کد مقاله | کد نشریه | سال انتشار | مقاله انگلیسی | نسخه تمام متن |
---|---|---|---|---|
1475612 | 991123 | 2010 | 6 صفحه PDF | دانلود رایگان |
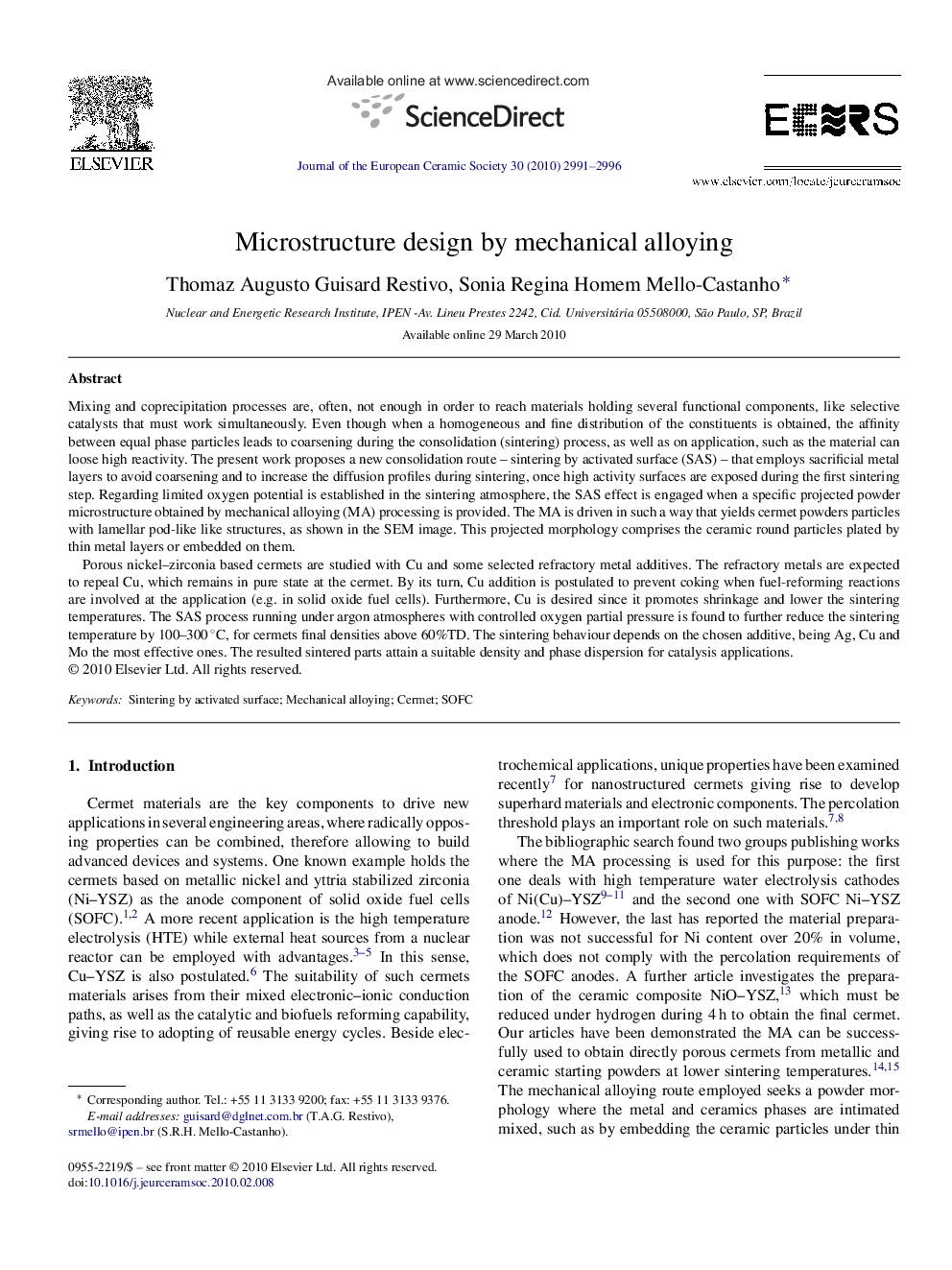
Mixing and coprecipitation processes are, often, not enough in order to reach materials holding several functional components, like selective catalysts that must work simultaneously. Even though when a homogeneous and fine distribution of the constituents is obtained, the affinity between equal phase particles leads to coarsening during the consolidation (sintering) process, as well as on application, such as the material can loose high reactivity. The present work proposes a new consolidation route – sintering by activated surface (SAS) – that employs sacrificial metal layers to avoid coarsening and to increase the diffusion profiles during sintering, once high activity surfaces are exposed during the first sintering step. Regarding limited oxygen potential is established in the sintering atmosphere, the SAS effect is engaged when a specific projected powder microstructure obtained by mechanical alloying (MA) processing is provided. The MA is driven in such a way that yields cermet powders particles with lamellar pod-like like structures, as shown in the SEM image. This projected morphology comprises the ceramic round particles plated by thin metal layers or embedded on them.Porous nickel–zirconia based cermets are studied with Cu and some selected refractory metal additives. The refractory metals are expected to repeal Cu, which remains in pure state at the cermet. By its turn, Cu addition is postulated to prevent coking when fuel-reforming reactions are involved at the application (e.g. in solid oxide fuel cells). Furthermore, Cu is desired since it promotes shrinkage and lower the sintering temperatures. The SAS process running under argon atmospheres with controlled oxygen partial pressure is found to further reduce the sintering temperature by 100–300 °C, for cermets final densities above 60%TD. The sintering behaviour depends on the chosen additive, being Ag, Cu and Mo the most effective ones. The resulted sintered parts attain a suitable density and phase dispersion for catalysis applications.
Journal: Journal of the European Ceramic Society - Volume 30, Issue 14, October 2010, Pages 2991–2996