کد مقاله | کد نشریه | سال انتشار | مقاله انگلیسی | نسخه تمام متن |
---|---|---|---|---|
8047855 | 1519222 | 2018 | 10 صفحه PDF | دانلود رایگان |
عنوان انگلیسی مقاله ISI
Experimental investigations on wiper inserts' edge preparation, workpiece hardness and operating parameters in hard turning of AISI D2 steel
دانلود مقاله + سفارش ترجمه
دانلود مقاله ISI انگلیسی
رایگان برای ایرانیان
موضوعات مرتبط
مهندسی و علوم پایه
سایر رشته های مهندسی
مهندسی صنعتی و تولید
پیش نمایش صفحه اول مقاله
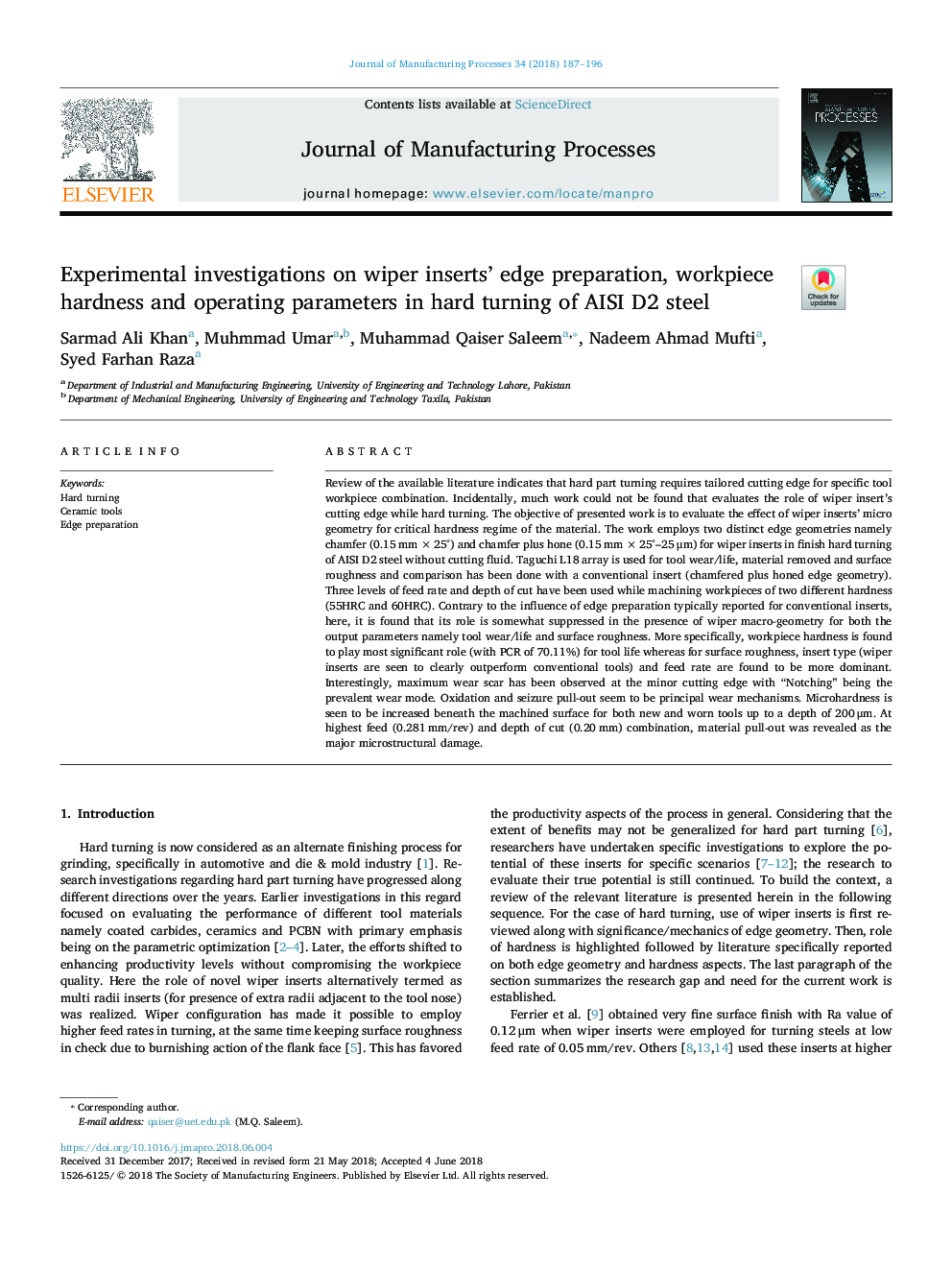
چکیده انگلیسی
Review of the available literature indicates that hard part turning requires tailored cutting edge for specific tool workpiece combination. Incidentally, much work could not be found that evaluates the role of wiper insert's cutting edge while hard turning. The objective of presented work is to evaluate the effect of wiper inserts' micro geometry for critical hardness regime of the material. The work employs two distinct edge geometries namely chamfer (0.15â¯mmâ¯Ãâ¯25°) and chamfer plus hone (0.15â¯mmâ¯Ãâ¯25°-25â¯Î¼m) for wiper inserts in finish hard turning of AISI D2 steel without cutting fluid. Taguchi L18 array is used for tool wear/life, material removed and surface roughness and comparison has been done with a conventional insert (chamfered plus honed edge geometry). Three levels of feed rate and depth of cut have been used while machining workpieces of two different hardness (55HRC and 60HRC). Contrary to the influence of edge preparation typically reported for conventional inserts, here, it is found that its role is somewhat suppressed in the presence of wiper macro-geometry for both the output parameters namely tool wear/life and surface roughness. More specifically, workpiece hardness is found to play most significant role (with PCR of 70.11%) for tool life whereas for surface roughness, insert type (wiper inserts are seen to clearly outperform conventional tools) and feed rate are found to be more dominant. Interestingly, maximum wear scar has been observed at the minor cutting edge with “Notching” being the prevalent wear mode. Oxidation and seizure pull-out seem to be principal wear mechanisms. Microhardness is seen to be increased beneath the machined surface for both new and worn tools up to a depth of 200â¯Î¼m. At highest feed (0.281â¯mm/rev) and depth of cut (0.20â¯mm) combination, material pull-out was revealed as the major microstructural damage.
ناشر
Database: Elsevier - ScienceDirect (ساینس دایرکت)
Journal: Journal of Manufacturing Processes - Volume 34, Part A, August 2018, Pages 187-196
Journal: Journal of Manufacturing Processes - Volume 34, Part A, August 2018, Pages 187-196
نویسندگان
Sarmad Ali Khan, Muhammad Umar, Muhammad Qaiser Saleem, Nadeem Ahmad Mufti, Syed Farhan Raza,