کد مقاله | کد نشریه | سال انتشار | مقاله انگلیسی | نسخه تمام متن |
---|---|---|---|---|
831222 | 1470365 | 2011 | 12 صفحه PDF | دانلود رایگان |
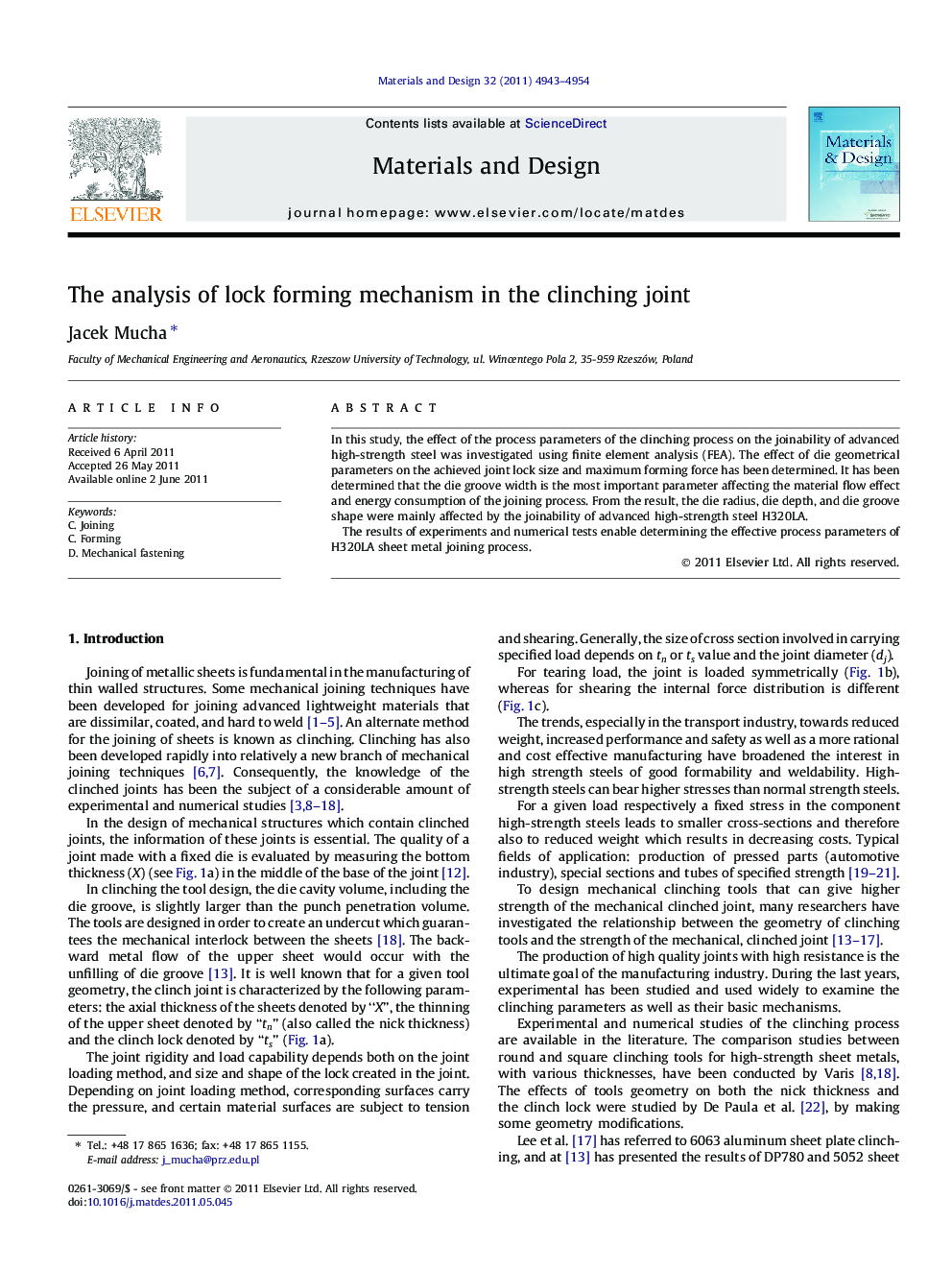
In this study, the effect of the process parameters of the clinching process on the joinability of advanced high-strength steel was investigated using finite element analysis (FEA). The effect of die geometrical parameters on the achieved joint lock size and maximum forming force has been determined. It has been determined that the die groove width is the most important parameter affecting the material flow effect and energy consumption of the joining process. From the result, the die radius, die depth, and die groove shape were mainly affected by the joinability of advanced high-strength steel H320LA.The results of experiments and numerical tests enable determining the effective process parameters of H320LA sheet metal joining process.
Graphs showing the numerical experiments are conducted in order to investigate the effects of tool geometrical parameters on two quality criteria: the nick thickness denoted (tn), the clinch lock (ts) and the maximum forming force, denoted (Pmax). Five models other simulations were then performed, each one involving a type of geometry change in the die or punch, as described in Figures. For previously specified tool geometry (basic model), the joint forming test were performed for various bottom thickness X values.Figure optionsDownload as PowerPoint slideHighlights
► The joint strength is influenced by the size of joint lock.
► The tool geometry and the final value of X influence the size lock significantly.
► Decreasing the X value of joint requires increasing the forming force.
► The specified tool geometry enables achieving the large lock and relatively low forming force.
Journal: Materials & Design - Volume 32, Issue 10, December 2011, Pages 4943–4954