کد مقاله | کد نشریه | سال انتشار | مقاله انگلیسی | نسخه تمام متن |
---|---|---|---|---|
829800 | 1470344 | 2014 | 8 صفحه PDF | دانلود رایگان |
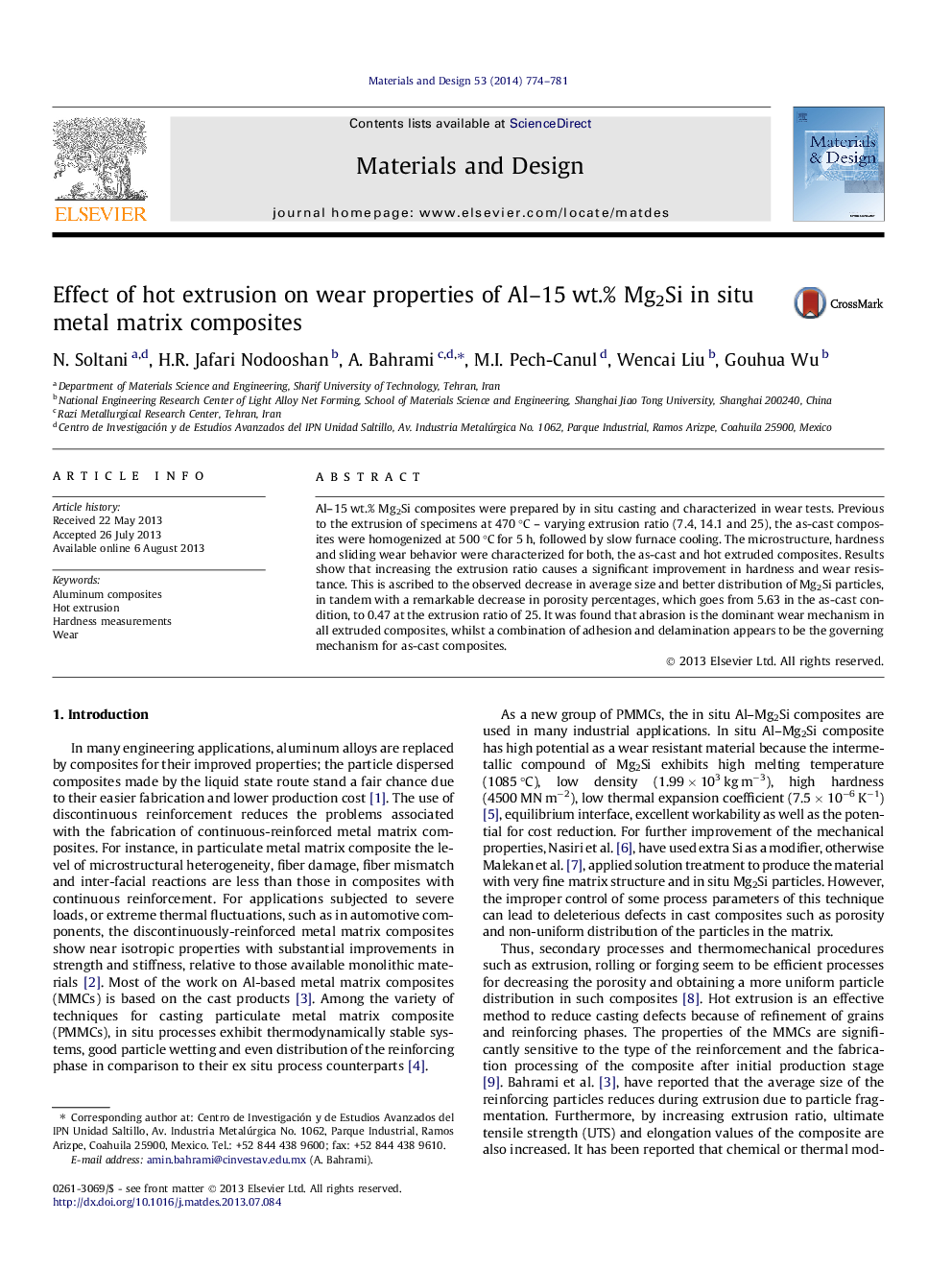
• Increasing the extrusion ratio, enhanced the hardness of the composites.
• Extrusion process led to a significant improvement in wear resistance.
• Wear rate of the composites increased with changing the applied load from 10 to 20 N.
• The dominant wear mechanisms of the extruded composites found to be abrasive.
Al–15 wt.% Mg2Si composites were prepared by in situ casting and characterized in wear tests. Previous to the extrusion of specimens at 470 °C – varying extrusion ratio (7.4, 14.1 and 25), the as-cast composites were homogenized at 500 °C for 5 h, followed by slow furnace cooling. The microstructure, hardness and sliding wear behavior were characterized for both, the as-cast and hot extruded composites. Results show that increasing the extrusion ratio causes a significant improvement in hardness and wear resistance. This is ascribed to the observed decrease in average size and better distribution of Mg2Si particles, in tandem with a remarkable decrease in porosity percentages, which goes from 5.63 in the as-cast condition, to 0.47 at the extrusion ratio of 25. It was found that abrasion is the dominant wear mechanism in all extruded composites, whilst a combination of adhesion and delamination appears to be the governing mechanism for as-cast composites.
Journal: Materials & Design - Volume 53, January 2014, Pages 774–781