کد مقاله | کد نشریه | سال انتشار | مقاله انگلیسی | نسخه تمام متن |
---|---|---|---|---|
791422 | 901959 | 2009 | 7 صفحه PDF | دانلود رایگان |
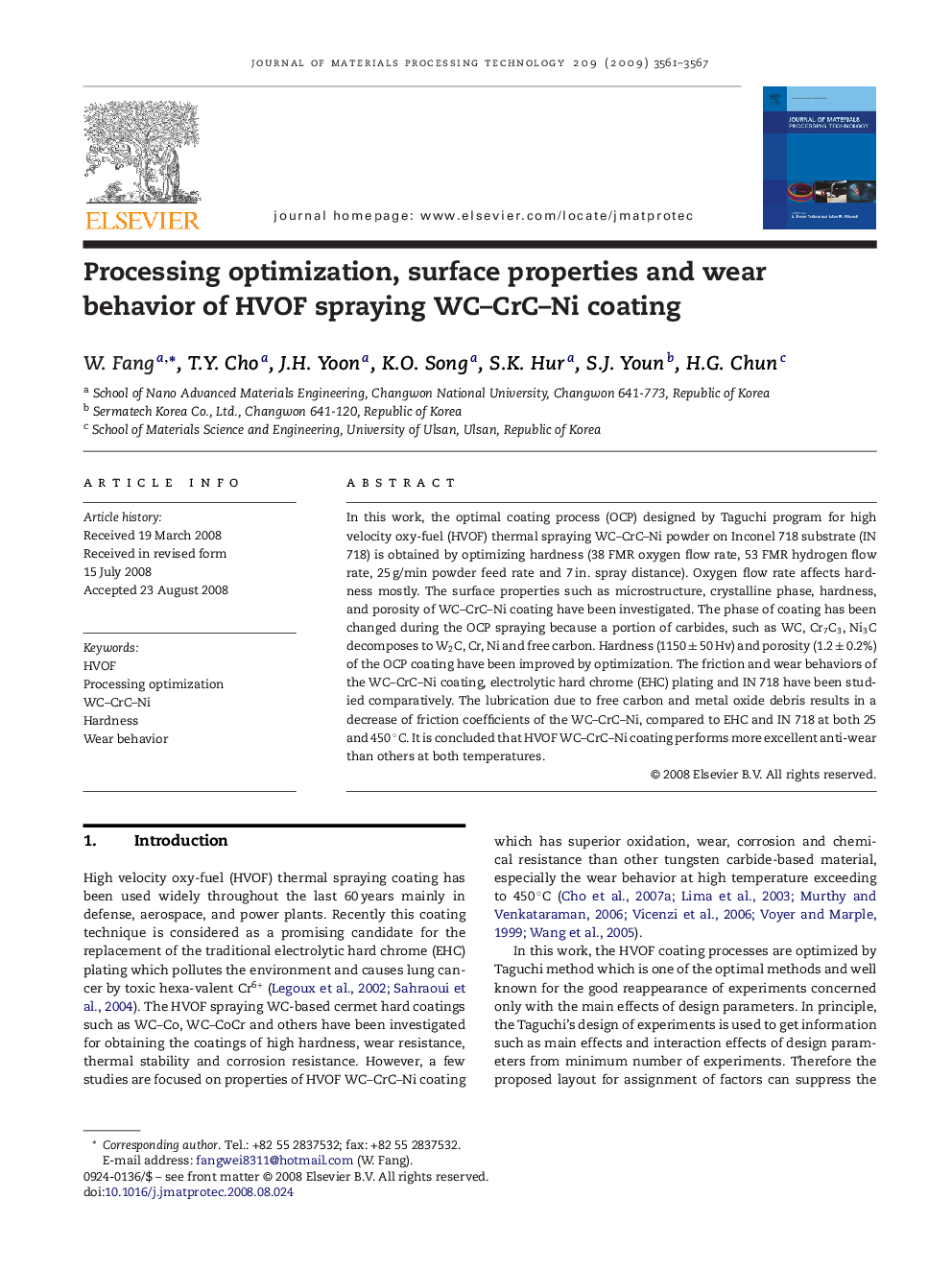
In this work, the optimal coating process (OCP) designed by Taguchi program for high velocity oxy-fuel (HVOF) thermal spraying WC–CrC–Ni powder on Inconel 718 substrate (IN 718) is obtained by optimizing hardness (38 FMR oxygen flow rate, 53 FMR hydrogen flow rate, 25 g/min powder feed rate and 7 in. spray distance). Oxygen flow rate affects hardness mostly. The surface properties such as microstructure, crystalline phase, hardness, and porosity of WC–CrC–Ni coating have been investigated. The phase of coating has been changed during the OCP spraying because a portion of carbides, such as WC, Cr7C3, Ni3C decomposes to W2C, Cr, Ni and free carbon. Hardness (1150 ± 50 Hv) and porosity (1.2 ± 0.2%) of the OCP coating have been improved by optimization. The friction and wear behaviors of the WC–CrC–Ni coating, electrolytic hard chrome (EHC) plating and IN 718 have been studied comparatively. The lubrication due to free carbon and metal oxide debris results in a decrease of friction coefficients of the WC–CrC–Ni, compared to EHC and IN 718 at both 25 and 450 °C. It is concluded that HVOF WC–CrC–Ni coating performs more excellent anti-wear than others at both temperatures.
Journal: Journal of Materials Processing Technology - Volume 209, Issue 7, 1 April 2009, Pages 3561–3567