angle, depth of cut and tool edge radius play major role in micromachining.
► FE model predictions errors lie between 2% and 23%.
Journal: International Journal of Machine Tools and Manufacture - Volume 64, January 2013, Pages 20–30