کد مقاله | کد نشریه | سال انتشار | مقاله انگلیسی | نسخه تمام متن |
---|---|---|---|---|
1467925 | 990123 | 2006 | 13 صفحه PDF | دانلود رایگان |
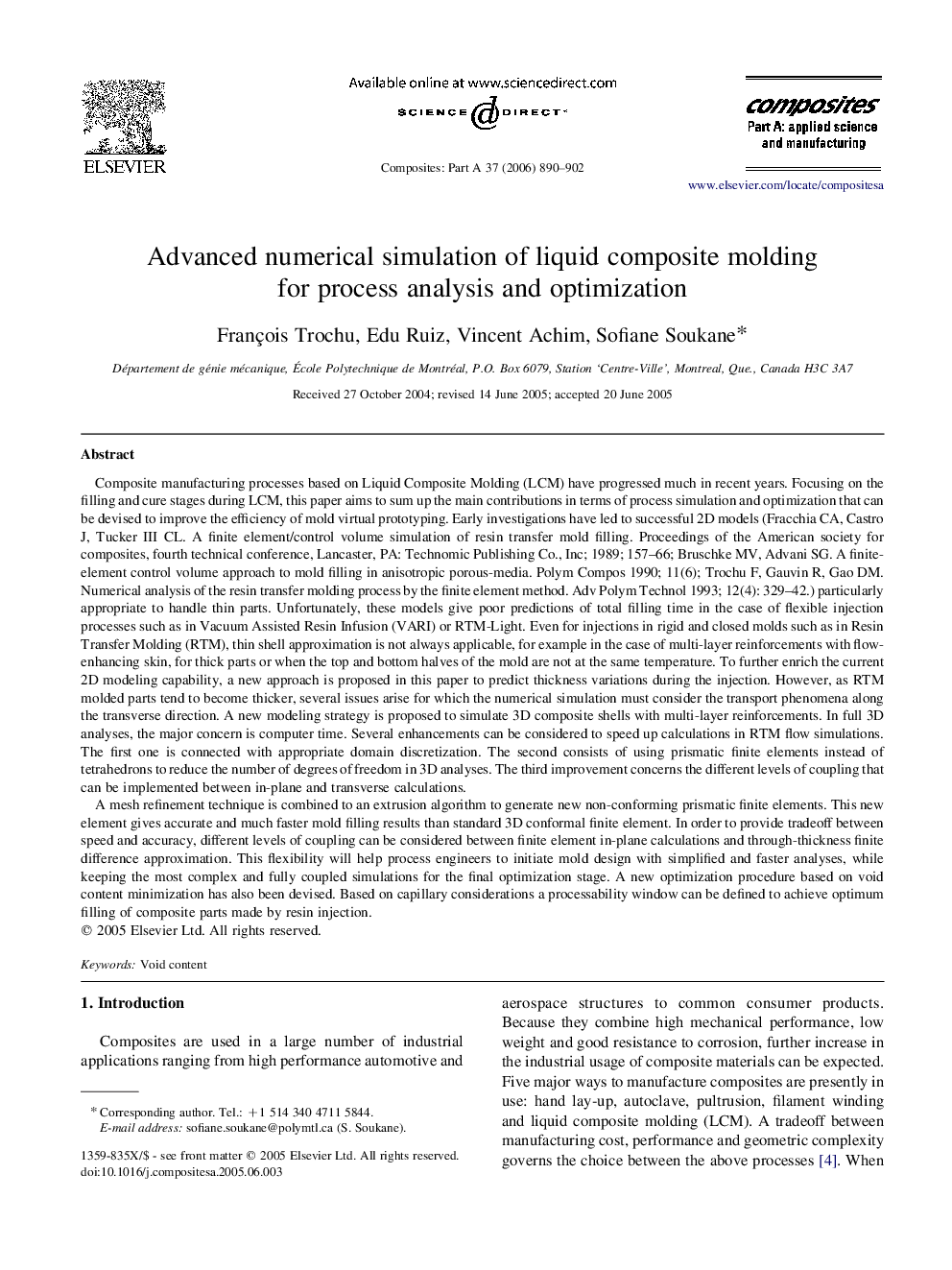
Composite manufacturing processes based on Liquid Composite Molding (LCM) have progressed much in recent years. Focusing on the filling and cure stages during LCM, this paper aims to sum up the main contributions in terms of process simulation and optimization that can be devised to improve the efficiency of mold virtual prototyping. Early investigations have led to successful 2D models (Fracchia CA, Castro J, Tucker III CL. A finite element/control volume simulation of resin transfer mold filling. Proceedings of the American society for composites, fourth technical conference, Lancaster, PA: Technomic Publishing Co., Inc; 1989; 157–66; Bruschke MV, Advani SG. A finite-element control volume approach to mold filling in anisotropic porous-media. Polym Compos 1990; 11(6); Trochu F, Gauvin R, Gao DM. Numerical analysis of the resin transfer molding process by the finite element method. Adv Polym Technol 1993; 12(4): 329–42.) particularly appropriate to handle thin parts. Unfortunately, these models give poor predictions of total filling time in the case of flexible injection processes such as in Vacuum Assisted Resin Infusion (VARI) or RTM-Light. Even for injections in rigid and closed molds such as in Resin Transfer Molding (RTM), thin shell approximation is not always applicable, for example in the case of multi-layer reinforcements with flow-enhancing skin, for thick parts or when the top and bottom halves of the mold are not at the same temperature. To further enrich the current 2D modeling capability, a new approach is proposed in this paper to predict thickness variations during the injection. However, as RTM molded parts tend to become thicker, several issues arise for which the numerical simulation must consider the transport phenomena along the transverse direction. A new modeling strategy is proposed to simulate 3D composite shells with multi-layer reinforcements. In full 3D analyses, the major concern is computer time. Several enhancements can be considered to speed up calculations in RTM flow simulations. The first one is connected with appropriate domain discretization. The second consists of using prismatic finite elements instead of tetrahedrons to reduce the number of degrees of freedom in 3D analyses. The third improvement concerns the different levels of coupling that can be implemented between in-plane and transverse calculations.A mesh refinement technique is combined to an extrusion algorithm to generate new non-conforming prismatic finite elements. This new element gives accurate and much faster mold filling results than standard 3D conformal finite element. In order to provide tradeoff between speed and accuracy, different levels of coupling can be considered between finite element in-plane calculations and through-thickness finite difference approximation. This flexibility will help process engineers to initiate mold design with simplified and faster analyses, while keeping the most complex and fully coupled simulations for the final optimization stage. A new optimization procedure based on void content minimization has also been devised. Based on capillary considerations a processability window can be defined to achieve optimum filling of composite parts made by resin injection.
Journal: Composites Part A: Applied Science and Manufacturing - Volume 37, Issue 6, June 2006, Pages 890–902