کد مقاله | کد نشریه | سال انتشار | مقاله انگلیسی | نسخه تمام متن |
---|---|---|---|---|
799778 | 1467772 | 2013 | 18 صفحه PDF | دانلود رایگان |
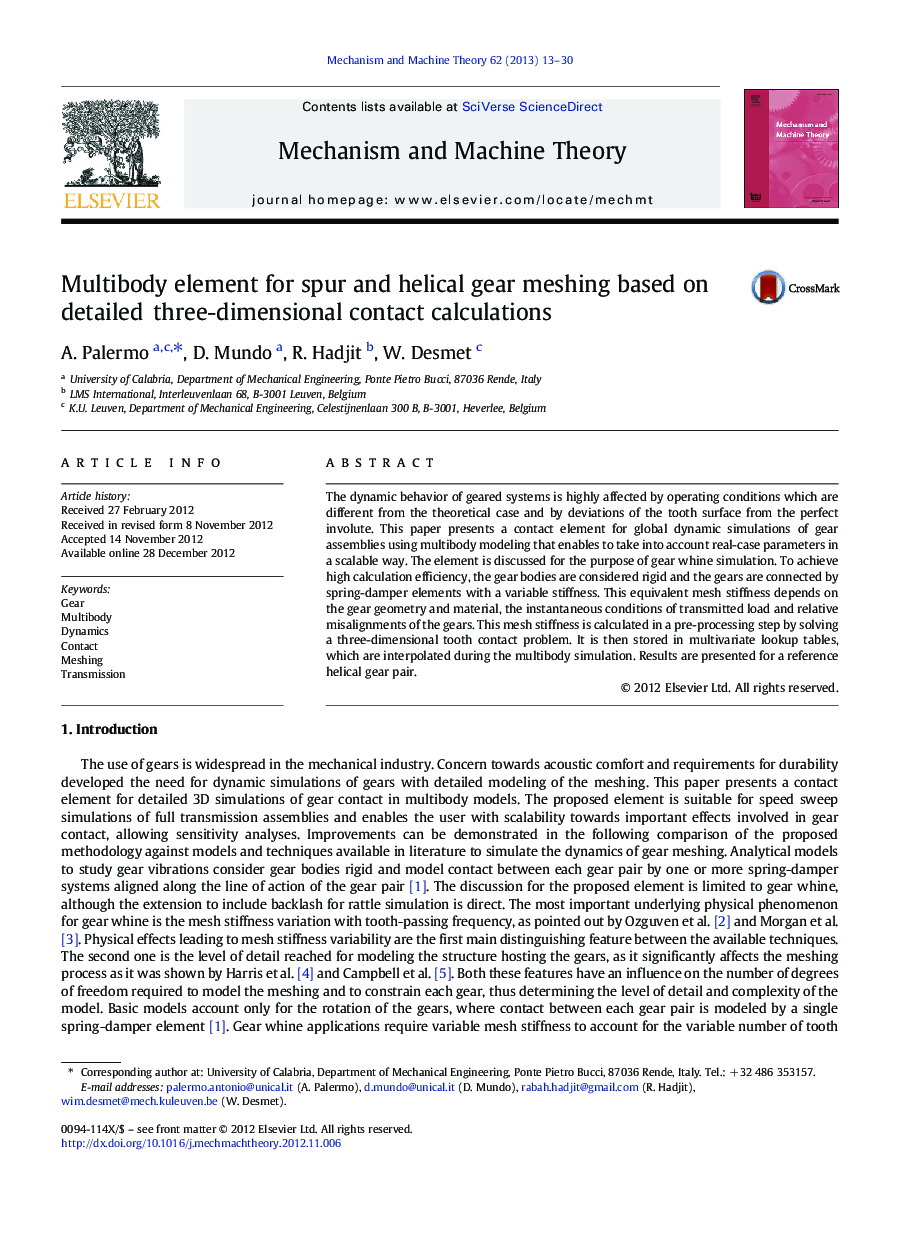
The dynamic behavior of geared systems is highly affected by operating conditions which are different from the theoretical case and by deviations of the tooth surface from the perfect involute. This paper presents a contact element for global dynamic simulations of gear assemblies using multibody modeling that enables to take into account real-case parameters in a scalable way. The element is discussed for the purpose of gear whine simulation. To achieve high calculation efficiency, the gear bodies are considered rigid and the gears are connected by spring-damper elements with a variable stiffness. This equivalent mesh stiffness depends on the gear geometry and material, the instantaneous conditions of transmitted load and relative misalignments of the gears. This mesh stiffness is calculated in a pre-processing step by solving a three-dimensional tooth contact problem. It is then stored in multivariate lookup tables, which are interpolated during the multibody simulation. Results are presented for a reference helical gear pair.
► A multibody element accounting for 3D contact in gear meshing dynamics is proposed.
► The element has scalable detail/complexity and can be included in a general MB model.
► Formulation based on multivariate look-up table to increase efficiency is discussed.
► Results are discussed for a helical gear pair with microgeometry corrections.
► Non-linear effects of load, angular misalignment and shuttling are shown and captured.
Journal: Mechanism and Machine Theory - Volume 62, April 2013, Pages 13–30