کد مقاله | کد نشریه | سال انتشار | مقاله انگلیسی | نسخه تمام متن |
---|---|---|---|---|
794193 | 1466777 | 2007 | 5 صفحه PDF | دانلود رایگان |
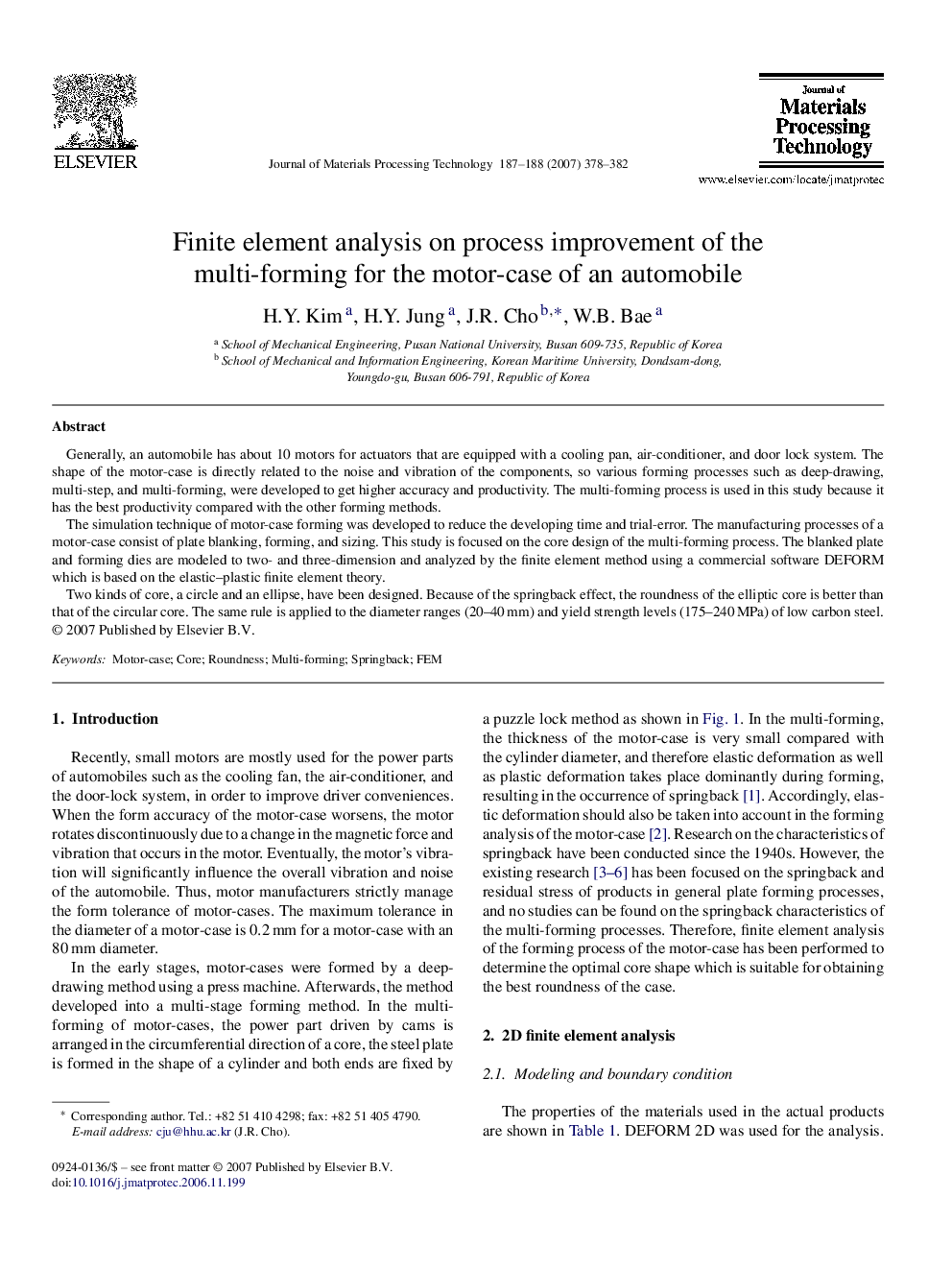
Generally, an automobile has about 10 motors for actuators that are equipped with a cooling pan, air-conditioner, and door lock system. The shape of the motor-case is directly related to the noise and vibration of the components, so various forming processes such as deep-drawing, multi-step, and multi-forming, were developed to get higher accuracy and productivity. The multi-forming process is used in this study because it has the best productivity compared with the other forming methods.The simulation technique of motor-case forming was developed to reduce the developing time and trial-error. The manufacturing processes of a motor-case consist of plate blanking, forming, and sizing. This study is focused on the core design of the multi-forming process. The blanked plate and forming dies are modeled to two- and three-dimension and analyzed by the finite element method using a commercial software DEFORM which is based on the elastic–plastic finite element theory.Two kinds of core, a circle and an ellipse, have been designed. Because of the springback effect, the roundness of the elliptic core is better than that of the circular core. The same rule is applied to the diameter ranges (20–40 mm) and yield strength levels (175–240 MPa) of low carbon steel.
Journal: Journal of Materials Processing Technology - Volumes 187–188, 12 June 2007, Pages 378–382