کد مقاله | کد نشریه | سال انتشار | مقاله انگلیسی | نسخه تمام متن |
---|---|---|---|---|
830826 | 1470361 | 2012 | 9 صفحه PDF | دانلود رایگان |
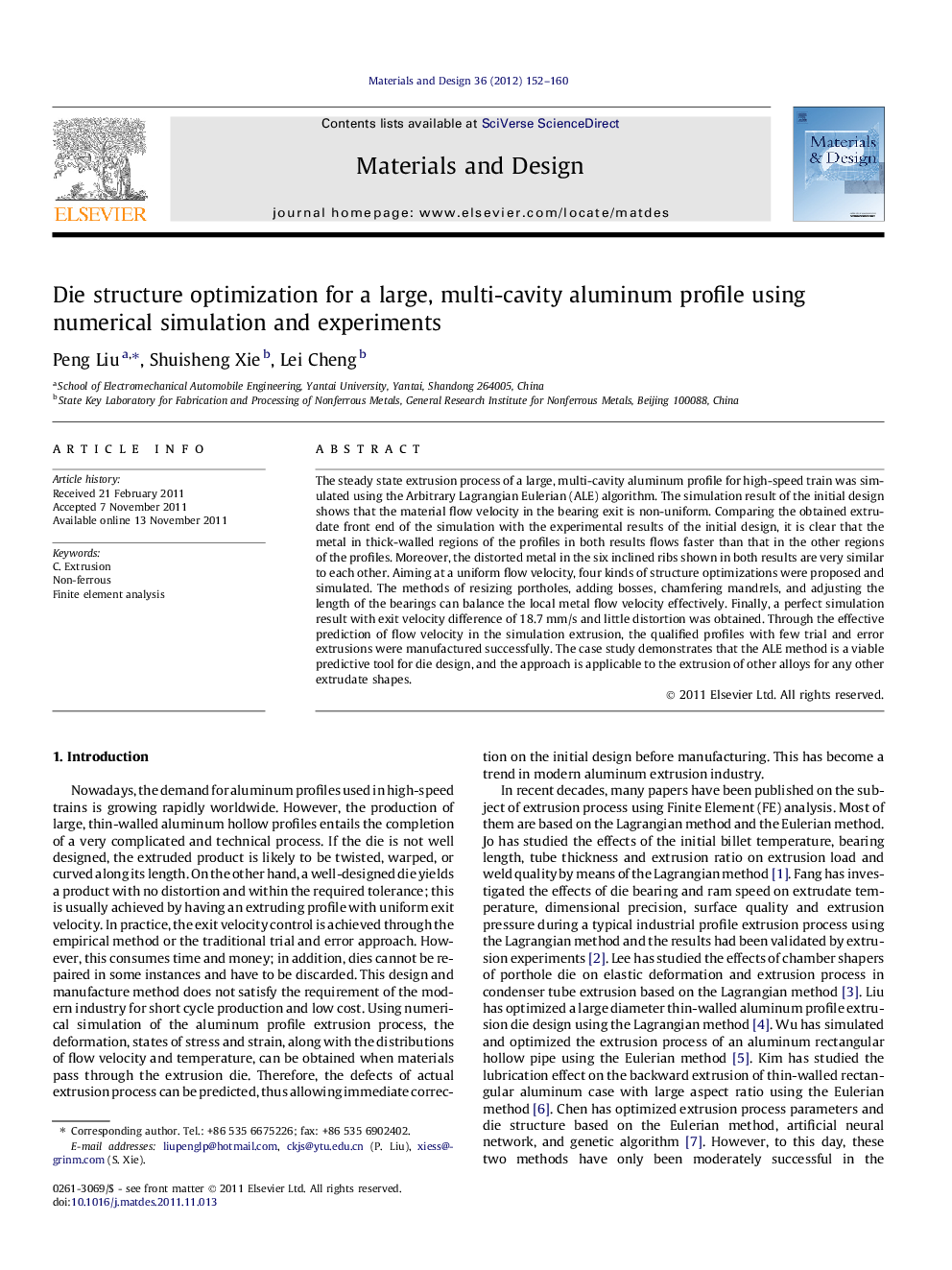
The steady state extrusion process of a large, multi-cavity aluminum profile for high-speed train was simulated using the Arbitrary Lagrangian Eulerian (ALE) algorithm. The simulation result of the initial design shows that the material flow velocity in the bearing exit is non-uniform. Comparing the obtained extrudate front end of the simulation with the experimental results of the initial design, it is clear that the metal in thick-walled regions of the profiles in both results flows faster than that in the other regions of the profiles. Moreover, the distorted metal in the six inclined ribs shown in both results are very similar to each other. Aiming at a uniform flow velocity, four kinds of structure optimizations were proposed and simulated. The methods of resizing portholes, adding bosses, chamfering mandrels, and adjusting the length of the bearings can balance the local metal flow velocity effectively. Finally, a perfect simulation result with exit velocity difference of 18.7 mm/s and little distortion was obtained. Through the effective prediction of flow velocity in the simulation extrusion, the qualified profiles with few trial and error extrusions were manufactured successfully. The case study demonstrates that the ALE method is a viable predictive tool for die design, and the approach is applicable to the extrusion of other alloys for any other extrudate shapes.
Figure optionsDownload as PowerPoint slideHighlights
► A 586.4 mm wide multi-cavity aluminum profile for high-speed train was simulated.
► An experimental extrudate front end was obtained.
► We compare the simulation with the experiment results of the initial design.
► We resize portholes, add bosses, chamfer mandrels and adjust bearing length.
► A result with almost the same exit velocity and little distortion was obtained.
Journal: Materials & Design (1980-2015) - Volume 36, April 2012, Pages 152–160