کد مقاله | کد نشریه | سال انتشار | مقاله انگلیسی | نسخه تمام متن |
---|---|---|---|---|
829809 | 1470346 | 2013 | 8 صفحه PDF | دانلود رایگان |
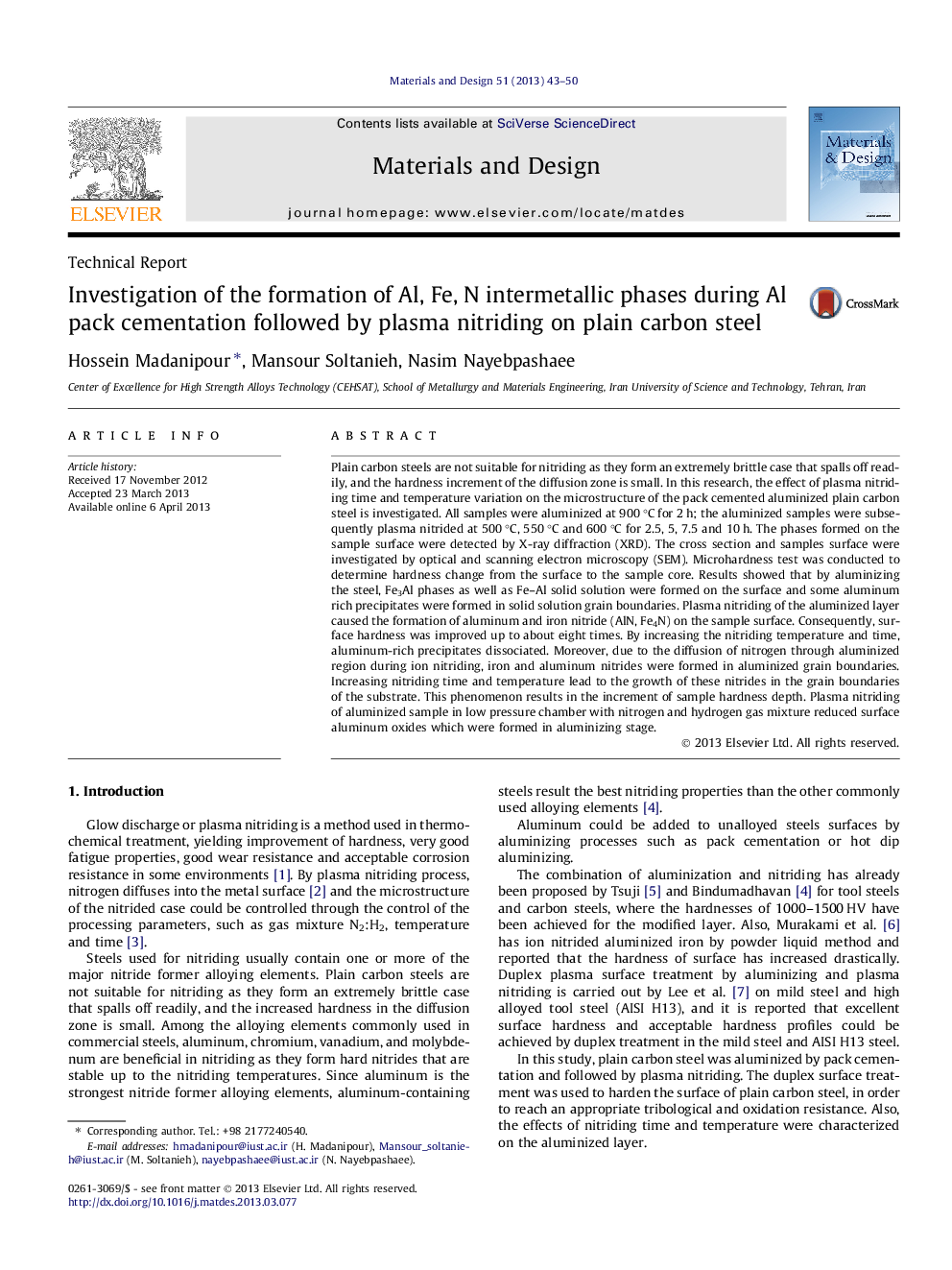
• The surface hardness is increased about eight times.
• Increasing nitriding time and temperature caused strengthening the Al diffused zone.
• The inward diffusion of nitrogen and outward diffusion of iron changed aluminized zone microstructure.
• Surface aluminum oxides are reduced by plasma nitriding in low pressure chamber with nitrogen and hydrogen in gas mixture.
Plain carbon steels are not suitable for nitriding as they form an extremely brittle case that spalls off readily, and the hardness increment of the diffusion zone is small. In this research, the effect of plasma nitriding time and temperature variation on the microstructure of the pack cemented aluminized plain carbon steel is investigated. All samples were aluminized at 900 °C for 2 h; the aluminized samples were subsequently plasma nitrided at 500 °C, 550 °C and 600 °C for 2.5, 5, 7.5 and 10 h. The phases formed on the sample surface were detected by X-ray diffraction (XRD). The cross section and samples surface were investigated by optical and scanning electron microscopy (SEM). Microhardness test was conducted to determine hardness change from the surface to the sample core. Results showed that by aluminizing the steel, Fe3Al phases as well as Fe–Al solid solution were formed on the surface and some aluminum rich precipitates were formed in solid solution grain boundaries. Plasma nitriding of the aluminized layer caused the formation of aluminum and iron nitride (AlN, Fe4N) on the sample surface. Consequently, surface hardness was improved up to about eight times. By increasing the nitriding temperature and time, aluminum-rich precipitates dissociated. Moreover, due to the diffusion of nitrogen through aluminized region during ion nitriding, iron and aluminum nitrides were formed in aluminized grain boundaries. Increasing nitriding time and temperature lead to the growth of these nitrides in the grain boundaries of the substrate. This phenomenon results in the increment of sample hardness depth. Plasma nitriding of aluminized sample in low pressure chamber with nitrogen and hydrogen gas mixture reduced surface aluminum oxides which were formed in aluminizing stage.
Journal: Materials & Design - Volume 51, October 2013, Pages 43–50