کد مقاله | کد نشریه | سال انتشار | مقاله انگلیسی | نسخه تمام متن |
---|---|---|---|---|
793447 | 902425 | 2009 | 5 صفحه PDF | دانلود رایگان |
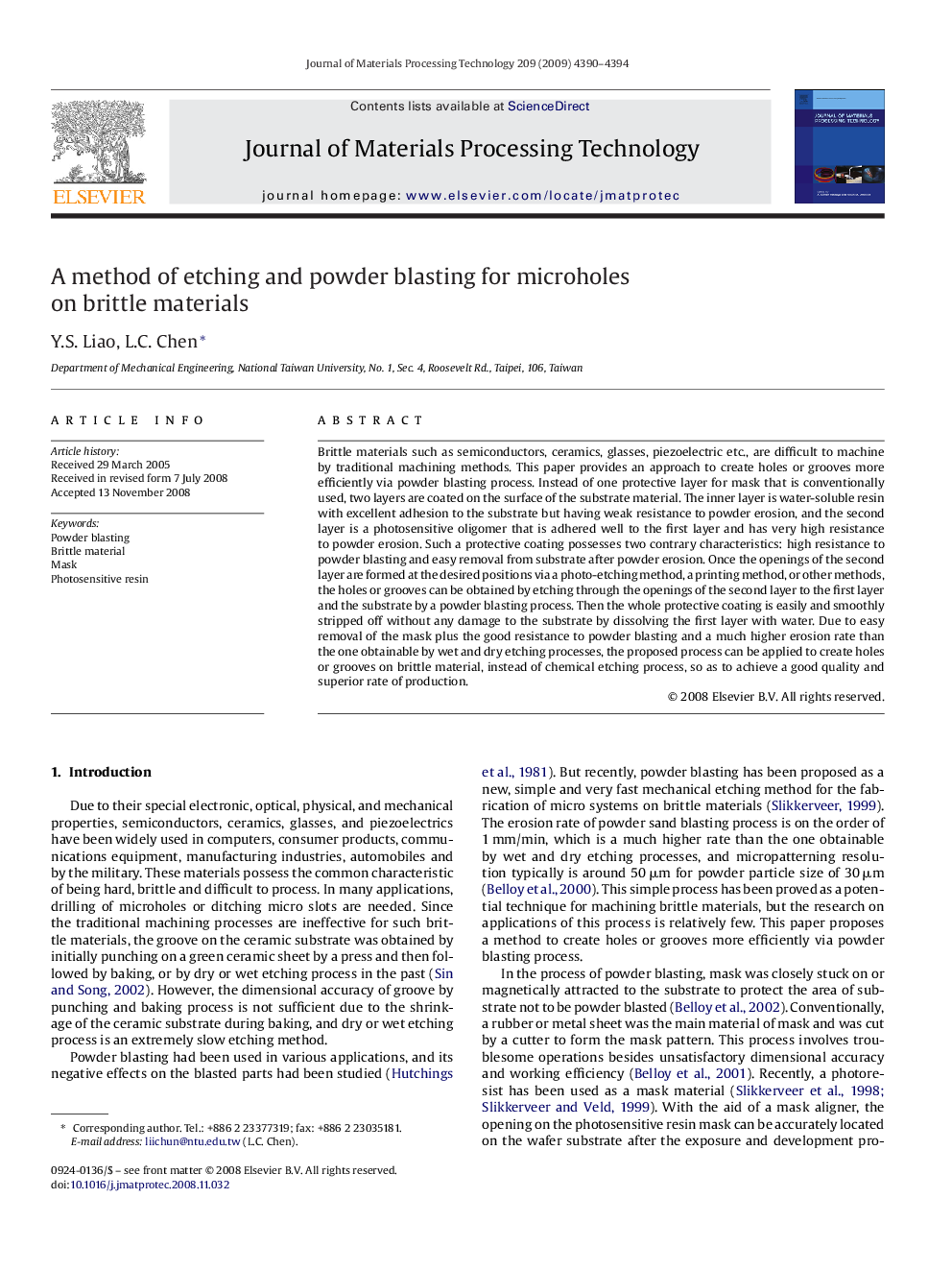
Brittle materials such as semiconductors, ceramics, glasses, piezoelectric etc., are difficult to machine by traditional machining methods. This paper provides an approach to create holes or grooves more efficiently via powder blasting process. Instead of one protective layer for mask that is conventionally used, two layers are coated on the surface of the substrate material. The inner layer is water-soluble resin with excellent adhesion to the substrate but having weak resistance to powder erosion, and the second layer is a photosensitive oligomer that is adhered well to the first layer and has very high resistance to powder erosion. Such a protective coating possesses two contrary characteristics: high resistance to powder blasting and easy removal from substrate after powder erosion. Once the openings of the second layer are formed at the desired positions via a photo-etching method, a printing method, or other methods, the holes or grooves can be obtained by etching through the openings of the second layer to the first layer and the substrate by a powder blasting process. Then the whole protective coating is easily and smoothly stripped off without any damage to the substrate by dissolving the first layer with water. Due to easy removal of the mask plus the good resistance to powder blasting and a much higher erosion rate than the one obtainable by wet and dry etching processes, the proposed process can be applied to create holes or grooves on brittle material, instead of chemical etching process, so as to achieve a good quality and superior rate of production.
Journal: Journal of Materials Processing Technology - Volume 209, Issue 9, 1 May 2009, Pages 4390–4394