کد مقاله | کد نشریه | سال انتشار | مقاله انگلیسی | نسخه تمام متن |
---|---|---|---|---|
1467083 | 990087 | 2010 | 9 صفحه PDF | دانلود رایگان |
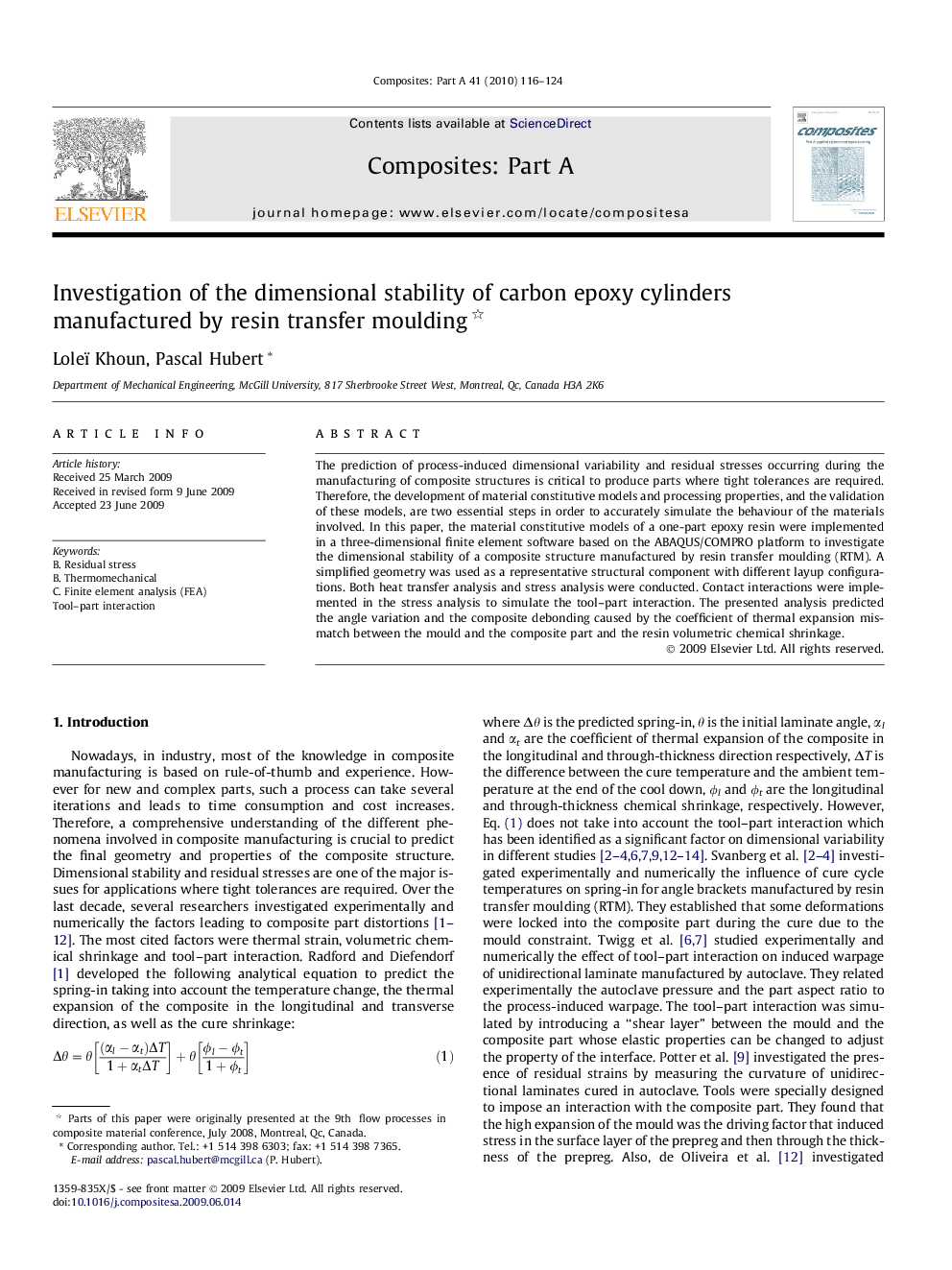
The prediction of process-induced dimensional variability and residual stresses occurring during the manufacturing of composite structures is critical to produce parts where tight tolerances are required. Therefore, the development of material constitutive models and processing properties, and the validation of these models, are two essential steps in order to accurately simulate the behaviour of the materials involved. In this paper, the material constitutive models of a one-part epoxy resin were implemented in a three-dimensional finite element software based on the ABAQUS/COMPRO platform to investigate the dimensional stability of a composite structure manufactured by resin transfer moulding (RTM). A simplified geometry was used as a representative structural component with different layup configurations. Both heat transfer analysis and stress analysis were conducted. Contact interactions were implemented in the stress analysis to simulate the tool–part interaction. The presented analysis predicted the angle variation and the composite debonding caused by the coefficient of thermal expansion mismatch between the mould and the composite part and the resin volumetric chemical shrinkage.
Journal: Composites Part A: Applied Science and Manufacturing - Volume 41, Issue 1, January 2010, Pages 116–124